摩擦を減らす!POM部品設計のための実践ガイド
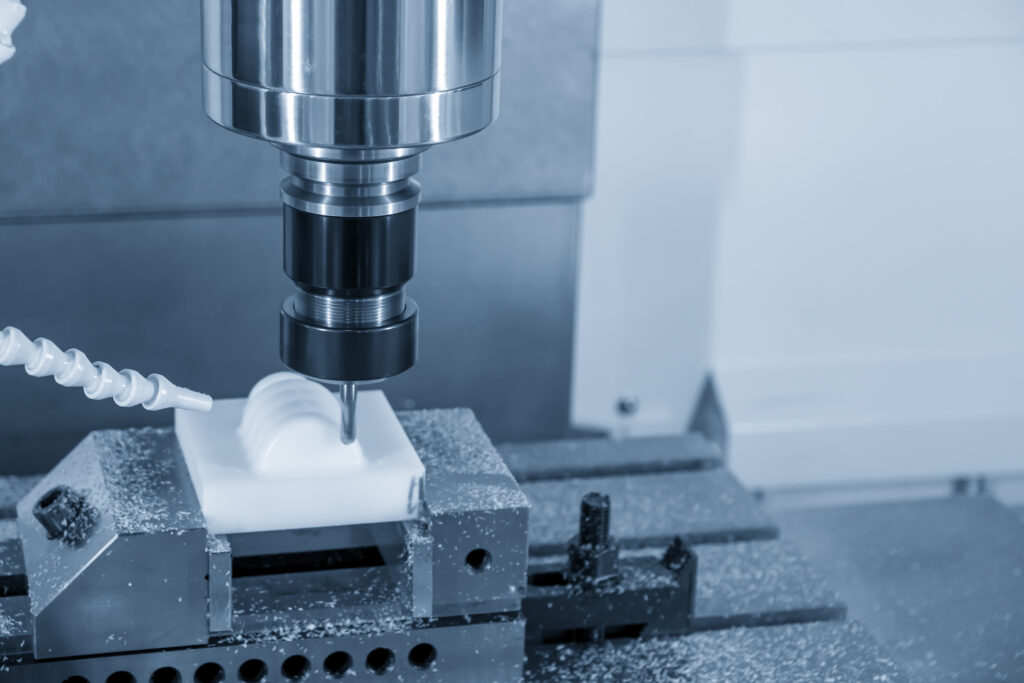
POM(ポリアセタール)は、その優れた物理的特性から、さまざまな産業で利用されていますが、設計の段階で摩擦をいかに低減するかが、部品の性能や耐久性に大きく影響します。「摩擦を減らしたいけれど、具体的にどうすればいいのだろう?」と悩んでいる方も多いのではないでしょうか。
このガイドは、POM部品設計における摩擦低減のテクニックや実践的なアプローチを詳しく説明します。摩擦のメカニズムを理解し、最適な材料や形状の選択、加工方法に至るまで、幅広く解説します。特に、これからPOM部品の設計に挑戦する方々や、摩擦を軽減してより高性能な製品を実現したいと考えているエンジニアにとって、非常に役立つ内容となっています。
摩擦を減らすことがどれほど製品の信頼性に寄与するか、一緒に探っていきましょう。このガイドを通じて、POM部品設計の新たな幕開けを迎えてみませんか?
1. POM部品設計摩擦低減の基本知識
1-1. POMとは何か
POM(ポリアセタール、Polyoxymethylene)は、優れた機械的強度と耐摩耗性を持つエンジニアリングプラスチックの一種です。結晶性の高い熱可塑性樹脂であり、硬さや剛性に優れ、自動車部品、機械部品、電子機器など幅広い分野で利用されています。特徴としては、低摩擦係数、良好な耐疲労性、高い耐薬品性が挙げられ、特に摺動部品やギア、軸受けなど摩擦が問題となる用途に適しています。
1-2. 摩擦低減の重要性
摩擦は部品の摩耗や発熱を引き起こし、機械の効率低下や故障の原因になります。POM部品においても摩擦を適切に制御することは、部品寿命の延長やメンテナンスコストの削減に直結します。特に高回転や高負荷条件下では摩擦による損失が大きくなるため、設計段階から摩擦低減を意識した対策を講じることが必要です。摩擦低減は、エネルギー消費の削減や騒音低減にも貢献します。
2. POM部品設計摩擦低減のための設計方法
2-1. 摩耗を抑えるための設計ポイント
POM部品の摩耗を抑えるためには、部品形状や表面仕上げ、潤滑条件を考慮した設計が重要です。まず、摩擦が集中しやすい接触面は可能な限り平滑に仕上げることが摩耗低減に効果的です。表面粗さを抑えることで接触面の局所的な圧力が減り、摩擦熱の発生を防ぎます。
また、荷重分散を図るために接触面積を適切に設計し、過大な応力集中を避けることも摩耗軽減に寄与します。例えば、シャフトや軸受けの形状にフィレットを入れるなど、応力集中点の緩和が推奨されます。さらに、部品同士の相対速度や摺動距離を設計段階で考慮し、過度な摩擦発生を防ぐことも効果的です。
2-2. 摩擦係数を考慮した設計技術
摩擦係数は材料の種類、表面状態、潤滑条件によって大きく変わります。POMの摩擦係数は金属に比べて低いものの、相手材や環境に応じて変動するため、設計時には使用環境を踏まえた摩擦係数の見積もりが必要です。
例えば、POMと金属の接触では摩擦係数が比較的低く安定しますが、POM同士やPOMとゴムの接触では摩擦係数が上昇しやすい傾向があります。また、湿潤状態や潤滑剤の有無によっても摩擦係数は大きく変わるため、実運用条件に合わせた摩擦試験の実施が望ましいです。
設計段階では、摩擦係数を元に接触応力や摩耗量を解析し、必要に応じて表面処理や潤滑設計を組み込むことが摩擦低減に効果的です。
3. POM部品設計摩擦低減における加工精度の向上
3-1. 加工精度向上のための品質管理
POM部品の摩擦低減には加工精度の向上が欠かせません。寸法公差や表面粗さの管理を徹底し、設計通りの部品精度を確保することで、部品同士の隙間や摩擦面の適合性が向上し、無駄な摩擦や摩耗を防ぎます。
具体的には、CNC加工や精密成形の工程で定期的な寸法検査、表面状態の確認を実施します。また、加工工具の摩耗管理や機械のメンテナンスを通じて加工安定性を維持することも重要です。品質管理体制の強化により、加工誤差のばらつきを抑え、製品の一貫性を高めることが摩擦低減に直結します。
3-2. 精度が摩擦に与える影響
加工精度が低いと、部品間のクリアランスが不適切になり、摩擦力が増加します。隙間が大きすぎると振動や摩耗が激しくなり、小さすぎると過剰な接触圧がかかり摩擦熱や早期摩耗を引き起こします。
したがって、適切な寸法精度を保つことは摩擦を適正化する上で非常に重要です。表面粗さも摩擦に影響し、粗い面は摩擦抵抗が大きくなりやすいので、加工後の研磨や表面処理を検討することが推奨されます。
4. POM部品設計摩擦低減と強度の関係
4-1. 強度を最大限に引き出す設計方法
POMは機械的強度に優れていますが、摩擦低減を優先するあまり強度を犠牲にしてはいけません。強度と摩擦のバランスを取るためには、部品の厚みや補強リブを適切に設計し、応力集中を回避することが大切です。
また、フィレットや面取り加工を施すことで応力集中点を減少させ、割れや亀裂の発生を防ぎます。こうした設計手法は、摩擦による局所的な熱や摩耗にも耐えうる強度を確保しつつ、全体の性能を維持します。
4-2. 摩擦と強度のバランスを考える
摩擦低減のために潤滑や表面処理を導入すると、強度や耐久性に影響を与えることがあります。例えば、硬度を上げるためのコーティングは摩擦を減らす効果がある一方で、割れやすさが増す場合もあります。
そのため、摩擦低減策を検討する際は、強度試験や耐久試験を併用して、最適なバランスを探ることが必要です。設計段階で強度と摩擦の両面から評価を行い、必要に応じて材料の選択や加工方法を調整します。
5. POM部品設計摩擦低減における材料選定
5-1. POMとMCナイロンの特性比較
POMとMCナイロン(モディファイドナイロン)はどちらも摩擦低減に適したエンジニアリングプラスチックですが、特性には違いがあります。
POMは硬くて耐摩耗性に優れ、低摩擦係数で摺動部品に適しています。一方、MCナイロンは柔軟性と耐衝撃性に優れ、耐熱性や吸水性もPOMより高い傾向にあります。摩擦係数はややPOMより高い場合がありますが、潤滑条件が良ければ問題ありません。
用途や使用環境に応じて、荷重や衝撃、温度、耐薬品性などの観点から適切な材料を選定することが重要です。
5-2. 適切な材料の選び方
摩擦低減を目的とする場合、まずPOMの特性を最大限活かせる設計を検討しますが、使用環境が厳しい場合や吸水による寸法変化が問題となる場合はMCナイロンを検討します。
また、耐摩耗性と強度、耐熱性、コストのバランスを考慮して材料を選択し、試作や評価を重ねて最適解を見つけることが望ましいです。
まとめ
POM部品設計において摩擦を減らすための実践ガイドでは、材料特性や表面処理、潤滑方法の選定が重要です。適切な設計と加工技術を用いることで、耐久性や性能を向上させ、効率的な機械運動を実現します。これにより、部品の寿命延長とメンテナンスコストの削減が期待できます。