エンジニアリングプラスチック徹底比較!種類と特性を一覧で理解しよう
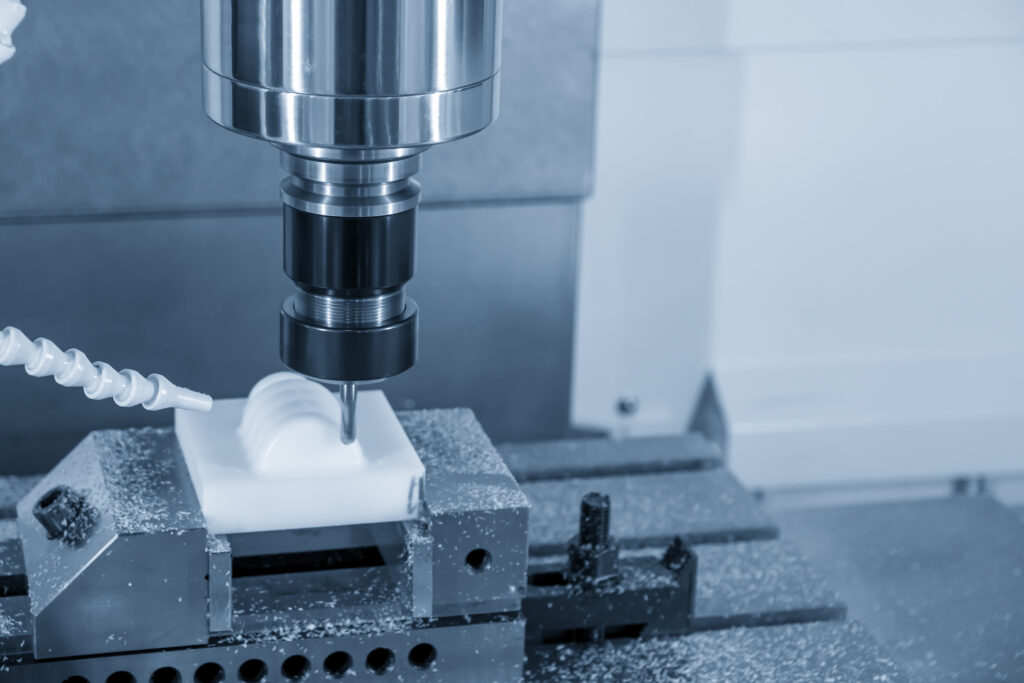
エンジニアリングプラスチックは、幅広い産業分野で重要な役割を果たしています。機械部品から電子機器まで、さまざまな製品に利用されており、その特性や適用範囲を正しく理解することが重要です。本記事では、エンジニアリングプラスチックの種類や特性を詳細に比較し、それぞれの特長や用途について解説していきます。エンジニアリングプラスチックに関心がある方や製品開発に携わる方々にとって、役立つ情報が満載です。さあ、エンジニアリングプラスチックの世界に深く入り込み、その魅力を探ってみましょう。
Contents
エンジニアリングプラスチックの基礎知識
エンジニアリングプラスチックとは
エンジニアリングプラスチックは、機械的特性や熱的特性が優れたプラスチック材料で、特に高強度、高耐熱性、耐薬品性、耐摩耗性を要求されるアプリケーションに使用されます。一般的なプラスチック材料よりも高性能で、金属に匹敵する性能を持つため、機械部品や自動車部品、電気機器、航空機など、幅広い産業で活用されています。 これらのプラスチックは、高温や高負荷環境においても安定して機能し、耐久性や安全性を向上させることができます。エンジニアリングプラスチックの例としては、ポリカーボネート(PC)、ポリフェニレンサルファイド(PPS)、ポリアミド(PA)、ポリテトラフルオロエチレン(PTFE)などがあります。一般プラスチックとの違い
エンジニアリングプラスチックと一般プラスチックの主な違いは、性能面での違いです。一般的なプラスチック(たとえばポリエチレンやポリプロピレン)は、低価格で加工が容易ですが、耐熱性や強度が低く、厳しい環境下では使用が難しいことがあります。 一方で、エンジニアリングプラスチックは、強度や耐熱性、化学耐性が高いため、長期間の使用にも耐え、過酷な条件でも安定した性能を発揮します。そのため、エンジニアリングプラスチックは、精密機器や自動車、航空機、医療機器など、特定の要件が厳しいアプリケーションに利用されています。エンジニアリングプラスチックの歴史
エンジニアリングプラスチックは、1950年代から1960年代にかけての化学技術の進歩により、登場しました。それまでのプラスチックは、比較的軽量で簡単な用途に使われていたため、強度や耐久性に限界がありました。しかし、新しい材料開発が進み、エンジニアリングプラスチックはその高性能が認められ、より高度な技術の要求を満たすために使用されるようになりました。 最初のエンジニアリングプラスチックの一例は、ナイロン(ポリアミド)で、耐摩耗性や耐熱性が優れていることから、機械部品に利用されました。その後、ポリカーボネート(PC)、ポリフェニレンサルファイド(PPS)、ポリテトラフルオロエチレン(PTFE)などの新しい材料が次々と開発され、これらは現在でも多くの産業で使用されています。 エンジニアリングプラスチックは、今後も新しい技術革新に伴い、さらに性能が向上し、より多くの分野での利用が期待されています。エンジニアリングプラスチックの種類と特性の比較
主要なエンジニアリングプラスチックの種類
エンジニアリングプラスチックには、さまざまな種類がありますが、以下が代表的なものです:- ポリカーボネート(PC)
- ポリアミド(PA)(ナイロン)
- ポリフェニレンサルファイド(PPS)
- ポリテトラフルオロエチレン(PTFE)
- ポリフッ化ビニリデン(PVDF)
- ポリエーテルエーテルケトン(PEEK)
- ポリエチレンテレフタレート(PET)
各種類の特性と比較
物理的特性の概要
- ポリカーボネート(PC):高い衝撃強度を持つ、透明で硬度もあり、良好な光透過性を有します。
- ポリアミド(PA):良好な摩耗性、強度、弾力性を持ち、耐摩耗部品や機械部品に適します。吸湿性が高く、湿気に敏感です。
- ポリフェニレンサルファイド(PPS):高い強度と剛性を持ち、高温下でも優れた性能を発揮します。化学薬品に非常に耐性が高いです。
- ポリテトラフルオロエチレン(PTFE):低摩擦係数、高耐熱性、化学耐性に優れており、主にシール材や摺動部品に使用されます。
- ポリエチレンテレフタレート(PET):軽量で強度も高く、食品包装材料やフィラメントなどに多く使用されます。
熱的特性の概要
- ポリカーボネート(PC):優れた耐熱性を持ち、約120〜130℃程度までの高温でも使用可能ですが、高温環境では変形することがあります。
- ポリアミド(PA):熱可塑性が高く、ナイロン系は一般に150℃程度の温度に耐えることができます。高温時に吸湿により寸法安定性に影響を与えることがあります。
- ポリフェニレンサルファイド(PPS):非常に高い耐熱性(300℃以上)を持ち、熱安定性が必要な環境で使用されます。
- ポリテトラフルオロエチレン(PTFE):非常に高い耐熱性を持ち、250℃を超える温度での使用にも適しています。
- ポリエチレンテレフタレート(PET):耐熱性に優れ、約150〜200℃で使用されることが一般的です。
化学的特性の概要
- ポリカーボネート(PC):耐薬品性は限定的で、強酸やアルカリには弱いですが、一般的な溶剤や油分には比較的強い耐性を示します。
- ポリアミド(PA):油や燃料、脂肪に対する耐性が良好ですが、酸やアルカリにはやや弱いです。
- ポリフェニレンサルファイド(PPS):非常に高い耐薬品性を持ち、強酸やアルカリにも耐性があります。腐食性環境での使用に最適です。
- ポリテトラフルオロエチレン(PTFE):ほぼすべての化学薬品に耐性があり、非常に広範な化学環境で使用可能です。
- ポリエチレンテレフタレート(PET):多くの化学薬品に耐性を持つが、強酸や高温での酸化に弱いです。
エンジニアリングプラスチックの選定基準
特性に基づく選定基準
エンジニアリングプラスチック(エンプラ)を選定する際、まず考慮すべきはその物理的、化学的、熱的特性です。選定基準として重要なポイントは以下の通りです。- 機械的強度:使用環境で必要な強度や剛性を維持できるかどうか。例えば、耐荷重性が重要な部品には強度が高いエンプラ(ポリフェニレンサルファイド(PPS)やポリカーボネート(PC)など)が適しています。
- 耐熱性:高温環境での使用が求められる場合、耐熱性の高いエンプラ(ポリエーテルエーテルケトン(PEEK)やポリフェニレンサルファイド(PPS))を選択することが必要です。
- 耐薬品性:化学薬品が接触する可能性がある場合、耐薬品性を重視します。ポリテトラフルオロエチレン(PTFE)は化学薬品に強く、腐食性のある環境でも使用できます。
- 衝撃強度:衝撃を受ける可能性がある場合、衝撃吸収性の高いエンプラ(ポリカーボネート(PC)やポリアミド(PA))が適しています。
- 摩擦係数と耐摩耗性:摩擦や摩耗の影響を受ける部品には、低摩擦係数と高耐摩耗性を持つエンプラ(ポリエチレンテレフタレート(PET)やポリテトラフルオロエチレン(PTFE))を選択します。
用途に応じた最適なエンプラの選び方
エンプラは用途によって求められる特性が異なるため、使用目的に合わせて最適な材料を選ぶことが重要です。以下は代表的な用途に応じたエンプラの選定基準です。- 自動車部品:自動車部品は、耐熱性、強度、衝撃吸収性が求められるため、ポリカーボネート(PC)やポリアミド(PA)が適しています。また、軽量化が求められる場合、ポリテトラフルオロエチレン(PTFE)やポリエーテルエーテルケトン(PEEK)も選ばれることがあります。
- 医療機器:医療機器では、耐薬品性、生体適合性、強度が求められます。ポリエーテルエーテルケトン(PEEK)は医療用インプラントにも使用されることが多いです。また、透明性が必要な部品にはポリカーボネート(PC)が選ばれます。
- 電子機器部品:電子機器部品では、電気絶縁性、耐熱性、衝撃強度が重視されます。ポリエチレンテレフタレート(PET)やポリカーボネート(PC)が適しており、特に高耐久性が求められる部品にはポリフェニレンサルファイド(PPS)も選択肢となります。
- 化学プラント部品:耐薬品性と耐熱性が最も重視される分野です。ポリテトラフルオロエチレン(PTFE)やポリフェニレンサルファイド(PPS)は化学薬品に強く、過酷な環境にも適しています。
- 航空宇宙産業:航空機部品では、高強度、耐熱性、軽量性が要求されるため、ポリエーテルエーテルケトン(PEEK)やポリフェニレンサルファイド(PPS)がよく使用されます。
エンジニアリングプラスチックの環境への影響と持続可能性
エンプラのリサイクルと環境への配慮
エンジニアリングプラスチック(エンプラ)は高性能な材料として多くの産業で利用されていますが、その環境への影響にも注目が集まっています。エンプラのリサイクルは、環境負荷を減らすための重要な取り組みの一つです。リサイクル可能なエンプラを選択することで、使用後の廃棄物を減らし、資源の有効活用ができます。リサイクル方法としては、機械的リサイクル、化学的リサイクル、熱的リサイクルがあり、これらの方法を駆使することで、エンプラの寿命を延ばし、廃棄物の削減に貢献します。- 機械的リサイクル:エンプラを粉砕し、新たな製品に再利用する方法です。特に、ポリエチレンテレフタレート(PET)などの材料はこの方法でリサイクルされています。
- 化学的リサイクル:エンプラを化学的に分解して、新たな原料に戻す方法です。これにより、エンプラを無駄なく再利用することが可能になります。
- 熱的リサイクル:焼却によってエンプラを熱エネルギーに変換する方法ですが、環境負荷を減らすためには最適な設備が必要です。
エンプラの持続可能性と環境保護基準
エンプラの持続可能性は、環境への影響を最小限に抑えるための重要な課題です。エンプラの製造過程では、二酸化炭素の排出、エネルギーの消費、化学物質の使用などが問題となりますが、持続可能性を高めるために、環境に配慮した製造プロセスの導入が進んでいます。 また、エンプラには環境保護基準が設定されており、これを遵守することが求められます。例えば、RoHS指令(有害物質の制限)やREACH規則(化学物質の登録、評価、認可)のような基準があります。これらの規則により、環境に有害な化学物質の使用を制限し、安全で環境負荷の少ない材料を使用することが推奨されています。環境に優しいエンプラの開発動向
環境に優しいエンプラの開発は、今後さらに重要なテーマとなっています。近年では、バイオベースのエンプラや、リサイクル可能なエンプラの開発が進められています。これにより、石油由来の化学物質を減らし、再生可能な資源を活用することが可能になります。- バイオベースエンプラ:植物由来の原料を使用したエンプラで、化石燃料の使用を減らすことができます。例えば、ポリ乳酸(PLA)などのバイオプラスチックが開発され、使用されています。
- リサイクル可能なエンプラ:再生可能なエンプラの開発が進み、廃棄物の削減と資源の有効活用を目指しています。ポリエチレンテレフタレート(PET)のような材料はリサイクル率が高く、環境負荷を減らすことができます。