POM部品の製造コストを削減するためのフライス加工のテクニック
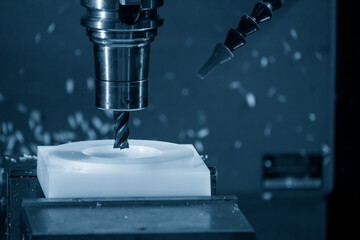
「POM部品の製造コストを削減したいが、どのようなフライス加工技術を使えばよいのか分からない…」そんなお悩みを抱えている方はいませんか?コスト削減は企業にとって至上命題であり、特にPOM(ポリアセタール)部品の生産においては、効率的な加工技術が求められます。そこで本記事では、POM部品の製造コストを抑えるためのフライス加工術について詳しく解説します。
この内容は、次のような方々に役立つものです:
- フライス加工に興味があるが、具体的な方法が知りたい
- POM部品のコスト削減に取り組んでいるが、効率化のアイデアが必要
- 新たな加工技術を導入したいと考えているエンジニアや企業の方
POM部品の製造には多くの要素が関与しますが、フライス加工を適切に活用することで、効率性やコストパフォーマンスを大幅に向上させることが可能です。本記事では、その基本的な概念から具体的なテクニックに至るまで、幅広くお伝えしていきます。あなたの製造プロセスがよりスムーズに進む手助けとなれば幸いです。
1. POM部品の製造コストを抑えるためのフライス加工術
POM(ポリアセタール)は、精密な部品に適した材料であり、軽量で高い機械的特性を持つため、さまざまな製品に利用されています。POM部品を製造する際にコストを抑えることは重要な課題ですが、適切なフライス加工術を採用することで、そのコストを効果的に削減することが可能です。以下は、POM部品の製造コストを抑えるためのフライス加工術について説明します。
1-1. POM部品の製造コストを抑えるための基本的な考え方
- 無駄な材料の削減:
- POM部品の製造コストを抑えるためには、まず材料費を抑えることが重要です。フライス加工時に無駄な部分を削減するために、設計段階で部品の形状を最適化し、切削量を減らすことが有効です。例えば、鋳造や成形である程度の形状を作成してからフライス加工を行うことで、無駄な切削を減らすことができます。
- 加工時間の短縮:
- POM部品の製造には加工時間が重要です。フライス加工での加工時間を短縮するために、適切な切削条件を設定し、無駄な動作を減らすことが求められます。加工速度や送り速度を最適化し、工具の選定を行うことで、加工時間を短縮し、全体的なコスト削減を図ることができます。
- 高い歩留まりの確保:
- 部品の歩留まりを高めることもコスト削減に繋がります。良好な設計と加工条件を選定することで、廃棄や再加工のリスクを減らし、より高い歩留まりを実現することが可能です。
1-2. 効率的な加工プロセスの選定
- フライス加工の最適化:
- フライス加工は、特に複雑な形状や高精度が要求される部品の製造に有効です。しかし、効率的に行うためには、切削条件や工具の選定が非常に重要です。切削条件を最適化し、適切な工具を使用することで、加工効率を大幅に向上させることができます。
- 加工中の冷却液の使用も大きな効果を発揮します。POMは加工中に熱を発生しやすいため、冷却液を適切に使用して熱の発生を抑えることで、精度を保ちつつ、加工効率を向上させることができます。
- 自動化の導入:
- フライス加工の効率化には自動化が効果的です。ロボットアームやCNCフライス盤を使用することで、作業の効率が格段に向上し、加工精度も保たれます。さらに、自動化によって人的ミスの削減や生産性の向上が期待できるため、コスト削減に寄与します。
- プロセスの統合:
- いくつかの加工工程を統合することで、製造工程の段階数を減らし、加工の手間を削減することが可能です。例えば、フライス加工と同時に穴あけやネジ切りを行うことで、加工の一貫性を高めつつ、効率的に部品を仕上げることができます。
1-3. 材料選定の重要性
環境への配慮をしつつコストを削減するために、リサイクルPOMの利用も選択肢として考慮できます。リサイクル材料を使用することで、コストを抑えつつも高い品質を維持することが可能となります。リサイクルPOMは、一般的なPOMの性能を保ちながら、コスト削減に繋がるため、必要に応じて適切な選定を行うことが重要です。
適切な材料の選定:
POM部品の製造において材料選定は非常に重要です。POMのグレードや仕様を選定する際、機械的特性や耐摩耗性を考慮することが必要です。高品質なPOMを使用することにより、加工時の不良や材料ロスを防ぎ、コストを抑えることが可能です。
材料の厚さや種類によって加工が難しくなることもあるため、部品の使用条件に最適な材料を選ぶことが重要です。また、使用する材料の精度が高いほど、加工精度も向上し、後工程での修正が必要なくなります。
材料のロット管理と調達:
材料調達時にロット管理を徹底することで、無駄な材料費を削減することができます。また、まとめて材料を購入することで、仕入れ単価を抑えることも可能です。特に規模が大きい場合には、材料の仕入れ先や仕入れ時期を調整することでコスト削減を実現できます。
リサイクル材料の利用:
環境への配慮をしつつコストを削減するために、リサイクルPOMの利用も選択肢として考慮できます。リサイクル材料を使用することで、コストを抑えつつも高い品質を維持することが可能となります。リサイクルPOMは、一般的なPOMの性能を保ちながら、コスト削減に繋がるため、必要に応じて適切な選定を行うことが重要です。
2. POM材料を効率的に加工するための具体的なテクニック
POM(ポリアセタール)は、優れた機械的特性と滑らかな表面仕上げが特徴で、精密な部品に適しています。しかし、その加工性を最大限に引き出すためには、適切な加工技術を使用することが求められます。以下では、POM材料を効率的に加工するための具体的なテクニックについて説明します。
2-1. フライス加工における最適な切削条件
フライス加工でPOMを処理する際の最適な切削条件は、以下の要素を考慮することが重要です。
- 切削速度:
- POMは比較的柔らかい材料であり、高速での切削が可能です。しかし、あまりにも高速すぎると材料の溶解や焼けが発生する恐れがあります。一般的には、切削速度を約200~500m/minに設定することが推奨されます。これにより、効率的な加工を実現し、表面仕上げも良好に保たれます。
- 送り速度:
- 送り速度も重要な要素で、過度の送り速度は切削効率を低下させ、仕上がりが粗くなる原因となります。送り速度はおおよそ0.1~0.3mm/回転程度に設定し、適切なバランスを保つことが求められます。
- 切削深さ:
- POMのフライス加工においては、切削深さを適度に設定することで工具の摩耗を抑え、仕上がりの精度を向上させることができます。深すぎる切削は、部品の形状精度を損なうことがあるため、浅めの切削を心がけると良いでしょう。
- 冷却液の使用:
- POMは加工中に熱を発生しやすいため、冷却液を使用することで温度上昇を抑え、加工精度と工具寿命を向上させることができます。適切な冷却液を使用し、加工中の温度管理を行うことが効率的な加工を支援します。
2-2. 切削工具の選び方とその影響
POM材料の加工には、適切な切削工具の選定が重要です。以下のポイントを押さえて、最適な工具を選びましょう。
- 工具の材質:
- POMは比較的柔らかいため、一般的な超硬工具(カルバイド)やコーティングされた工具が適しています。これらの工具は、高い耐摩耗性を提供し、加工精度を保つために重要です。また、表面が滑らかな工具を選ぶことで、仕上がりの美しさが向上します。
- 工具形状:
- フライス加工においては、工具の形状が重要です。エンドミルやラフィングツールなど、用途に応じて工具を選定することが求められます。特に、細かい切削を行う際は、切り刃の数や角度を適切に設定することで、加工効率を高め、仕上がりを良好に保つことができます。
- 工具の刃先角度:
- POMの加工時には、鋭い刃先を持つ工具が推奨されます。これにより、切削時に材料がスムーズに切り離され、仕上がりが滑らかになります。鈍い刃先では、切削時に材料が引っかかりやすく、加工精度が低下するため、刃先角度を適切に選ぶことが大切です。
2-3. 加工後の仕上げ方法
POM材料は仕上がりの美しさが重要であるため、加工後の仕上げ方法も大切です。以下は、POM部品の仕上げに役立つ方法です。
加工後の部品は、組立て前に厳密にチェックすることが求められます。部品が規定のサイズや形状に合致しているか、精度を確認するために測定器を使用して測定を行い、最終的な品質を確保します。
研磨:
POMは研磨により、非常に滑らかな表面を得ることができます。細かい研磨ペーパーや研磨パッドを使用して、表面を均一に仕上げることで、高い光沢感と精度を実現できます。特に、精密部品や外観重視の部品に適しています。
バリ取り:
加工後に残るバリを取り除くことも重要です。バリが残っていると、部品の使用性や外観が損なわれることがあります。手作業や自動バリ取り機を使用して、バリを完全に取り除くことで、部品の仕上がり品質が向上します。
表面コーティング:
POMは摩耗や擦れに強い特性を持っていますが、さらに耐摩耗性を向上させるために、表面にコーティングを施すことがあります。コーティングを行うことで、POM部品の寿命を延ばし、性能を向上させることが可能です。
3. フライス加工におけるPOM材料の特性や注意点
POM材料は、フライス加工において優れた特性を持っていますが、その特性を最大限に活かすためには、適切な理解と注意が必要です。ここでは、POM材料の物理的特性、加工時の注意点、そして熱特性について詳しく解説します。
3-1. POM材料の物理的特性
POM(ポリアセタール)は、以下のような物理的特性を持っています。
- 高い機械的強度:
- POMは強度が高く、優れた耐摩耗性を持つため、摩擦が多い部品にも適しています。これにより、精密部品の製造にも適しており、長寿命が求められる用途に最適です。
- 優れた耐薬品性:
- POMは多くの化学薬品に耐性があり、酸やアルカリなどの液体にも強い耐性を示します。これにより、過酷な化学環境でも安定した性能を発揮します。
- 低摩擦係数:
- POMは摩擦係数が低く、滑らかな表面を持っています。この特性により、部品間の摩耗を抑え、静音性を高めることができます。
- 耐衝撃性:
- 物理的衝撃に対しても高い耐性を持っており、破損しにくい特性を持っています。これにより、動的負荷がかかる部品にも適しています。
3-2. 加工時の注意点とトラブルシューティング
POM材料をフライス加工する際には、いくつかの注意点があります。以下は、加工時の主な注意点とその対処法です。
- 溶けやすさ:
- POMは熱に敏感な材料であり、高温下で加工を行うと材料が溶けてしまうことがあります。これにより、仕上がりが悪くなったり、工具が詰まったりする原因になります。適切な切削速度を設定し、冷却液を使用することで熱の発生を抑えることが重要です。
- 加工後のバリ:
- POMは切削時にバリが発生しやすい材料です。バリが残ると、部品の精度や外観に影響を与えるため、加工後にバリ取りを十分に行うことが求められます。手作業やバリ取り機を使用して処理を行いましょう。
- 切削不良や表面仕上げの問題:
- POMは柔らかい材料であるため、過度な切削や不適切な工具を使用すると、表面に傷がついたり、仕上がりが粗くなることがあります。切削条件を適切に設定し、工具を定期的に確認することで、精度の高い仕上がりを実現できます。
- 工具の摩耗:
- POMは比較的柔らかいため、切削工具が摩耗しやすいことがあります。特に長時間の加工を行う場合は、工具の摩耗状態を確認し、適切なタイミングで工具を交換することが重要です。
3-3. POM材料の熱特性とその影響
POMの熱特性には、以下の点が挙げられます。
加工中に材料が過熱すると、熱変形が生じたり、表面が焼けたりすることがあります。これを防ぐためには、切削条件を調整し、冷却液を使用して温度管理を行うことが重要です。また、加工時の温度管理をしっかり行うことで、加工後の部品精度が向上します。
低い熱膨張率:
POMは熱膨張率が低いため、温度変化に対して安定した寸法を保ちます。これにより、精密な部品や温度変化に敏感な部品を製造するのに適しています。
熱安定性:
POMは、熱的に安定しており、最大加工温度は約100℃程度です。それ以上の温度に達すると、材料が軟化し、形状が変化する恐れがあります。加工中に過度な温度上昇を避けるために、冷却液を適切に使用することが重要です。
加工温度管理:
加工中に材料が過熱すると、熱変形が生じたり、表面が焼けたりすることがあります。これを防ぐためには、切削条件を調整し、冷却液を使用して温度管理を行うことが重要です。また、加工時の温度管理をしっかり行うことで、加工後の部品精度が向上します。
4. 切削加工におけるドリルの選び方やその影響
切削加工におけるドリルの選定は、加工精度や効率を大きく左右します。特にPOM部品の加工では、適切なドリル選びが部品の仕上がりや生産性に影響を与えます。ここでは、ドリルの種類や特性、POM部品に適したドリル選定基準、メンテナンスの重要性について解説します。
4-1. ドリルの種類と特性
ドリルにはさまざまな種類があり、用途に応じて選択する必要があります。主なドリルの種類とその特性は以下の通りです。
- 標準ドリル(ツイストドリル):
- 一般的なドリルで、主に金属やプラスチック、木材などの材料に使用されます。切削効率が高く、安定した切削性能を発揮します。
- コンクリートドリル:
- コンクリートや硬い材料を対象にしたドリルで、強度が高く、耐久性に優れています。POMのような軟質材料には使用されません。
- センタードリル:
- 中心に穴を開けるためのドリルで、主に精密な作業や下穴の作成に使用されます。これにより、次の加工が精密に行えます。
- コーティングドリル:
- ドリル先端にコーティングが施されており、摩耗を抑え、寿命を延ばす効果があります。硬い材料を扱う際に有用です。
- 特殊ドリル(スパイラルドリル、スリーブドリル):
- 特定の用途に合わせて設計されたドリルで、加工精度や効率を最大化するために使用されます。
4-2. POM部品に適したドリルの選定基準
POM部品を加工する際、ドリルの選定は加工精度や部品の品質に直接影響を与えます。POM部品に適したドリルを選ぶ際の基準は以下の通りです。
- ドリルの材質:
- POMの加工においては、炭素鋼や高速鋼(HSS)製のドリルが一般的に適しています。これらのドリルは切削速度が速く、POMのような柔らかい材料に対して効率的に加工が行えます。
- 切削角度:
- POMを加工する際は、切削角度を調整することが重要です。ドリルの切削角度が鋭すぎると、加工中に材料が溶けたり、仕上がりが悪くなる可能性があります。適切な切削角度(例えば、118度)を選ぶと良い結果が得られます。
- 穴あけの深さとドリル径:
- 深穴加工を行う際は、穴あけの深さに応じてドリル径を選びます。深い穴を開ける場合、長さが長いドリルを使用し、適切な切削速度と送り速度を選定することが重要です。
- コーティングの有無:
- POMは柔らかい材料ですが、長時間の加工や高負荷な加工を行う場合は、コーティングドリル(TiNなど)を使用することで、摩耗を防ぎ、ドリルの寿命を延ばすことができます。
4-3. ドリルのメンテナンスと寿命延長
ドリルのメンテナンスを行うことで、切削効率や加工精度を維持し、寿命を延ばすことが可能です。以下はドリルのメンテナンス方法と寿命延長のポイントです。
使用後にドリルを清掃し、切削屑や冷却液が残らないようにすることで、次回の使用時にトラブルを防ぐことができます。また、清掃によってドリルの寿命を延ばすことができます。
定期的な研磨:
ドリル先端が摩耗したり、切れ味が悪くなると加工精度が低下します。定期的に研磨を行うことで、切削力を回復させ、長期間使用することができます。特に、高精度が求められる場合、先端部分の研磨が重要です。
適切な冷却液の使用:
冷却液を使用することで、ドリルの温度を下げ、摩耗を防ぐことができます。POMの加工では過度な加熱を避けるために、冷却液を適切に使用することが重要です。
ドリルの点検と交換:
ドリルは定期的に点検し、必要に応じて交換することが必要です。特に高負荷の加工を行う際は、ドリルの摩耗を早期に発見し、交換することで加工の安定性を保つことができます。
5. 樹脂成型品の製作において、コストダウンのためのポイント
樹脂成型品の製作において、コストダウンは生産性を向上させ、競争力を強化するために非常に重要です。適切な成型プロセスの選定や、材料の最適化、生産効率の向上を図ることで、無駄なコストを削減できます。以下では、樹脂成型品のコストダウンを実現するための重要なポイントを解説します。
5-1. 成型プロセスの最適化
成型プロセスの最適化は、コストダウンを達成するための最初のステップです。以下の点に留意することで、製作コストを削減しつつ高品質な製品を得ることができます。
- 射出成型の最適化:
- 射出成型は最も一般的な樹脂成型方法ですが、加工条件(温度、圧力、冷却時間など)を最適化することで、エネルギーコストや材料の無駄を削減できます。特に冷却時間を短縮し、成型サイクルを短くすることで生産効率を向上させることができます。
- 金型の最適化:
- 成型品の設計段階で金型の設計を最適化することが、長期的なコストダウンにつながります。例えば、金型の複雑さを減らす、金型の寿命を延ばすための設計を行う、金型交換時の時間短縮を図るなどの工夫が必要です。
- 複合成型技術の導入:
- 複合成型技術を導入することで、材料の効率を上げると共に、新たな成型方法を採用することができます。例えば、二色成型やインサート成型を用いることで、組立工程を減らし、製造時間とコストの削減が可能になります。
- 成型サイクルの管理:
- 成型サイクルを短縮することが、製造コストの削減に直結します。射出速度や圧力を最適化し、冷却プロセスを効率化することで、製造時間を短縮し、コスト削減を実現します。
5-2. 材料の選定とコスト管理
材料選定は、樹脂成型品のコストダウンに大きな影響を与えます。材料の選定とコスト管理を適切に行うことで、製造コストを削減できます。
- 適切な樹脂の選定:
- 樹脂の選定においては、機能性とコストのバランスを考慮する必要があります。例えば、機能が求められる部品には高性能な樹脂を使用し、一般的な用途の場合はコスト効率が良い樹脂を選定します。これにより、性能に影響を与えることなく、材料費を削減することができます。
- 材料の調達ルートの最適化:
- 複数の仕入先と契約することで、価格競争を促進し、最適なコストで材料を調達することが可能です。また、安定した供給元を選ぶことで、納期の遅延や在庫管理の手間を減らすことができます。
- リサイクル材料の活用:
- リサイクル可能な樹脂材料を活用することで、材料コストを削減し、環境にも配慮することができます。リサイクル材料の品質が適切であれば、製品に影響を与えずにコスト削減が可能です。
- 材料の無駄削減:
- 成型の際に発生する端材や余剰材料を削減することも重要です。端材を再利用する、または最小化するために金型設計を見直すことにより、材料ロスを減らし、コストダウンを実現します。
5-3. 生産効率を上げるための工夫
生産効率を上げるための工夫を行うことで、製造コストを削減するだけでなく、納期の短縮や品質の向上にもつながります。
各工程の無駄を省き、効率的に作業を進めるために、改善活動(例えば、LEAN生産方式)を取り入れることが効果的です。工程間の手待ち時間や移動時間の短縮を図ることで、生産コストを削減できます。
自動化の導入:
生産ラインでの自動化を進めることで、作業員の手間を減らし、一定の品質を維持しながらコスト削減を実現できます。特に、成型後の後処理や組立工程においてロボットや自動機器を導入することで、生産効率が大きく向上します。
生産ラインのレイアウト改善:
生産ラインのレイアウトを見直し、部品の流れを効率化することで、作業時間を短縮し、物流コストや無駄な動きを削減することができます。
生産スケジュールの最適化:
生産スケジュールを適切に管理し、需要に合わせた柔軟な対応ができる体制を整えることで、無駄な生産ラインの稼働を減らし、コスト削減に繋がります。例えば、余分な生産や納期遅延を防ぐために生産計画を効率的に立てることが重要です。
まとめ
POM部品の製造コスト削減には、フライス加工での最適な工具選定、切削条件の見直し、加工順序の工夫が重要です。高効率な加工方法を取り入れることで、時間と材料の無駄を減らし、全体のコストを低減できます。