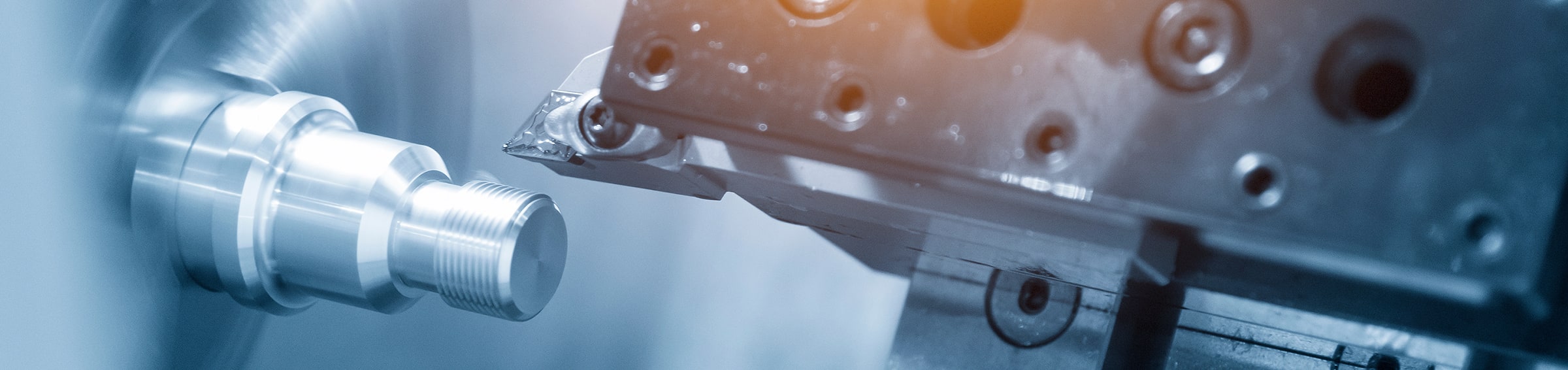
コラム column
ポリアセタール原材料完全ガイド:製品の品質を左右する素材とは
ポリアセタール(POM)は、様々な製品に使用される重要な素材です。製品の品質や性能を左右する重要な要素となるポリアセタール原材料について、本記事では詳しく解説します。製品開発や製造に携わる方々にとって、ポリアセタールの選択は極めて重要です。そこで、このガイドでは、ポリアセタール原材料の基本から、製品品質に与える影響、選び方のポイントなどを具体的に紹介していきます。製品の品質向上や製造効率向上に向けて、ポリアセタール原材料について正しく理解し、適切に活用するための手助けとなるでしょう。
ポリアセタール原材料とは
ポリアセタール樹脂の基本的な理解
ポリアセタール樹脂は、製品の品質に大きな影響を与える重要な素材です。この樹脂は、耐摩耗性や剛性に優れており、機械部品や歯車などの高性能部品に広く使用されています。例えば、自動車業界では、エンジン部品や内装パーツなどにポリアセタール樹脂が利用されています。
ポリアセタール樹脂は、耐摩耗性に優れているため、歯車などの摩耗が激しい部品に適しています。また、化学的な安定性も高く、耐油性や耐薬品性に優れているため、幅広い産業分野で使用されています。
さらに、ポリアセタール樹脂は耐熱性や寸法安定性にも優れており、高い機械的強度を持つことから、精密機器や電子部品などにも広く利用されています。これらの特性から、ポリアセタール樹脂は製品の性能向上や耐久性向上に貢献する重要な素材と言えます。
ポリアセタールの化学的性質
ポリアセタールは、プラスチックの一種であり、非常に優れた物理的性質を持っています。この素材は、高い剛性と耐久性を誇り、化学薬品や摩耗にも強い特性を持っています。この特性から、機械部品や電気部品、歯車など、耐久性が求められる製品に広く使用されています。
ポリアセタールは、熱可塑性樹脂としても知られており、加熱することで形状を変えることができます。そのため、成形加工が比較的容易であり、様々な形状の製品を生産する際に重宝されています。さらに、外部からの影響を受けにくい性質を持つため、耐候性にも優れています。
例えば、自動車のインジェクションポンプや時計の歯車、ファスナーやバルブなど、私たちの身の回りにあるさまざまな製品にポリアセタールが使われています。その優れた性質から、製品の品質向上に欠かせない素材として重要視されています。
原材料の種類とその特徴
ポリアセタール(POM)は、耐熱性や耐摩耗性に優れた樹脂で、さまざまな製品に使用されます。POMの原料は、主にフォーマルデヒドとエチレンオキシドから作られており、その特徴は優れた機械的特性と化学的安定性です。例えば、自動車部品や家電製品などの耐久性が求められる製品に広く利用されています。
また、POMの原料の一つであるフォーマルデヒドは有毒な物質であり、製品の品質に大きな影響を与える重要な要素です。原料の純度や製造プロセスが品質に直結し、品質管理が怠ると製品の性能や信頼性に影響を及ぼす可能性があります。
したがって、製品の品質向上を目指す際には、POMの原料についても注意深く管理することが肝要です。原料の種類や特性を理解し、製品のパフォーマンスを左右する重要性を認識することが、製造業における競争力強化につながるでしょう。
ポリアセタール樹脂の特性
物理的特性とその影響
ポリアセタール原材料は製品の品質に影響を与える重要な素材です。この素材の物理的特性が製品の性能や耐久性に大きく関わります。例えば、ポリアセタールは優れた機械的強度と硬度を持ち、熱にも強い性質があります。そのため、歯車やベアリングなどの精密機器や自動車部品などに幅広く使用されています。
さらに、ポリアセタールは化学的に安定しており、摩擦や腐食にも強い特性があります。このため、耐摩耗性や耐薬品性が求められる場面で広く利用されています。例えば、医療機器や家電製品、工業製品など多様な分野でポリアセタールが重要な役割を果たしています。
このように、ポリアセタール原材料の物理的特性は製品の品質や信頼性に大きな影響を与えています。その優れた特性から、様々な産業分野で幅広く活用されている素材と言えるでしょう。
熱的特性と耐久性
ポリアセタール原材料は、製品の品質に大きな影響を与えます。その熱的特性と耐久性が重要な要素となります。例えば、ポリアセタールは高い剛性と強度を持ち、耐摩耗性にも優れています。これにより、歯車やベアリングなどの部品として幅広く使用されています。
さらに、ポリアセタールの熱的特性は優れており、高温においても形状安定性を保ちます。これにより、自動車部品や電子機器など高温環境で使用される製品に最適です。
その耐久性も優れており、化学薬品や油脂に対しても強い耐性を持っています。この点からも、ポリアセタールは幅広い産業分野で重要な素材として利用されています。
化学的耐性と加工性
ポリアセタールは、化学的に耐性があり、加工性に優れた素材です。これらの特性は製品の品質に大きく影響します。例えば、ポリアセタールは自動車部品や電子機器などの幅広い製品に使用されています。その理由は、耐摩耗性や耐熱性に優れているためです。さらに、ポリアセタールは潤滑剤の使用を必要とせず、摩擦抵抗が少ないため、機械部品などの用途に適しています。結論として、ポリアセタールは優れた化学的性質と加工性を兼ね備えた素材であり、製品の品質向上に貢献しています。
ポリアセタールの用途
一般的な使用例
ポリアセタール原材料は製品の品質に大きな影響を与えます。これは、様々な産業で広く使用されており、その特性によって優れた性能を発揮します。例えば、車の内装やエンジン部品、家電製品など多くの製品にポリアセタールが使われています。ポリアセタールは非常に耐久性があり、摩耗や化学物質にも強いため、製品の寿命を延ばすことができます。
さらに、ポリアセタールは高い剛性と耐熱性を持ち、機械部品や工業製品にも適しています。そのため、製品の信頼性や性能を向上させることができます。環境への影響も少なく、リサイクルも比較的容易なため、持続可能な製品作りにも貢献します。
ポリアセタール原材料の利点を活かし、製品の品質向上や持続可能性を考える際には、その優れた特性を生かした製品開発が重要です。
特殊な産業での活用
[heading]=ポリアセタール原材料完全ガイド:製品の品質を左右する素材とは
[text]=ポリアセタール(POM)は、機械部品や自動車部品などさまざまな分野で広く使用されています。この素材は、耐熱性や耐摩耗性に優れており、非常に強度があります。POMは、歯車やベアリングなどの精密部品から、家電製品の部品まで幅広い用途に使われています。
POMの品質は、原材料の選定によって大きく左右されます。品質の悪い原料を使用すると、製品の強度や耐久性が低下し、安全性にも問題が生じる可能性があります。したがって、製造業者は高品質なPOM原料を選定することが重要です。
具体的な例として、自動車メーカーはエンジン部品や内装部品にPOMを使用しており、品質の高いPOMを使用することで製品性能を向上させています。そのため、POMの原材料選定は製品の品質向上に直結する重要な要素と言えます。
ポリアセタール製品の市場動向
ポリアセタール製品は、様々な製品に使われる素材です。この素材は、耐熱性や耐摩耗性に優れ、高い剛性と強度を持っています。これらの特性が製品の品質を左右します。例えば、機械部品や電子機器のギア、プラスチック製のボタンやジッパーなどに広く使用されています。
ポリアセタールの市場動向を考えると、需要が年々増加しており、自動車産業や家電製品業界などで広く利用されています。特に自動車部品としての需要が高まっており、その耐久性や耐候性から選択されることが多いです。
今後もポリアセタール製品はさらなる成長が期待されており、製品の品質向上や新たな用途開拓が進められています。これからもこの素材が様々な製品に利用され、需要が増加していくことが予想されます。
ポリアセタール製品の品質と問題点
品質に影響を与える要因
ポリアセタールは、製品の品質に大きな影響を与える重要な素材です。この素材の品質は、原材料の選定や加工方法によって左右されます。例えば、原材料の純度や特性が製品の強度や耐久性に直接影響を与えます。また、製造プロセスの品質管理も重要であり、正確な温度や圧力の管理が製品の均一性や完成度に影響します。さらに、環境要因や添加物の適切な配合も製品の品質に大きく関わります。これらの要因を適切に管理し、高品質なポリアセタールを製造することが、製品の性能や信頼性を確保する上で不可欠です。そのため、製造業者や製品設計者は、原材料選定から製造プロセスまでを慎重に管理することが重要です。
一般的な品質問題と解決策
ポリアセタール原材料完全ガイド:製品の品質を左右する素材とは
一般的な品質問題を解決するためには、ポリアセタール(POM)の原材料選定が重要です。POMは自動車部品、家電製品、医療機器など幅広い製品に使われる素材であり、その品質は製品の性能や信頼性に直結します。
POMの品質を左右する要素として、原料の純度、粘度、耐熱性などが挙げられます。例えば、高い純度の原料を使用することで、製品の強度や耐久性が向上します。また、適切な粘度を選定することで、成形プロセスの安定性や製品の寸法精度が確保されます。
したがって、製品の品質を確保するためには、適切なPOM原材料の選定が欠かせません。適切な原料を選ぶことで、製品の性能向上や市場競争力の強化につながることが期待されます。
製品寿命と環境への影響
ポリアセタールは耐摩耗性や強度に優れ、自動車部品や電子機器など幅広い製品に使われる重要な素材です。しかし、その製品寿命や環境への影響を考えるときには、ポリアセタールの原材料が重要な役割を果たします。例えば、再生プラスチックを使用することで、製品の持続可能性が高まります。日本では環境に配慮した製品への需要が高まっており、ポリアセタールの原材料選定にも注目が集まっています。企業が環境負荷を低減し、製品の品質向上に取り組むことで、消費者からの評価も高まるでしょう。このように、ポリアセタールの原材料は製品の品質だけでなく、環境への貢献にも大きな影響を与える重要な要素と言えます。
ポリアセタール原材料の選定
選定のポイントと基準
ポリアセタールは製品の品質に影響を与える重要な素材です。原材料の選定においては、いくつかのポイントと基準があります。まず、原材料の純度が重要です。高品質なポリアセタールを製品に使用することで、製品の物性や耐久性が向上します。また、安定した供給源を確保することも重要です。信頼性の高いサプライヤーから原材料を調達することで、製品の一貫性を保つことができます。さらに、環境への配慮や法規制の遵守も欠かせません。良質な素材を使用することで、製品の競争力を高めることができます。これらのポイントを踏まえて、ポリアセタール原材料の選定を慎重に行うことが重要です。
原材料の品質と製品性能の関係
ポリアセタールは、プラスチックの一種であり、さまざまな製品に使われています。ポリアセタールの品質は、製品の性能に直接影響を与えます。例えば、ポリアセタールの原料であるアセトアルデヒドが純度不足だと、製品の強度や耐久性が低下する可能性があります。
製品の成形時にも、原料の品質は重要です。粒子の大きさや均一性が問題となると、製品の表面に凹凸や欠陥が生じることがあります。その結果、製品の品質が低下し、使用用途が制限される可能性があります。
したがって、ポリアセタール製品を製造する際には、原料の品質に注意することが重要です。良質な原料を選ぶことで、製品の性能を最大限に引き出し、ユーザーに満足をもたらすことができます。
供給元との連携方法
ポリアセタール原材料は製品の品質に大きな影響を与えます。原料の供給元との連携方法は非常に重要です。なぜなら、品質の良し悪しは素材によって左右されるからです。例えば、高品質なポリアセタール原材料を使用すると製品の耐久性や耐熱性が向上し、顧客満足度も高まります。逆に、低品質な原料を使用すると製品の強度や耐久性が低下し、市場競争力が損なわれる可能性があります。したがって、製品の品質を保つためには、信頼できる供給元との継続的な連携が不可欠です。ポリアセタール原材料を選ぶ際には、供給元の信頼性や品質管理体制を慎重に考慮することが重要です。
ポリアセタール原材料の調達
原材料の市場と価格動向
ポリアセタール原材料は製品の品質に大きな影響を与える重要な素材です。この素材は、様々な工業製品や部品に広く使用されており、その需要は着実に高まっています。ポリアセタールは、耐熱性や耐摩耗性に優れており、機械部品や自動車部品などの製造に欠かせない素材となっています。
原材料の市場と価格動向は、製品の生産コストや供給安定性に直接影響を与えます。需要の増加や供給不足などの要因によって、原材料の価格は変動する傾向にあります。このため、製造業や製品開発に携わる企業は、市場動向を注視し、原材料の調達計画やコスト管理を適切に行う必要があります。
ポリアセタール原材料の市場における動向を把握し、品質向上とコスト効率化に努めることが、製品競争力を維持するために重要です。良質な原材料の選定と適切な価格管理は、製品の信頼性と競争力を高める一助となります。
安定供給のための戦略
ポリアセタール(POM)は、製品の品質に大きな影響を与える重要な素材です。POMは機械的な強度や耐熱性に優れ、自己潤滑性を持つため、自動車部品や家電製品など幅広い製品に利用されています。原材料の選定が品質に直結するため、メーカーは原料の品質や供給安定性に注力しています。
原材料の調達先や品質管理が十分でない場合、製品の仕上がりや性能に影響が出る可能性があります。特に自動車部品など、安全性が求められる製品では、適切なPOMの選定が不可欠です。
したがって、メーカーは信頼できる原材料サプライヤーとのパートナーシップを築き、品質管理に努めることが重要です。安定供給と品質確保を両立させることで、製品の信頼性向上につながります。
持続可能な原材料調達の重要性
ポリアセタール(POM)製品の品質を左右するポリアセタール原材料の調達が注目されています。ポリアセタールは、耐熱性や耐摩耗性に優れた樹脂であり、自動車部品や家電製品など幅広い製品に使用されています。原材料の品質が不良だと製品の強度や耐久性が低下し、安全性にも問題が生じる可能性があります。
より持続可能な製品を提供するためには、信頼性のある供給元からの原材料調達が重要です。たとえば、環境への配慮や社会的責任を果たすサプライヤーからの原材料を選択することで、製品の価値が向上し、顧客からの信頼も高まります。
ポリアセタール製品の製造において、原材料の選定は製品の品質に直結する重要な要素となります。持続可能な原材料調達を通じて、製品の品質向上と社会的責任の実践を両立させることが求められています。
ポリアセタール製品の製造プロセス
製造工程の概要
ポリアセタール製品の品質には、原材料が重要な役割を果たします。ポリアセタールは、機械部品や電気部品など幅広い製品に使用され、その耐熱性や耐摩耗性が求められます。原材料は、ポリオキシメチレンとして知られる重要な樹脂を含みます。この樹脂は、高い剛性や耐熱性を持ち、様々な工業製品に適しています。
特に、自動車部品や家電製品などの製造において、ポリアセタールの品質は製品の信頼性や長寿命に直結します。例えば、自動車の歯車や電子機器の部品など、高い耐久性や精度が求められる製品においては、原材料の質が重要です。
したがって、ポリアセタール製品の製造工程においては、原材料の品質管理が欠かせません。適切な原料の選定や加工技術の向上などが重要であり、製品の品質向上と市場競争力の確保につながります。ポリアセタール製品の素材には、製品の性能と信頼性を左右する重要な要素が詰まっています。
原材料から製品までの変換
ポリアセタール(POM)は、耐熱性や耐薬品性に優れた樹脂であり、自動車部品や電子機器などの製品に広く使用されています。ポリアセタールの品質は、原材料の選定から製品の製造に至るまでの各段階で左右されます。
まず、ポリアセタールの原材料は、高品質なポリオキシメチレン樹脂が選ばれます。この原材料の純度や特性が、最終製品の物性や耐久性に大きく影響します。次に、製造プロセスが品質に与える影響も大きいです。適切な温度管理や成形方法が重要であり、これらが適切に行われることで製品の品質が向上します。
したがって、ポリアセタール製品の品質は、原材料から製品までの変換プロセス全体で慎重に管理されることが重要です。そのような注意深い管理が製品の信頼性と性能を確保し、最終的には消費者に安心して利用してもらえる製品を提供することにつながります。
製造時の品質管理
ポリアセタール原料の品質管理は製品の品質に直結する重要な要素です。ポリアセタールは自動車部品や家電製品など幅広い製品に使用される素材であり、その品質は製品の性能や耐久性に大きな影響を与えます。製造時の品質管理は材料の純度や均一性を確保し、最終製品の品質を一貫して高レベルに保つために欠かせません。
例えば、製造時に使用される原料の品質が低いと、製品の強度や耐久性が不足し、製品が早期に劣化する可能性があります。これにより製品の信頼性が低下し、顧客からの評価や信頼を失うことにつながります。したがって、ポリアセタール製品の品質を維持するためには、製造時の品質管理が欠かせない要素となります。
最新の研究と開発動向
ポリアセタール樹脂のイノベーション
ポリアセタール樹脂は、製品の品質に大きな影響を与える重要な素材です。この革新的な材料は、様々な産業分野で幅広い用途に使われています。例えば、自動車部品や家電製品、工業製品などに利用されており、その耐久性や耐熱性能が高く評価されています。
ポリアセタール樹脂は、優れた機械的特性を持ちながらも、耐化学性や電気絶縁性も兼ね備えています。このため、要求される特性に合わせて調整が可能であり、製品の信頼性や耐久性を向上させることができます。
さらに、ポリアセタール樹脂は、高い加工性を持つため、複雑な形状や精密な部品の製造にも適しています。このような特性から、製品の設計自由度が高く、製造プロセスの効率化にも貢献しています。ポリアセタール樹脂は、今後もさらなる技術革新や産業への貢献が期待される素材と言えるでしょう。
環境に優しい原材料の開発
ポリアセタールは、製品の品質に大きな影響を与える重要な素材です。環境に優しい製品を作るためには、ポリアセタール原材料の開発が欠かせません。例えば、再生可能な植物由来の原料を使用することで、製品の持続可能性が向上します。日本では、環境保護への取り組みがますます重要となっており、企業も環境負荷の低減を目指しています。
ポリアセタール原材料の選択は製品の性能や品質に直結します。例えば、耐熱性や耐摩耗性を向上させるためには、適切な原料を選定することが重要です。品質の向上は顧客満足度にもつながり、競争力の向上に繋がります。
環境に配慮したポリアセタール原材料の開発は、今後ますます重要性を増していくことが予想されます。企業が持続可能な製品開発に取り組むことで、社会への貢献や市場での競争力強化が期待されます。
産業界における新しい応用
ポリアセタールは、製品の品質に大きな影響を与える重要な素材です。この原材料は、耐熱性や耐摩耗性に優れ、機械部品や自動車部品、電子機器など幅広い産業で使用されています。例えば、自動車の歯車や電子機器のギアなど、耐久性が求められる部品にポリアセタールが活躍します。
ポリアセタールは、化学的に安定しており、摩擦や薬品にも強い特性を持っています。そのため、品質や耐久性が必要な製品には欠かせない素材として注目されています。産業界において、ポリアセタールが新しい応用を見出し、製品の性能向上に貢献しているのです。
ポリアセタール原材料の安全性と規制
安全性に関する基準とガイドライン
ポリアセタール原材料は製品の品質に大きく影響を与えます。ポリアセタールは、高い強度や耐熱性を持つプラスチック素材であり、様々な製品に広く使用されています。品質を保つためには、原材料の選定が重要です。
ポリアセタールの特性を生かすためには、原材料の純度や添加物の有無など安全性に関する基準とガイドラインを遵守する必要があります。例えば、製品の強度や耐久性を保つためには、原材料の純度が高く、不純物が少ないことが重要です。
製品の品質を左右するポリアセタール原材料の選定は製品の信頼性や性能に直結します。安全性に関する基準とガイドラインを守りながら、適切な原材料を選定することが製品の品質向上につながります。
国内外の規制の現状
ポリアセタールは、製品の品質に影響する重要な素材です。この原材料が品質に与える影響を理解することは、製品開発や製造において重要です。ポリアセタールは機械的性質に優れ、耐熱性や耐摩耗性にも優れています。そのため、歯車やボタンなどの部品製造に広く使用されています。
しかし、原材料の品質にばらつきがあると、製品の性能や耐久性に影響が出てしまいます。特に、熱安定性や機械的強度は品質に大きく左右されます。製品の安全性や信頼性を確保するためにも、原材料の品質管理は欠かせません。
例えば、自動車部品のような高い要求水準を持つ製品では、品質のばらつきが製品の信頼性や安全性に直結します。そのため、厳格な品質管理が求められ、原材料の選定にも細心の注意が必要です。品質の良し悪しは製品の価値を左右する重要な要素なのです。
法規制への対応と企業の責任
ポリアセタールは、製品の品質に影響を与える重要な素材です。この原材料は、製品の耐久性や強度を左右し、製品全体の性能に大きな影響を与えます。例えば、自動車部品や家庭用品など、さまざまな製品に使用されています。ポリアセタールは、耐摩耗性や化学薬品に対する抵抗力に優れており、長期間使われる製品に適しています。そのため、製造業界で広く利用されています。
製品の品質を向上させるためには、適切なポリアセタール原材料を選択し、製品設計や製造過程において適切に使用することが重要です。このように、ポリアセタール原材料の選定と取り扱いを正しく行うことで、製品の性能や耐久性を確保することができます。
ポリアセタール原材料の将来性
市場予測と産業の成長
ポリアセタールは、製品の品質に影響を与える重要な素材です。この原材料は、耐熱性や耐摩耗性に優れており、機械部品や電子部品など幅広い製品に使用されています。例えば、歯車やホイール、ジッパーやスナップボタンなどにポリアセタールが使われています。
ポリアセタールは、強度や剛性が高く、化学的にも安定しているため、長期間使用しても劣化しにくい特徴があります。そのため、自動車部品や家電製品など耐久性が求められる製品に広く利用されています。
このように、ポリアセタールは製品の性能向上や耐久性強化に貢献する重要な素材であり、製造業において欠かせない存在と言えます。
技術革新による機会
ポリアセタール原材料は製品の品質に大きく影響する重要な素材です。この原材料は様々な製品に使用され、その優れた特性から幅広い産業分野で重要な役割を果たしています。例えば、自動車部品や電子機器、家庭用品などに使用されており、その耐久性や耐熱性などの性質が製品の信頼性や長寿命につながっています。
ポリアセタールは、化学的に安定しており、摩耗や腐食にも強いため、製品の耐久性を向上させます。さらに、高い機械的強度や耐摩耗性も持っており、製品の品質向上に貢献しています。
したがって、ポリアセタール原材料は製品の性能や品質を向上させる上で欠かせない素材であり、産業界において重要な役割を果たしています。その優れた特性を活かしながら、さまざまな製品の品質向上に貢献していくことが期待されています。
持続可能性と環境への取り組み
ポリアセタール原材料は製品の品質に直接影響を与える重要な素材です。この素材は、様々な産業で広く使用されており、その特性や品質は製品の性能や耐久性に大きく関わってきます。例えば、自動車や家電製品などの製造において、ポリアセタールは高い機械的強度や耐熱性を持つため、優れた製品を生み出すために欠かせない材料となっています。
ポリアセタール原材料の選定は製品の品質向上につながる重要な要素であり、適切な素材を選ぶことが製品の信頼性や耐久性を高めることにつながります。素材の品質や純度、加工技術などが製品の最終的な品質に大きな影響を与えるため、製品開発や製造においてポリアセタール原材料の選定は慎重に行われるべきです。
まとめ
ポリアセタールの製品の品質を左右する素材とは
ポリアセタールは、機械部品や電気部品など多くの製品に使用される工業用プラスチックです。その原材料は、高品質でなければなりません。原材料の品質が製品の品質に直結するため、製造業者は原材料の選定に注意を払う必要があります。原材料の品質が高ければ、製品の耐久性や信頼性が向上し、顧客の信頼を得ることができます。これにより、市場競争において優位に立つことができます。
ホモポリマーの基点!理解しておきたい原材料とその特性
ホモポリマーの基点となる原材料とその特性について理解しておきたいと考えたことはありますか?ホモポリマーは、現代の産業において欠かせない重要な素材ですが、その製造や特性について深く理解することは重要です。本記事では、ホモポリマーの基礎知識から、使用される原材料の種類やその特性について詳しく解説していきます。ホモポリマーに興味がある方やこの分野に関わる方々にとって、参考になる情報を提供します。原材料や特性について理解を深めることで、ホモポリマーに関する知識がより豊かになることでしょう。
ホモポリマーとは
ホモポリマー基本概念の紹介
ホモポリマーは、同じ種類の単位でできているポリマーの一種です。このホモポリマーを作るために必要なのが「原材料」です。例えば、エチレンなどの単量体を使ってポリエチレンを作ると、それはホモポリマーとなります。原材料の種類によって、ポリマーの性質や特性が決まります。例えば、ポリエチレンは柔らかくて耐久性があり、プラスチック製品に広く使われています。一方、ポリプロピレンは強度があるため、様々な用途に適しています。つまり、原材料が異なれば、作られるホモポリマーの特性も異なるということです。これらの原材料と特性を理解することは、ホモポリマーに関する基本概念を押さえるうえで重要です。
ホモポリマーの原材料とその種類
ホモポリマーは、プラスチック製品や合成繊維など多くの製品に使われる重要な材料です。ホモポリマーの原材料には、主に石油やナフサが使われます。これらは石油化学製品から抽出され、化学反応を経てホモポリマーが生成されます。
ホモポリマーには、たくさんの種類があります。例えば、ポリエチレンやポリプロピレンなどがあります。ポリエチレンは柔らかく、伸縮性に優れているため、ビニール袋や容器などに広く使われています。一方、ポリプロピレンは耐熱性に優れており、電子機器や自動車部品などに利用されています。
ホモポリマーの種類によって特性が異なるため、製品の用途に合った適切なホモポリマーを選ぶことが重要です。原材料としての石油やナフサから始まり、化学反応を経て様々なホモポリマーが生み出される仕組みが、製品の多様性を支えています。
ホモポリマーとコポリマーの違い
ホモポリマーとコポリマーの違いについてご説明します。ホモポリマーは、同じ単一のモノマーからできているポリマーのことです。例えば、ポリエチレンやポリプロピレンなどがあります。一方、コポリマーは、複数の異なる種類のモノマーからできています。例えば、スチレンとブタジエンからなるスチレン・ブタジエンコポリマーがあります。
ホモポリマーは、単一のモノマーからできているため、物性や加工性が比較的均一であり、一定の特性を持ちます。一方、コポリマーは異なるモノマーの影響を受けるため、複数の特性を合わせ持つことができます。例えば、スチレンとブタジエンのコポリマーは、スチレンの硬さとブタジエンの柔軟性を兼ね備えています。
このように、ホモポリマーとコポリマーは原材料の違いから独自の特性を持ち、それぞれ異なる用途に活用されています。
ホモポリマーの特性と用途
物理的特性の理解
ホモポリマーは、私たちの日常生活に欠かせない重要な素材です。ホモポリマーの物理的特性を理解することは、その用途や特性を理解し、適切に利用するために重要です。ホモポリマーは、単一のモノマーから構成される高分子化合物であり、同じ種類の単位構造が連続して重なっています。
例えば、ポリエチレンはエチレン単位が繰り返されることで作られます。このような構造によって、ホモポリマーは特定の特性を持つことができます。ポリエチレンは柔軟性があり、耐久性が高いため、様々な用途に利用されています。
ホモポリマーの物理的特性を理解することで、それぞれの素材の適正な使用方法や利点を理解し、効果的に活用することができます。
化学的耐性
ホモポリマーは、さまざまな素材に使われる重要な材料です。これらの特性を理解することは、製品の性能や耐久性を向上させるために重要です。ホモポリマーは、化学的に優れた耐性を持っています。例えば、酸やアルカリ、溶剤などの化学物質に対して安定した性質を示すことがあります。このため、ホモポリマーは、さまざまな産業分野で幅広く使用されています。例えば、自動車部品、電子機器、医療機器などの製造において重要な役割を果たしています。そのため、ホモポリマーの化学的耐性を理解し、適切に活用することは、製品の品質向上や安定した性能維持につながります。
ホモポリマーの日常生活での応用例
ホモポリマーは、私たちの日常生活に広く使われている重要な素材です。例えば、プラスチック製品や合成繊維などに利用されています。ホモポリマーは、ポリエチレンやポリプロピレンなどの材料で作られ、軽量で耐久性に優れています。これらの特性から、食品容器、衣類、家具、車両部品など幅広い製品に利用されています。
さらに、ホモポリマーは熱可塑性樹脂としても知られており、加熱によって形状を変えることができるため、製造プロセスでの柔軟性が高いという利点もあります。これにより、様々な形状や用途に合わせた製品を効率的に生産することが可能となっています。
ホモポリマーは、私たちの生活を快適にするさまざまな製品の製造に欠かせない素材であり、その特性を理解することは重要です。
プラスチック製品の安全性
ホモポリマー製品の安全基準
ホモポリマー製品の安全基準は、製品の使用目的や材料の特性によって異なります。ホモポリマーは、複数の単量体から合成される高分子化合物であり、様々な製品に利用されています。例えば、ポリエチレンやポリプロピレンなどが一般的なホモポリマーです。
製品の安全性を確保するためには、原材料の選定が重要です。特定の用途に適した材料を選ぶことで、製品の耐久性や安全性を確保することが可能です。また、製造過程での品質管理も欠かせません。例えば、製品中の不純物や異物が許容基準を超えないように管理することが重要です。
したがって、ホモポリマー製品の安全基準を確保するためには、適切な原材料の選定と品質管理が欠かせません。これにより、安全性や品質が確保された製品を提供することが可能となります。
食品用プラスチックの安全性
ホモポリマーは、私たちの日常生活に欠かせない素材です。これらの素材を作るための原材料やその特性について、理解しておくことは重要です。ホモポリマーは、1つの単位からできているため、様々な特性を持っています。例えば、ポリエチレンはしなやかである一方、ポリプロピレンは硬い特性を持っています。
原材料として使われるモノマーには、エチレンやプロピレンなどがあります。これらは石油由来の化合物であり、石油の精製過程で得られます。これらの原料は、様々な加工技術を経て、私たちの身の回りのさまざまな製品に使われています。
ホモポリマーは、軽量で丈夫であり、食品包装や家電製品などに広く使用されています。これらの素材は私たちの生活を支える大切な役割を果たしています。
使用上の注意点と対策
[ホモポリマーの基点!理解しておきたい原材料とその特性]
ホモポリマーは、私たちの日常生活において広く使用されている重要な素材です。では、ホモポリマーがどのように作られ、どのような特性を持っているのでしょうか?
まず、ホモポリマーの主な原材料は石油由来の単量体です。これらの単量体が重合反応によってつながり、長い重合体となります。この結果、さまざまな種類のホモポリマーが生まれます。例えば、ポリエチレンは食品包装やビニール袋などに広く使われています。
ホモポリマーは軽量で丈夫な特性を持ち、耐久性に優れているため、さまざまな産業で幅広く活用されています。石油由来の原料を使用しているため、環境への影響にも注意が必要ですが、リサイクル技術の進歩により、再利用が可能となっています。これらの特性を理解することで、ホモポリマーの重要性が見えてきます。
プラスチック製品のリサイクル
プラスチックリサイクルの基本プロセス
ホモポリマーの基点!理解しておきたい原材料とその特性
ホモポリマーは、プラスチック製品の原材料として重要な役割を果たしています。原材料は、石油や天然ガスなどの化石燃料から作られ、熱や圧力などの過程を経てポリマーとなります。これらの原材料は、繊維、フィルム、容器などさまざまな製品に利用されています。
ただし、ホモポリマーは環境にも影響を及ぼすことがあります。例えば、リサイクルが困難であることや廃棄物としての処理が課題となっています。そのため、原材料の選択や製造プロセスの見直しが求められています。
したがって、ホモポリマーの特性や環境への影響を理解し、持続可能な製品開発に取り組むことが重要です。原材料の効率的な利用やリサイクル技術の向上などが今後の課題となるでしょう。
ホモポリマー製品のリサイクル性
ホモポリマー製品のリサイクル性は、環境への配慮や資源の有効活用において重要です。ホモポリマーは、同じ種類の単量体からできており、これによってリサイクルが比較的容易に行えます。例えば、ポリエチレンやポリプロピレンはホモポリマーの一種であり、使用済み製品を再生して新しい製品を作ることが可能です。そのため、廃棄物の削減や環境への負荷軽減に貢献します。また、リサイクルされたホモポリマーは品質を保持しつつ、コスト削減にもつながります。このように、ホモポリマー製品のリサイクル性は、持続可能性を考える上で欠かせない要素となっています。
家庭でできるプラスチックの分別とリサイクル
ホモポリマーの基点!理解しておきたい原材料とその特性
ホモポリマーは、プラスチック製品の基本となる重要な素材です。この素材を理解するためには、その原材料や特性を知ることが重要です。
理由として、ホモポリマーの原材料は石油や天然ガスなどの化石燃料から作られています。これらの原料を適切に加工することで、様々なプラスチック製品が生産されます。例えば、PETボトルやポリエチレン製品などが挙げられます。
具体例として、PETボトルは一般的なホモポリマーであり、飲料容器や衣類などに幅広く利用されています。また、ポリプロピレンは高い耐熱性や剛性を持ち、家庭用品や自動車部品などに使用されています。
結論として、ホモポリマーは私たちの日常生活に欠かせない素材であり、その原材料や特性を理解することで、プラスチック製品の重要性や使い方をより深く理解することができます。
プラスチックと環境
プラスチックの環境への影響
ホモポリマーは、私たちの日常生活に多く使われており、その原材料と特性を理解することは重要です。ホモポリマーの主な原材料は石油から作られており、石油は非再生可能な資源であるため、環境に与える影響が懸念されています。例えば、プラスチック製品の多くが海洋に流出し、生態系や海洋生物に害を及ぼしています。
原材料の再利用やリサイクルが進められていますが、今後は環境に配慮した代替原料の開発が求められています。バイオマス由来の原料や再生可能な資源を使用することで、ホモポリマーの製造における環境への負荷を軽減できます。
環境への配慮がますます重要となる中、ホモポリマーの原材料に関する知識は今後ますます注目されるでしょう。生産段階から環境に配慮した取り組みを進め、持続可能な社会を築くための一環として、私たちも積極的に取り組んでいきましょう。
ホモポリマー製品のエコフレンドリーな取り組み
ホモポリマー製品のエコフレンドリーな取り組み
ホモポリマー製品は、私たちの日常生活に広く使われている重要な素材です。しかし、その製造には環境への負荷が問題とされています。原材料の選定が重要であり、再生可能素材の利用やリサイクル可能なポリマーの開発が進められています。
例えば、植物由来のバイオマスを原料とするホモポリマーは、化石燃料に比べて二酸化炭素排出量が低いため、環境への負荷を軽減できます。また、リサイクルがしやすいポリマーを使用することで、廃棄物の削減や環境への配慮が可能となります。
これらの取り組みによって、ホモポリマー製品のエコフレンドリーな特性がより注目されることで、持続可能な未来を目指す一翼を担っています。
環境保護への意識とプラスチック使用のバランス
ホモポリマーは、日常生活で広く使われているプラスチック製品の基本となる素材です。原材料としては、石油や天然ガスから作られることが一般的です。これらの化石燃料から作られるホモポリマーは、軽量で丈夫、耐熱性に優れるなどの特性を持っています。
例えば、ペットボトルや食品包装、衣類などのプラスチック製品は、ホモポリマーから作られています。また、自動車の内装部品や建築材料にも広く使用されています。
ホモポリマーはリサイクルも可能であり、環境への負荷を軽減することができます。しかし、適切なリサイクルを行わないと廃棄物となり、環境に悪影響を与える可能性もあるため、使用後の処理にも配慮が必要です。
環境への配慮とプラスチック製品の利便性を両立させるためには、ホモポリマーの適切な使用とリサイクルが重要です。
プラスチック製品の未来
持続可能なプラスチックの開発動向
ホモポリマーの基点!理解しておきたい原材料とその特性
ホモポリマーは、化学的に単一の重合体から構成されるポリマーです。原材料として使われるモノマーが大きな影響を与えます。例えば、エチレンはポリエチレンの主要な原料であり、プロピレンはポリプロピレンの主成分です。
ホモポリマーは、特性を変えることなく均一な構造を持ち、結晶性や非結晶性の特性を制御できます。これにより、加工性や強度などの特性が調整しやすく、幅広い用途に利用されています。例えば、ポリエチレンは包装材料やパイプ、ポリプロピレンは自動車部品や繊維などに広く使われています。
原材料の選択とポリマーの特性を理解することで、製品開発や工業製品の改善に役立ちます。ホモポリマーの理解は、さまざまな産業分野での革新と持続可能なプラスチックの開発につながる重要な要素となります。
ホモポリマーの技術革新と市場への影響
ホモポリマーは様々な製品や材料の製造に利用される重要な素材です。ホモポリマーの特性を理解するためには、その原材料を知ることが不可欠です。一般的に、ホモポリマーは単一のモノマーから作られるため、原材料は同じ種類の単量体となります。例えば、ポリエチレンはエチレンから作られ、ポリプロピレンはプロピレンから作られます。
これらのモノマーはそれぞれ異なる特性を持ち、ホモポリマーの最終的な特性に影響を与えます。例えば、エチレンから作られたポリエチレンは柔らかく、プロピレンから作られたポリプロピレンは硬い性質を持ちます。したがって、原材料が与える影響を理解することで、製品の選択や設計に役立ちます。ホモポリマーの基点である原材料は、製品の特性や用途に大きな影響を及ぼす重要な要素です。
プラスチック代替素材の研究と展望
ホモポリマーの基点!理解しておきたい原材料とその特性
ホモポリマーは、私たちの日常生活に欠かせない素材の一つです。身近な製品にも使われていて、その特性によってさまざまな用途に活用されています。ホモポリマーを作るための原材料は、石油から作られる炭化水素を主成分としています。この炭化水素は、重合反応を経て長い鎖状の分子構造を持ったポリマーになります。
例えば、ポリエチレンはビニール袋やペットボトルなどに使用され、ポリプロピレンは容器や衣類、車の部品に利用されます。ホモポリマーは、その特性によって硬さや柔軟性、耐熱性などが異なり、さまざまな製品に適した素材として使われています。理解しておくことで、製品の性質や使い道をより深く理解できるでしょう。
プラスチックの豆知識とお役立ち情報
プラスチックの豆知識
ホモポリマーの基本となる原材料や特性を理解することは重要です。ホモポリマーは、同じ種類の単量体から作られる重合体で、一般的なプラスチック製品の材料として広く使われています。このようなポリマーは、加工性や耐久性に優れている特性があります。たとえば、ポリエチレンは柔らかく耐久性があり、ポリプロピレンは内部の圧力に強い特性があります。これらの特性は、製品の用途や要件に合わせて適切なホモポリマーを選ぶ際に重要です。したがって、材料の原料や特性を理解することで、効果的なプラスチック製品の製造や利用が可能となります。
プラスチックの選び方と購入ガイド
ホモポリマーの基点!理解しておきたい原材料とその特性
ホモポリマーは、様々な製品や素材に使われる重要な材料です。原材料として使われるポリマーは、プラスチック製品の特性や品質に大きな影響を与えます。例えば、ポリエチレンは柔らかくて耐久性があり、ポリプロピレンは耐熱性に優れています。これらの特性を理解することは、製品選びや使用方法に役立ちます。
ホモポリマーの原材料選びは重要です。ポリエチレンやポリプロピレンなどの特性を理解し、製品の要件に合った材料を選ぶことが大切です。例えば、耐久性が求められる製品にはポリエチレンが適しています。品質や性能を考慮して、適切なホモポリマーを選ぶことで、製品の品質向上や耐久性の向上が期待できます。
プラスチック製品の正しい使い方とメンテナンス
ホモポリマーの基点!理解しておきたい原材料とその特性
ホモポリマーは、日常生活で多く使用されるプラスチック製品の一種です。ホモポリマーの特性や性能を理解するためには、その原材料を知ることが重要です。ホモポリマーの原材料は、石油から得られる化学物質を主成分としています。この化学物質は、石油製品の加工過程で得られ、プラスチック製品を作る際に加工されます。
例えば、ポリエチレンはホモポリマーの一種で、ビニール袋やプラスチックボトルなどに広く使用されています。ポリプロピレンは、食品容器や繊維製品などに利用されます。これらの原材料がホモポリマー製品の特性や用途に影響を与えています。
原材料の種類や配合比率によって、ホモポリマーの硬さや柔軟性、耐久性などが異なります。理解を深めることで、プラスチック製品を適切に利用し、長く使えるメンテナンス方法を実践することが大切です。
まとめ
ホモポリマーは、原材料によってその特性が大きく異なります。一般に使用される原材料には、エチレン、プロピレン、スチレンなどがあります。これらの原材料を組み合わせることで、様々な特性を持ったホモポリマーが製造されます。特定の原材料を使用することで、硬度、耐熱性、耐候性などが向上するため、製品の用途に応じて適切な原材料の選択が重要です。ホモポリマーの特性を理解し、適切な原材料を選択することで、製品の品質向上につながることでしょう。
耐熱性は重要!樹脂材料の連続使用温度解説
耐熱性は樹脂材料を選ぶ際に重要な要素の一つです。樹脂材料の連続使用温度が知られていることは、製品の性能や安全性を確保する上で不可欠です。例えば、高温で連続使用される製品では、材料がそれに耐えられることが求められます。
この記事では、樹脂材料の連続使用温度に焦点を当て、その重要性や影響について解説します。樹脂材料を選ぶ際に知っておくべきことや、連続使用温度が製品の信頼性に与える影響について詳しく紹介します。耐熱性に関する知識が製品開発や選定の際に役立つこと間違いありません。ご一読いただき、樹脂材料の連続使用温度について理解を深めてみてください。
樹脂材料とは
樹脂材料の基本的な特性
樹脂材料の基本的な特性について理解することは重要です。その中でも、耐熱性は特に注目される要素です。樹脂材料の連続使用温度とは、その材料が長時間にわたって使用できる最高温度を示します。例えば、自動車のエンジンルーム内など、高温環境下で使用される部品には高い耐熱性が求められます。
耐熱性が不足していると、樹脂材料は変形や劣化を起こし、機能を果たせなくなる可能性があります。したがって、連続使用温度を正しく把握し、適切な材料を選択することが重要です。例えば、耐熱性に優れたポリイミド樹脂は、高温下でも安定した性能を発揮します。
樹脂材料の連続使用温度を考慮することで、製品の信頼性や耐久性を向上させることができます。そのため、樹脂材料を選ぶ際には、連続使用温度に注目して適切な材料を選ぶことが大切です。
樹脂材料の種類と用途
耐熱性は樹脂材料を選ぶ際に重要な要素です。樹脂材料は様々な種類があり、連続使用温度も各種によって異なります。例えば、ポリエチレンは比較的低い温度までしか耐えられませんが、ポリアミドは高温でも安定した性能を保ちます。これらの違いは、樹脂材料の用途に直結します。
自動車部品のような高温環境で使われる場合、ポリアミドが適しています。一方で、プラスチック容器のような一般家庭用途にはポリエチレンが適しています。樹脂材料を選ぶ際には、連続使用温度に注目することが重要です。
したがって、樹脂材料の連続使用温度を考慮して適切な材料を選ぶことが、製品の性能や耐久性を確保する上で重要です。
熱による樹脂の変形と劣化のメカニズム
耐熱性は重要!樹脂材料の連続使用温度解説
樹脂は熱によって変形や劣化することがあります。連続使用温度とは、樹脂が安定して機能するために保たれる必要のある温度範囲を指します。例えば、車のエンジンルーム内では高温にさらされるため、そこで使用される樹脂材料は高い耐熱性が求められます。
樹脂材料の中には、特定の温度以上になると変形や劣化が進んでしまうものもあります。したがって、適切な連続使用温度を選定することは製品の性能や寿命を確保するために重要です。
例えば、自動車部品や航空機部品など、厳しい環境下で使用される製品では、連続使用温度を考慮した樹脂材料の選定が欠かせません。適切な材料選定により、安全性や信頼性を高めることができます。
樹脂材料の連続使用温度
連続使用温度の定義
連続使用温度とは、樹脂材料が長時間にわたって安定して使用できる最高温度のことを指します。この耐熱性は、製品が適切に機能し続けるために非常に重要です。例えば、自動車部品や電子機器など、さまざまな産業で使用される樹脂製品は、高温下で長時間使用されることがあります。連続使用温度が適切でないと、樹脂材料は劣化し、製品の性能が低下する可能性があります。したがって、製品設計や材料選定の段階で連続使用温度を考慮することが重要です。適切な連続使用温度を持つ樹脂材料を選択することで、製品の信頼性と耐久性を確保できます。
連続使用温度の重要性
樹脂材料の連続使用温度は、製品の性能と耐久性に直結する重要な要素です。例えば、ある樹脂は特定の温度以上になると変形や破損する可能性があります。このため、適切な連続使用温度を設定することが必要です。
連続使用温度を理解するためには、樹脂の分子構造や熱伝導率などの物性を考慮することが重要です。例えば、ポリエチレンは比較的低い温度で溶け始める性質がありますが、ポリアミドは高温でも安定しています。
したがって、製品の使用環境や目的に合わせて適切な樹脂材料を選定し、適切な連続使用温度を設定することが重要です。これにより製品の信頼性や安全性を確保し、最適な性能を引き出すことができます。
連続使用温度の測定方法
耐熱性は樹脂材料を評価する際に非常に重要です。樹脂材料の連続使用温度とは、その材料が長時間にわたって安定して使用できる温度のことを指します。この温度は、樹脂の性能や安定性を確保するために把握しておく必要があります。
連続使用温度を測定する方法には、様々な手法があります。一般的な方法としては、熱重量分析法や熱歪み温度測定法が挙げられます。これらの方法を使用して、樹脂材料がどの温度範囲で安定して使用できるのかを評価します。
例えば、自動車部品や電子機器など、様々な製品には樹脂材料が使われています。これらの製品が長期間にわたって正常に機能するためには、連続使用温度が重要な要素となります。
樹脂材料の連続使用温度を理解することで、製品開発や設計段階での適切な材料選定が可能となり、製品の品質向上につながります。
耐熱性に関する樹脂材料の選び方
耐熱性が必要なアプリケーション
耐熱性は樹脂材料の重要な特性の一つです。連続使用温度とは、その材料が長期間にわたって安定して使用できる温度のことを指します。例えば、自動車エンジンルーム内や電子機器の筐体など、高温環境下で使用される部品や製品には耐熱性が欠かせません。
日本の自動車産業では、エンジンコンポーネントや車内部品など、樹脂材料の耐熱性が求められています。特に夏場の高温時においても安定した性能を発揮することが重要です。このような要求に応えるため、熱可塑性樹脂や耐熱性樹脂が開発されています。
樹脂材料の連続使用温度を理解することで、製品の信頼性や耐久性を向上させることができます。したがって、耐熱性に注目しながら適切な樹脂材料を選択することが重要です。
選び方のポイント
耐熱性は重要!樹脂材料の連続使用温度解説
樹脂材料を選ぶ際に連続使用温度を考慮することは非常に重要です。なぜなら、材料が設計された温度を超えると、強度や性能が低下し、最悪の場合、破損する可能性があるからです。例えば、自動車部品や電子機器など、日常生活で使われる製品には樹脂材料が使用されており、連続使用温度が適切でない場合、安全性や信頼性に問題が生じる恐れがあります。
選ぶ際のポイントは、具体的な温度要件に応じて適切な樹脂を選定することです。例えば、ポリプロピレンは高い連続使用温度を持つため、高温環境で使用される部品に適しています。一方で、ポリエチレンは低温に強いため、冷凍庫などの冷却環境に適しています。適切な樹脂を選択することで製品の耐久性や安全性を確保し、品質向上につなげることができます。
コストと性能のバランス
樹脂材料の連続使用温度は、耐熱性という重要な性質です。連続使用温度とは、材料が維持できる最高温度であり、これを超えると物性が変化する可能性があります。例えば、車のエンジンルームなど高温環境下で使用される部品には、高い耐熱性が求められます。
樹脂材料は、耐熱性の向上に取り組まれており、そのバランスがコストと性能に影響します。高耐熱性を持つ材料は製品寿命を延ばし、安全性を向上させる一方、製造コストが上がる可能性もあります。
このように、樹脂材料の連続使用温度は製品設計や選定において重要な要素となります。適切な耐熱性を持つ材料を選ぶことで、製品の性能と安全性を確保することができます。
プラスチックの耐熱温度についての理解
耐熱温度とは
耐熱性は重要!樹脂材料の連続使用温度解説
樹脂材料の連続使用温度とは、熱に対する耐性を示す重要な指標です。例えば、樹脂製品が長時間にわたって高温で使用される場合、その樹脂の性能が維持されるかどうかは連続使用温度に依存します。樹脂は温度が上昇すると柔らかくなり、強度や寸法安定性が損なわれることがあります。
連続使用温度を理解するためには、樹脂の種類や製品の使用状況によって異なることを考慮する必要があります。例えば、自動車部品や電子機器などの分野では、高い耐熱性が求められます。そのため、適切な樹脂材料を選択することが重要です。樹脂材料の連続使用温度を十分に理解し、適切な選択を行うことで製品の性能向上や安全性確保につながります。
耐熱温度の範囲と樹脂選択
耐熱性は重要!樹脂材料の連続使用温度解説
樹脂材料を選ぶ際に重要な要素の一つが連続使用温度です。樹脂は熱によって性質が変化するため、適切な環境での使用が必要です。
樹脂の連続使用温度は、その材料が長期間にわたって安定して使用できる温度範囲を示します。例えば、ポリエチレンは比較的低い温度で使えますが、ポリアミドは高温にも耐えられます。
このように、樹脂の連続使用温度を理解することで、適切な材料を選択できます。環境や用途に合わせて適切な耐熱性を持つ樹脂を選ぶことが重要です。樹脂の選択を誤ると、製品の性能や安全性に影響を及ぼす可能性があります。使い方を理解し、適切な樹脂を選ぶことが大切です。
耐熱性を左右する要因
耐熱性は、樹脂材料がどれだけ高温に耐えられるかを示す重要な性質です。樹脂の連続使用温度は、製品や部品の長期的な安定性や性能に大きく影響します。例えば、車のエンジンルーム内では高温が発生するため、そこで使われる樹脂材料は耐熱性が求められます。
耐熱性を左右する要因は、素材の組成や添加剤、加工方法などがあります。繊維強化樹脂は耐熱性が高いため、自動車部品や航空機部品によく使用されています。
したがって、樹脂材料の連続使用温度を理解し、適切に選択することは製品の耐久性や安全性を確保するうえで重要です。耐熱性に優れた樹脂材料を選ぶことで、製品の品質向上や信頼性の向上につながるでしょう。
熱に強い樹脂の特徴と比較
代表的な耐熱性樹脂の紹介
耐熱性は、樹脂材料において非常に重要です。樹脂は熱を受けると変形したり融解したりする性質がありますが、耐熱性が高いとその特性を長期間維持できるのです。例えば、ポリアミド(ナイロン)やポリエーテルエーテルケトン(PEEK)などの樹脂は、高温下でも安定した性能を発揮します。これにより、自動車部品や産業機械部品など、高温環境で使用される製品に適しています。連続使用温度が高い樹脂は、厳しい環境下での信頼性を高めるだけでなく、製品寿命を延ばすことにもつながります。耐熱性が備わっていることは、製品の品質や安全性にも直結する重要な要素です。
各樹脂の耐熱性能比較
耐熱性は、樹脂材料を選ぶ際に非常に重要な要素です。樹脂の連続使用温度は、その材料がどれだけ高温で安定して使用できるかを示します。例えば、ポリエーテルエーテルケトン(PEEK)は、約250度の高い連続使用温度を持ち、自動車部品や産業機械部品などの高温環境での使用に適しています。一方、ポリプロピレンは連続使用温度が約100度と比較的低く、低温環境向けの製品に適しています。
したがって、樹脂材料を選択する際には、その連続使用温度を考慮することが重要です。高温での安定性が必要な場合には、PEEKのような耐熱性に優れた材料を選ぶことが適しています。樹脂材料の適切な選択により、製品の性能や耐久性を確保することができます。
使用環境に応じた耐熱樹脂の選定
樹脂材料の連続使用温度は、製品がどれだけ高温環境に耐えられるかを示す重要な要素です。この連続使用温度が低いと、樹脂が溶解したり変形したりする可能性が高まります。例えば、自動車エンジンの部品や電子機器など、高温で動作する製品では、高い耐熱性が求められます。逆に、一般家庭用品などの低温環境で使用される製品では、連続使用温度がそれほど重要ではありません。
適切な耐熱性を持つ樹脂を選定することで、製品の耐久性や安全性を確保することができます。日常生活に欠かせない様々な製品の中で、耐熱性が重要な役割を果たしていることが分かります。樹脂材料の連続使用温度を考慮することは製品の品質向上につながります。
耐熱性高分子材料の詳細
高分子材料の耐熱性能と構造
耐熱性は樹脂材料の重要な特性の一つです。連続使用温度とは、その樹脂が長期間にわたって安定して使用できる温度のことを指します。例えば、樹脂製のパーツが高温環境下で使用される場合、その樹脂が連続使用温度を超えると変形や劣化が進み、機能を果たせなくなる可能性があります。したがって、製品や部品を設計する際には、材料の耐熱性能を考慮することが重要です。樹脂材料の中には高温に耐えられるものもありますが、適切な材料選定や製品設計が必要です。材料の適正な連続使用温度を把握し、それに基づいて製品を設計することが、安定した製品性能を確保するために欠かせません。
耐熱性高分子材料の開発動向
耐熱性は樹脂材料の重要な特性の1つです。樹脂材料の連続使用温度とは、その材料が長時間にわたって持続的に使用できる最高温度を指します。例えば、自動車のエンジンルーム内や電子機器の筐体内など、高温の環境下で使用される製品では、耐熱性が重要になります。
近年、耐熱性高分子材料の開発が進んでいます。これにより、樹脂製品の利用範囲が広がり、耐熱性が求められるさまざまな分野で活躍しています。例えば、航空宇宙産業での使用や自動車部品、医療機器などでの応用が増えています。
樹脂材料の連続使用温度が高いほど、それを使った製品の耐久性や信頼性が向上します。したがって、耐熱性の高い樹脂材料の開発は産業界にとって重要な課題となっています。
耐熱性と他の物性との関連性
樹脂材料の連続使用温度は、耐熱性を示す重要な指標です。樹脂は高温になると変形したり劣化したりするため、連続使用温度が低い場合、長期間の安定した使用が難しくなります。例えば、自動車部品や電子機器など、多くの製品で樹脂材料が使用されています。それらの製品が高温環境下で正常に機能するためには、適切な耐熱性が求められます。
耐熱性が不十分な樹脂材料を使用すると、例えば自動車のエンジンルーム内などの高温環境で部品が劣化し、安全性や耐久性が損なわれる可能性があります。そのため、樹脂材料の連続使用温度を正しく理解し、適切に選択することが重要です。
実例から学ぶ耐熱性樹脂の活用
工業分野における耐熱樹脂の事例
樹脂材料の連続使用温度とは、特定の樹脂が維持できる温度範囲を示します。工業分野では、耐熱性の高い樹脂が重要です。例えば、自動車部品や電子機器など、高温環境下で安定した性能を発揮する必要があります。
耐熱樹脂の事例として、ポリイミド樹脂があります。ポリイミドは高い耐熱性と機械的強度を持ち、航空宇宙や医療機器などで幅広く使用されています。また、ポリエーテルエーテルケトン(PEEK)も高い連続使用温度を持ち、機械部品や化学機器などに適しています。
樹脂の選択においては、連続使用温度を考慮することが重要です。適切な樹脂を選ぶことで、製品の信頼性や耐久性を確保することができます。耐熱性を持つ樹脂の活用により、工業製品の性能向上に貢献することが期待されています。
日常生活における耐熱樹脂の事例
耐熱性は樹脂材料の重要な特性です。連続使用温度とは、その材料が持続して耐えられる温度範囲を示す指標です。例えば、自動車部品や家電製品に使用される樹脂は、高温で安定した性能を示さなければなりません。これは、エンジンルーム内や電子機器の近くなど、高温環境での使用を考慮しています。
樹脂材料の連続使用温度が低いと、熱変形や劣化が起こりやすくなります。そのため、適切な耐熱性能を持つ樹脂を選択することが重要です。例えば、ポリイミド樹脂は高い連続使用温度を持ち、航空宇宙産業などで広く使用されています。
耐熱性の高い樹脂を選ぶことで製品の耐久性や安全性が向上し、幅広い産業分野で活躍します。樹脂材料の選択において、連続使用温度を考慮することは欠かせません。
耐熱性樹脂の将来的な応用展望
耐熱性は、樹脂材料の品質を評価する上で非常に重要です。樹脂がどの程度の高温に耐えられるかは、その素材がどれくらいの環境で使用できるかを示す指標となります。例えば、自動車のエンジンルームや電子機器の基板など、高温環境下で使用される製品には耐熱性が求められます。
連続使用温度とは、材料が長時間にわたって特定の温度下で使用される際の安定性を示す重要な性能です。例えば、特定の樹脂は150℃で連続使用されることが許容されているが、それを超えると劣化や変形が起こる可能性があります。
したがって、樹脂材料の連続使用温度を理解し、適切に選定することは製品の信頼性や性能向上につながります。将来的には、さらなる耐熱性樹脂の開発が進み、様々な産業分野での応用が期待されています。
耐熱性樹脂の選定と設計への応用
設計段階での耐熱性の考慮
耐熱性の重要性は、樹脂材料の設計段階で考慮するべき要素です。樹脂材料は特定の温度以上になると変形や劣化が発生するため、連続使用温度を正しく把握することが不可欠です。例えば、車載部品や家電製品などの高温環境下で使用される製品では、耐熱性が求められます。
連続使用温度を適切に設定するためには、樹脂材料の特性を理解し、製品がどのような環境で使用されるかを考慮する必要があります。例えば、ポリアミド樹脂は高い耐熱性を持つため、エンジン部品などの高温環境に適しています。
したがって、設計段階で耐熱性を適切に考慮することで、製品の性能や耐久性を向上させることができます。樹脂材料の連続使用温度を正しく把握し、適切な材料を選択することが重要です。
耐熱性樹脂の加工方法と注意点
耐熱性樹脂の加工方法と注意点
樹脂材料の連続使用温度は、製品の耐熱性能を示す重要な指標です。高い連続使用温度を持つ樹脂は、高温環境下で安定した性能を発揮し、安全性を確保することができます。
連続使用温度が低い樹脂は、高温で使用する場合には注意が必要です。例えば、自動車部品や電子機器など、高温環境で使用される製品には、耐熱性の高い樹脂が求められます。
そのため、製品の使用環境や条件に合わせて適切な樹脂材料を選定することが重要です。製品の安全性や信頼性を確保するためには、連続使用温度に注目し、適切な加工方法と注意点を把握することが欠かせません。
耐熱性樹脂の選定チェックリスト
耐熱性は樹脂材料を選ぶ際に重要な要素です。樹脂の連続使用温度は、その材料がどれだけ高温環境で安定して使えるかを示します。例えば、自動車部品や電子機器のケーシングなど、様々な分野で耐熱性が求められています。
樹脂材料を選ぶ際には、連続使用温度だけでなく、耐候性や耐薬品性などの特性も考慮する必要があります。例えば、ポリエーテルエーテルケトン(PEEK)は高い耐熱性と耐薬品性を持ち、航空宇宙や医療機器などの分野で広く使用されています。
樹脂材料を選ぶ際は、適切なチェックリストを作成し、必要な特性を確認することが重要です。耐熱性は製品の信頼性や耐久性に直結するため、慎重な選定が求められます。
Q&A:耐熱性樹脂材料に関するよくある質問
耐熱性樹脂の選択に関する疑問
耐熱性は、樹脂材料を選ぶ際に重要な要素です。連続使用温度が高いほど、樹脂は高温環境で安定して機能します。例えば、自動車エンジンルーム内では高温が発生するため、耐熱性のある樹脂が必要とされます。逆に、連続使用温度が低い樹脂は一定温度を超えると変形や劣化が進みます。一般家庭で使用される樹脂製品でも、耐熱性が不十分だと長期間の使用に耐えられない可能性があります。したがって、樹脂材料を選ぶ際には連続使用温度に注目し、使用環境に適したものを選ぶことが重要です。耐熱性が高い樹脂を選ぶことで、製品の信頼性や耐久性を向上させることができます。
耐熱性能を最大限に活かす方法
耐熱性は樹脂材料を選ぶ際に重要な要素です。樹脂は高温になると変形したり溶けたりすることがありますが、それを防ぐために連続使用温度という指標があります。連続使用温度とは、樹脂が長期間にわたって安定して使える温度のことです。
樹脂の連続使用温度は、その素材の特性によって異なります。例えば、ポリプロピレンは比較的低い温度で使用できますが、ポリエーテルイミドは高温にも耐えられます。このように、樹脂ごとに連続使用温度は異なるため、使用する環境や条件に応じて適切な樹脂材料を選ぶことが重要です。
したがって、耐熱性を最大限に活かすためには、想定される温度範囲内で安定して性能を発揮する樹脂を選ぶことが大切です。適切な連続使用温度を選定することで、樹脂材料の効果的な活用が可能となります。
耐熱性に関する誤解とその訂正
樹脂材料の連続使用温度は、製品の性能や耐久性に大きな影響を与えます。多くの方が耐熱性を見落としてしまう傾向がありますが、実際には非常に重要な要素です。例えば、樹脂製の部品や機器が高温環境で使われる場合、連続使用温度を超えると変形したり劣化したりする可能性があります。
樹脂材料の中には高温に耐えられるものもありますが、それぞれの材料には連続使用できる温度が設定されています。このため、製品を設計する際には適切な材料を選択することが重要です。連続使用温度を正しく把握し、適切な材料を選ぶことで製品の寿命を延ばし、安全性を確保することができます。
耐熱性樹脂の安全性と環境への配慮
耐熱性樹脂の健康への影響
耐熱性は、樹脂材料の大切な特性の一つです。連続使用温度とは、その樹脂が安定して機能することができる温度のことを指します。例えば、自動車のエンジンルーム内など、高温環境下で使われる部品には、耐熱性の高い樹脂が必要です。日常生活でも、電子機器や調理器具など様々な製品に耐熱性樹脂が使われています。
樹脂材料の連続使用温度が適切でないと、熱による劣化や変形が起こり、製品の寿命や安全性が損なわれる可能性があります。したがって、製品の使用環境に応じて適切な耐熱性樹脂を選択することが重要です。耐熱性樹脂の適切な選択は、製品の信頼性向上や人々の健康への影響にも繋がる重要な要素と言えます。
環境保護と耐熱性樹脂の関係
耐熱性は樹脂材料の重要な特性の一つです。連続使用温度とは、樹脂が安定して使われることができる最高温度を指します。例えば、自動車部品や家電製品など、さまざまな分野で耐熱性が求められます。日本では、高温多湿の環境が一般的であり、耐熱性の高い樹脂材料が重要です。具体的には、自動車のエンジンルームや家電製品の基盤などが連続使用温度の高い樹脂で作られています。環境保護の観点からも、耐熱性のある樹脂材料は長期間使われるため、廃棄物の削減につながります。したがって、樹脂材料の連続使用温度を考慮することは、製品の耐久性向上や環境への配慮にもつながる重要な要素と言えます。
サステナビリティと耐熱性樹脂の未来
耐熱性は樹脂材料にとって非常に重要です。樹脂は熱によって変形しやすい素材であり、連続使用温度が設定温度を超えると品質が損なわれる可能性があります。例えば、自動車のエンジンで使用される樹脂部品は、高温環境下で安定して機能する必要があります。耐熱性が不足していると、エンジンの性能低下や部品の劣化が起こり、安全性や信頼性に影響を及ぼす可能性があります。したがって、様々な産業分野において耐熱性の高い樹脂材料の需要が高まっています。連続使用温度を考慮した適切な材料選択や設計が重要であり、これによって製品の信頼性や耐久性を向上させることができます。結果として、耐熱性樹脂は産業界の未来において重要な役割を果たすことが期待されています。
まとめ
樹脂材料の連続使用温度は重要な要素です。これは樹脂材料の耐熱性能を示し、製品の適切な使用条件を決定する上で重要な指標です。樹脂材料の連続使用温度は、製品が長期間にわたって特定の温度で使用される際の性能を示しています。製品設計や材料選定において、この連続使用温度を把握することは重要です。設計や製造プロセスにおいて樹脂材料の耐熱性能を考慮することで、製品の信頼性や耐久性を向上させることが可能です。
耐熱性は重要!樹脂材料の連続使用温度解説
耐熱性は樹脂材料を選ぶ際に重要な要素の一つです。樹脂材料の連続使用温度が知られていることは、製品の性能や安全性を確保する上で不可欠です。例えば、高温で連続使用される製品では、材料がそれに耐えられることが求められます。
この記事では、樹脂材料の連続使用温度に焦点を当て、その重要性や影響について解説します。樹脂材料を選ぶ際に知っておくべきことや、連続使用温度が製品の信頼性に与える影響について詳しく紹介します。耐熱性に関する知識が製品開発や選定の際に役立つこと間違いありません。ご一読いただき、樹脂材料の連続使用温度について理解を深めてみてください。
樹脂材料とは
樹脂材料の基本的な特性
樹脂材料の基本的な特性について理解することは重要です。その中でも、耐熱性は特に注目される要素です。樹脂材料の連続使用温度とは、その材料が長時間にわたって使用できる最高温度を示します。例えば、自動車のエンジンルーム内など、高温環境下で使用される部品には高い耐熱性が求められます。
耐熱性が不足していると、樹脂材料は変形や劣化を起こし、機能を果たせなくなる可能性があります。したがって、連続使用温度を正しく把握し、適切な材料を選択することが重要です。例えば、耐熱性に優れたポリイミド樹脂は、高温下でも安定した性能を発揮します。
樹脂材料の連続使用温度を考慮することで、製品の信頼性や耐久性を向上させることができます。そのため、樹脂材料を選ぶ際には、連続使用温度に注目して適切な材料を選ぶことが大切です。
樹脂材料の種類と用途
耐熱性は樹脂材料を選ぶ際に重要な要素です。樹脂材料は様々な種類があり、連続使用温度も各種によって異なります。例えば、ポリエチレンは比較的低い温度までしか耐えられませんが、ポリアミドは高温でも安定した性能を保ちます。これらの違いは、樹脂材料の用途に直結します。
自動車部品のような高温環境で使われる場合、ポリアミドが適しています。一方で、プラスチック容器のような一般家庭用途にはポリエチレンが適しています。樹脂材料を選ぶ際には、連続使用温度に注目することが重要です。
したがって、樹脂材料の連続使用温度を考慮して適切な材料を選ぶことが、製品の性能や耐久性を確保する上で重要です。
熱による樹脂の変形と劣化のメカニズム
耐熱性は重要!樹脂材料の連続使用温度解説
樹脂は熱によって変形や劣化することがあります。連続使用温度とは、樹脂が安定して機能するために保たれる必要のある温度範囲を指します。例えば、車のエンジンルーム内では高温にさらされるため、そこで使用される樹脂材料は高い耐熱性が求められます。
樹脂材料の中には、特定の温度以上になると変形や劣化が進んでしまうものもあります。したがって、適切な連続使用温度を選定することは製品の性能や寿命を確保するために重要です。
例えば、自動車部品や航空機部品など、厳しい環境下で使用される製品では、連続使用温度を考慮した樹脂材料の選定が欠かせません。適切な材料選定により、安全性や信頼性を高めることができます。
樹脂材料の連続使用温度
連続使用温度の定義
連続使用温度とは、樹脂材料が長時間にわたって安定して使用できる最高温度のことを指します。この耐熱性は、製品が適切に機能し続けるために非常に重要です。例えば、自動車部品や電子機器など、さまざまな産業で使用される樹脂製品は、高温下で長時間使用されることがあります。連続使用温度が適切でないと、樹脂材料は劣化し、製品の性能が低下する可能性があります。したがって、製品設計や材料選定の段階で連続使用温度を考慮することが重要です。適切な連続使用温度を持つ樹脂材料を選択することで、製品の信頼性と耐久性を確保できます。
連続使用温度の重要性
樹脂材料の連続使用温度は、製品の性能と耐久性に直結する重要な要素です。例えば、ある樹脂は特定の温度以上になると変形や破損する可能性があります。このため、適切な連続使用温度を設定することが必要です。
連続使用温度を理解するためには、樹脂の分子構造や熱伝導率などの物性を考慮することが重要です。例えば、ポリエチレンは比較的低い温度で溶け始める性質がありますが、ポリアミドは高温でも安定しています。
したがって、製品の使用環境や目的に合わせて適切な樹脂材料を選定し、適切な連続使用温度を設定することが重要です。これにより製品の信頼性や安全性を確保し、最適な性能を引き出すことができます。
連続使用温度の測定方法
耐熱性は樹脂材料を評価する際に非常に重要です。樹脂材料の連続使用温度とは、その材料が長時間にわたって安定して使用できる温度のことを指します。この温度は、樹脂の性能や安定性を確保するために把握しておく必要があります。
連続使用温度を測定する方法には、様々な手法があります。一般的な方法としては、熱重量分析法や熱歪み温度測定法が挙げられます。これらの方法を使用して、樹脂材料がどの温度範囲で安定して使用できるのかを評価します。
例えば、自動車部品や電子機器など、様々な製品には樹脂材料が使われています。これらの製品が長期間にわたって正常に機能するためには、連続使用温度が重要な要素となります。
樹脂材料の連続使用温度を理解することで、製品開発や設計段階での適切な材料選定が可能となり、製品の品質向上につながります。
耐熱性に関する樹脂材料の選び方
耐熱性が必要なアプリケーション
耐熱性は樹脂材料の重要な特性の一つです。連続使用温度とは、その材料が長期間にわたって安定して使用できる温度のことを指します。例えば、自動車エンジンルーム内や電子機器の筐体など、高温環境下で使用される部品や製品には耐熱性が欠かせません。
日本の自動車産業では、エンジンコンポーネントや車内部品など、樹脂材料の耐熱性が求められています。特に夏場の高温時においても安定した性能を発揮することが重要です。このような要求に応えるため、熱可塑性樹脂や耐熱性樹脂が開発されています。
樹脂材料の連続使用温度を理解することで、製品の信頼性や耐久性を向上させることができます。したがって、耐熱性に注目しながら適切な樹脂材料を選択することが重要です。
選び方のポイント
耐熱性は重要!樹脂材料の連続使用温度解説
樹脂材料を選ぶ際に連続使用温度を考慮することは非常に重要です。なぜなら、材料が設計された温度を超えると、強度や性能が低下し、最悪の場合、破損する可能性があるからです。例えば、自動車部品や電子機器など、日常生活で使われる製品には樹脂材料が使用されており、連続使用温度が適切でない場合、安全性や信頼性に問題が生じる恐れがあります。
選ぶ際のポイントは、具体的な温度要件に応じて適切な樹脂を選定することです。例えば、ポリプロピレンは高い連続使用温度を持つため、高温環境で使用される部品に適しています。一方で、ポリエチレンは低温に強いため、冷凍庫などの冷却環境に適しています。適切な樹脂を選択することで製品の耐久性や安全性を確保し、品質向上につなげることができます。
コストと性能のバランス
樹脂材料の連続使用温度は、耐熱性という重要な性質です。連続使用温度とは、材料が維持できる最高温度であり、これを超えると物性が変化する可能性があります。例えば、車のエンジンルームなど高温環境下で使用される部品には、高い耐熱性が求められます。
樹脂材料は、耐熱性の向上に取り組まれており、そのバランスがコストと性能に影響します。高耐熱性を持つ材料は製品寿命を延ばし、安全性を向上させる一方、製造コストが上がる可能性もあります。
このように、樹脂材料の連続使用温度は製品設計や選定において重要な要素となります。適切な耐熱性を持つ材料を選ぶことで、製品の性能と安全性を確保することができます。
プラスチックの耐熱温度についての理解
耐熱温度とは
耐熱性は重要!樹脂材料の連続使用温度解説
樹脂材料の連続使用温度とは、熱に対する耐性を示す重要な指標です。例えば、樹脂製品が長時間にわたって高温で使用される場合、その樹脂の性能が維持されるかどうかは連続使用温度に依存します。樹脂は温度が上昇すると柔らかくなり、強度や寸法安定性が損なわれることがあります。
連続使用温度を理解するためには、樹脂の種類や製品の使用状況によって異なることを考慮する必要があります。例えば、自動車部品や電子機器などの分野では、高い耐熱性が求められます。そのため、適切な樹脂材料を選択することが重要です。樹脂材料の連続使用温度を十分に理解し、適切な選択を行うことで製品の性能向上や安全性確保につながります。
耐熱温度の範囲と樹脂選択
耐熱性は重要!樹脂材料の連続使用温度解説
樹脂材料を選ぶ際に重要な要素の一つが連続使用温度です。樹脂は熱によって性質が変化するため、適切な環境での使用が必要です。
樹脂の連続使用温度は、その材料が長期間にわたって安定して使用できる温度範囲を示します。例えば、ポリエチレンは比較的低い温度で使えますが、ポリアミドは高温にも耐えられます。
このように、樹脂の連続使用温度を理解することで、適切な材料を選択できます。環境や用途に合わせて適切な耐熱性を持つ樹脂を選ぶことが重要です。樹脂の選択を誤ると、製品の性能や安全性に影響を及ぼす可能性があります。使い方を理解し、適切な樹脂を選ぶことが大切です。
耐熱性を左右する要因
耐熱性は、樹脂材料がどれだけ高温に耐えられるかを示す重要な性質です。樹脂の連続使用温度は、製品や部品の長期的な安定性や性能に大きく影響します。例えば、車のエンジンルーム内では高温が発生するため、そこで使われる樹脂材料は耐熱性が求められます。
耐熱性を左右する要因は、素材の組成や添加剤、加工方法などがあります。繊維強化樹脂は耐熱性が高いため、自動車部品や航空機部品によく使用されています。
したがって、樹脂材料の連続使用温度を理解し、適切に選択することは製品の耐久性や安全性を確保するうえで重要です。耐熱性に優れた樹脂材料を選ぶことで、製品の品質向上や信頼性の向上につながるでしょう。
熱に強い樹脂の特徴と比較
代表的な耐熱性樹脂の紹介
耐熱性は、樹脂材料において非常に重要です。樹脂は熱を受けると変形したり融解したりする性質がありますが、耐熱性が高いとその特性を長期間維持できるのです。例えば、ポリアミド(ナイロン)やポリエーテルエーテルケトン(PEEK)などの樹脂は、高温下でも安定した性能を発揮します。これにより、自動車部品や産業機械部品など、高温環境で使用される製品に適しています。連続使用温度が高い樹脂は、厳しい環境下での信頼性を高めるだけでなく、製品寿命を延ばすことにもつながります。耐熱性が備わっていることは、製品の品質や安全性にも直結する重要な要素です。
各樹脂の耐熱性能比較
耐熱性は、樹脂材料を選ぶ際に非常に重要な要素です。樹脂の連続使用温度は、その材料がどれだけ高温で安定して使用できるかを示します。例えば、ポリエーテルエーテルケトン(PEEK)は、約250度の高い連続使用温度を持ち、自動車部品や産業機械部品などの高温環境での使用に適しています。一方、ポリプロピレンは連続使用温度が約100度と比較的低く、低温環境向けの製品に適しています。
したがって、樹脂材料を選択する際には、その連続使用温度を考慮することが重要です。高温での安定性が必要な場合には、PEEKのような耐熱性に優れた材料を選ぶことが適しています。樹脂材料の適切な選択により、製品の性能や耐久性を確保することができます。
使用環境に応じた耐熱樹脂の選定
樹脂材料の連続使用温度は、製品がどれだけ高温環境に耐えられるかを示す重要な要素です。この連続使用温度が低いと、樹脂が溶解したり変形したりする可能性が高まります。例えば、自動車エンジンの部品や電子機器など、高温で動作する製品では、高い耐熱性が求められます。逆に、一般家庭用品などの低温環境で使用される製品では、連続使用温度がそれほど重要ではありません。
適切な耐熱性を持つ樹脂を選定することで、製品の耐久性や安全性を確保することができます。日常生活に欠かせない様々な製品の中で、耐熱性が重要な役割を果たしていることが分かります。樹脂材料の連続使用温度を考慮することは製品の品質向上につながります。
耐熱性高分子材料の詳細
高分子材料の耐熱性能と構造
耐熱性は樹脂材料の重要な特性の一つです。連続使用温度とは、その樹脂が長期間にわたって安定して使用できる温度のことを指します。例えば、樹脂製のパーツが高温環境下で使用される場合、その樹脂が連続使用温度を超えると変形や劣化が進み、機能を果たせなくなる可能性があります。したがって、製品や部品を設計する際には、材料の耐熱性能を考慮することが重要です。樹脂材料の中には高温に耐えられるものもありますが、適切な材料選定や製品設計が必要です。材料の適正な連続使用温度を把握し、それに基づいて製品を設計することが、安定した製品性能を確保するために欠かせません。
耐熱性高分子材料の開発動向
耐熱性は樹脂材料の重要な特性の1つです。樹脂材料の連続使用温度とは、その材料が長時間にわたって持続的に使用できる最高温度を指します。例えば、自動車のエンジンルーム内や電子機器の筐体内など、高温の環境下で使用される製品では、耐熱性が重要になります。
近年、耐熱性高分子材料の開発が進んでいます。これにより、樹脂製品の利用範囲が広がり、耐熱性が求められるさまざまな分野で活躍しています。例えば、航空宇宙産業での使用や自動車部品、医療機器などでの応用が増えています。
樹脂材料の連続使用温度が高いほど、それを使った製品の耐久性や信頼性が向上します。したがって、耐熱性の高い樹脂材料の開発は産業界にとって重要な課題となっています。
耐熱性と他の物性との関連性
樹脂材料の連続使用温度は、耐熱性を示す重要な指標です。樹脂は高温になると変形したり劣化したりするため、連続使用温度が低い場合、長期間の安定した使用が難しくなります。例えば、自動車部品や電子機器など、多くの製品で樹脂材料が使用されています。それらの製品が高温環境下で正常に機能するためには、適切な耐熱性が求められます。
耐熱性が不十分な樹脂材料を使用すると、例えば自動車のエンジンルーム内などの高温環境で部品が劣化し、安全性や耐久性が損なわれる可能性があります。そのため、樹脂材料の連続使用温度を正しく理解し、適切に選択することが重要です。
実例から学ぶ耐熱性樹脂の活用
工業分野における耐熱樹脂の事例
樹脂材料の連続使用温度とは、特定の樹脂が維持できる温度範囲を示します。工業分野では、耐熱性の高い樹脂が重要です。例えば、自動車部品や電子機器など、高温環境下で安定した性能を発揮する必要があります。
耐熱樹脂の事例として、ポリイミド樹脂があります。ポリイミドは高い耐熱性と機械的強度を持ち、航空宇宙や医療機器などで幅広く使用されています。また、ポリエーテルエーテルケトン(PEEK)も高い連続使用温度を持ち、機械部品や化学機器などに適しています。
樹脂の選択においては、連続使用温度を考慮することが重要です。適切な樹脂を選ぶことで、製品の信頼性や耐久性を確保することができます。耐熱性を持つ樹脂の活用により、工業製品の性能向上に貢献することが期待されています。
日常生活における耐熱樹脂の事例
耐熱性は樹脂材料の重要な特性です。連続使用温度とは、その材料が持続して耐えられる温度範囲を示す指標です。例えば、自動車部品や家電製品に使用される樹脂は、高温で安定した性能を示さなければなりません。これは、エンジンルーム内や電子機器の近くなど、高温環境での使用を考慮しています。
樹脂材料の連続使用温度が低いと、熱変形や劣化が起こりやすくなります。そのため、適切な耐熱性能を持つ樹脂を選択することが重要です。例えば、ポリイミド樹脂は高い連続使用温度を持ち、航空宇宙産業などで広く使用されています。
耐熱性の高い樹脂を選ぶことで製品の耐久性や安全性が向上し、幅広い産業分野で活躍します。樹脂材料の選択において、連続使用温度を考慮することは欠かせません。
耐熱性樹脂の将来的な応用展望
耐熱性は、樹脂材料の品質を評価する上で非常に重要です。樹脂がどの程度の高温に耐えられるかは、その素材がどれくらいの環境で使用できるかを示す指標となります。例えば、自動車のエンジンルームや電子機器の基板など、高温環境下で使用される製品には耐熱性が求められます。
連続使用温度とは、材料が長時間にわたって特定の温度下で使用される際の安定性を示す重要な性能です。例えば、特定の樹脂は150℃で連続使用されることが許容されているが、それを超えると劣化や変形が起こる可能性があります。
したがって、樹脂材料の連続使用温度を理解し、適切に選定することは製品の信頼性や性能向上につながります。将来的には、さらなる耐熱性樹脂の開発が進み、様々な産業分野での応用が期待されています。
耐熱性樹脂の選定と設計への応用
設計段階での耐熱性の考慮
耐熱性の重要性は、樹脂材料の設計段階で考慮するべき要素です。樹脂材料は特定の温度以上になると変形や劣化が発生するため、連続使用温度を正しく把握することが不可欠です。例えば、車載部品や家電製品などの高温環境下で使用される製品では、耐熱性が求められます。
連続使用温度を適切に設定するためには、樹脂材料の特性を理解し、製品がどのような環境で使用されるかを考慮する必要があります。例えば、ポリアミド樹脂は高い耐熱性を持つため、エンジン部品などの高温環境に適しています。
したがって、設計段階で耐熱性を適切に考慮することで、製品の性能や耐久性を向上させることができます。樹脂材料の連続使用温度を正しく把握し、適切な材料を選択することが重要です。
耐熱性樹脂の加工方法と注意点
耐熱性樹脂の加工方法と注意点
樹脂材料の連続使用温度は、製品の耐熱性能を示す重要な指標です。高い連続使用温度を持つ樹脂は、高温環境下で安定した性能を発揮し、安全性を確保することができます。
連続使用温度が低い樹脂は、高温で使用する場合には注意が必要です。例えば、自動車部品や電子機器など、高温環境で使用される製品には、耐熱性の高い樹脂が求められます。
そのため、製品の使用環境や条件に合わせて適切な樹脂材料を選定することが重要です。製品の安全性や信頼性を確保するためには、連続使用温度に注目し、適切な加工方法と注意点を把握することが欠かせません。
耐熱性樹脂の選定チェックリスト
耐熱性は樹脂材料を選ぶ際に重要な要素です。樹脂の連続使用温度は、その材料がどれだけ高温環境で安定して使えるかを示します。例えば、自動車部品や電子機器のケーシングなど、様々な分野で耐熱性が求められています。
樹脂材料を選ぶ際には、連続使用温度だけでなく、耐候性や耐薬品性などの特性も考慮する必要があります。例えば、ポリエーテルエーテルケトン(PEEK)は高い耐熱性と耐薬品性を持ち、航空宇宙や医療機器などの分野で広く使用されています。
樹脂材料を選ぶ際は、適切なチェックリストを作成し、必要な特性を確認することが重要です。耐熱性は製品の信頼性や耐久性に直結するため、慎重な選定が求められます。
Q&A:耐熱性樹脂材料に関するよくある質問
耐熱性樹脂の選択に関する疑問
耐熱性は、樹脂材料を選ぶ際に重要な要素です。連続使用温度が高いほど、樹脂は高温環境で安定して機能します。例えば、自動車エンジンルーム内では高温が発生するため、耐熱性のある樹脂が必要とされます。逆に、連続使用温度が低い樹脂は一定温度を超えると変形や劣化が進みます。一般家庭で使用される樹脂製品でも、耐熱性が不十分だと長期間の使用に耐えられない可能性があります。したがって、樹脂材料を選ぶ際には連続使用温度に注目し、使用環境に適したものを選ぶことが重要です。耐熱性が高い樹脂を選ぶことで、製品の信頼性や耐久性を向上させることができます。
耐熱性能を最大限に活かす方法
耐熱性は樹脂材料を選ぶ際に重要な要素です。樹脂は高温になると変形したり溶けたりすることがありますが、それを防ぐために連続使用温度という指標があります。連続使用温度とは、樹脂が長期間にわたって安定して使える温度のことです。
樹脂の連続使用温度は、その素材の特性によって異なります。例えば、ポリプロピレンは比較的低い温度で使用できますが、ポリエーテルイミドは高温にも耐えられます。このように、樹脂ごとに連続使用温度は異なるため、使用する環境や条件に応じて適切な樹脂材料を選ぶことが重要です。
したがって、耐熱性を最大限に活かすためには、想定される温度範囲内で安定して性能を発揮する樹脂を選ぶことが大切です。適切な連続使用温度を選定することで、樹脂材料の効果的な活用が可能となります。
耐熱性に関する誤解とその訂正
樹脂材料の連続使用温度は、製品の性能や耐久性に大きな影響を与えます。多くの方が耐熱性を見落としてしまう傾向がありますが、実際には非常に重要な要素です。例えば、樹脂製の部品や機器が高温環境で使われる場合、連続使用温度を超えると変形したり劣化したりする可能性があります。
樹脂材料の中には高温に耐えられるものもありますが、それぞれの材料には連続使用できる温度が設定されています。このため、製品を設計する際には適切な材料を選択することが重要です。連続使用温度を正しく把握し、適切な材料を選ぶことで製品の寿命を延ばし、安全性を確保することができます。
耐熱性樹脂の安全性と環境への配慮
耐熱性樹脂の健康への影響
耐熱性は、樹脂材料の大切な特性の一つです。連続使用温度とは、その樹脂が安定して機能することができる温度のことを指します。例えば、自動車のエンジンルーム内など、高温環境下で使われる部品には、耐熱性の高い樹脂が必要です。日常生活でも、電子機器や調理器具など様々な製品に耐熱性樹脂が使われています。
樹脂材料の連続使用温度が適切でないと、熱による劣化や変形が起こり、製品の寿命や安全性が損なわれる可能性があります。したがって、製品の使用環境に応じて適切な耐熱性樹脂を選択することが重要です。耐熱性樹脂の適切な選択は、製品の信頼性向上や人々の健康への影響にも繋がる重要な要素と言えます。
環境保護と耐熱性樹脂の関係
耐熱性は樹脂材料の重要な特性の一つです。連続使用温度とは、樹脂が安定して使われることができる最高温度を指します。例えば、自動車部品や家電製品など、さまざまな分野で耐熱性が求められます。日本では、高温多湿の環境が一般的であり、耐熱性の高い樹脂材料が重要です。具体的には、自動車のエンジンルームや家電製品の基盤などが連続使用温度の高い樹脂で作られています。環境保護の観点からも、耐熱性のある樹脂材料は長期間使われるため、廃棄物の削減につながります。したがって、樹脂材料の連続使用温度を考慮することは、製品の耐久性向上や環境への配慮にもつながる重要な要素と言えます。
サステナビリティと耐熱性樹脂の未来
耐熱性は樹脂材料にとって非常に重要です。樹脂は熱によって変形しやすい素材であり、連続使用温度が設定温度を超えると品質が損なわれる可能性があります。例えば、自動車のエンジンで使用される樹脂部品は、高温環境下で安定して機能する必要があります。耐熱性が不足していると、エンジンの性能低下や部品の劣化が起こり、安全性や信頼性に影響を及ぼす可能性があります。したがって、様々な産業分野において耐熱性の高い樹脂材料の需要が高まっています。連続使用温度を考慮した適切な材料選択や設計が重要であり、これによって製品の信頼性や耐久性を向上させることができます。結果として、耐熱性樹脂は産業界の未来において重要な役割を果たすことが期待されています。
まとめ
樹脂材料の連続使用温度は重要な要素です。これは樹脂材料の耐熱性能を示し、製品の適切な使用条件を決定する上で重要な指標です。樹脂材料の連続使用温度は、製品が長期間にわたって特定の温度で使用される際の性能を示しています。製品設計や材料選定において、この連続使用温度を把握することは重要です。設計や製造プロセスにおいて樹脂材料の耐熱性能を考慮することで、製品の信頼性や耐久性を向上させることが可能です。
耐薬品性を高める!ホモポリマーの特性と用途
耐薬品性を向上させるために欠かせない、ホモポリマーの特性と用途についてご紹介します。化学工業や医療分野など、さまざまな産業で重要な役割を果たすホモポリマー。その特性や利点を知ることで、耐薬品性を高めるための効果的な方法を探求できます。さらに、薬品耐性を強化することによって、製品の品質や耐久性を向上させることが可能です。本記事では、ホモポリマーに焦点を当て、その重要性や用途について詳しく解説していきます。耐薬品性を向上させるための鍵となる情報をお届けしますので、ぜひご一読ください。
ホモポリマーとは
ホモポリマーの基本概念
ホモポリマーは一種の高分子で、同じ単位構成体が重なって繰り返されてできています。この特性により、耐薬品性という大きな利点があります。耐薬品性とは、化学薬品や溶剤などの影響を受けにくい性質を指します。例えば、プラスチック製容器やパイプ、建材としての利用があります。これらの製品は日常生活や産業で幅広く利用されており、ホモポリマーの耐薬品性が重要視されているのです。さらに、医療機器や自動車部品など、厳しい環境下で使用される製品にも活用されています。ホモポリマーはその特性により、多岐にわたる用途で活躍しており、耐薬品性を高める重要な素材として注目を集めています。
ホモポリマーの種類と構造
ホモポリマーは、薬品に対する耐性を高めるために広く使用されています。ホモポリマーとは、同じ単量体からできた重合体のことです。この特性により、材料の物理的・化学的性質を調整し、耐薬品性を向上させることができます。
例えば、ホモポリプロピレンは、薬品に対する優れた耐性を持ち、パイプやタンクなどの産業用途で広く使用されています。また、ホモポリエチレンは、包装材料としても優れた耐薬品性を発揮し、食品や医薬品の保存に重要な役割を果たしています。
このように、ホモポリマーは多様な産業分野で耐薬品性を高めるために活用されています。その特性と用途から、物質の安定性や保護性を向上させる重要な役割を果たしています。
ホモポリマーの一般的な特性
ホモポリマーは、1種類のモノマーから作られる重要な高分子材料です。耐薬品性は、ホモポリマーの主な特性の一つです。耐薬品性が高いとは、化学薬品や溶剤などの外部からの影響に強いことを意味します。例えば、プラスチック容器やパイプなどに使用されるポリエチレンは、耐薬品性が高く、化学薬品の影響を受けにくい特性があります。これにより、化学工場や医薬品製造業界など、耐薬品性が要求されるさまざまな分野で重宝されています。ホモポリマーの耐薬品性が高まることで、産業界や生活の様々な面で利用される幅が広がり、安定性や効率性が向上すると期待されています。
ホモポリマーの薬品耐性
薬品耐性とは
ホモポリマーは、薬品に対する耐性を高める素材として注目されています。この特性について理解するために、まず薬品耐性の定義を考えてみましょう。薬品耐性とは、化学薬品や熱など外部の要因に対して、物質が変化せずにその性質を保つことを指します。
例えば、ホモポリマーは化学薬品に対して高い耐性を持つため、工業製品や医療機器などさまざまな分野で利用されています。ポリエチレンやポリプロピレンなどのホモポリマーは、その耐久性や耐薬品性から、食品包装や自動車部品などで広く使われています。
このように、ホモポリマーの薬品耐性は、さまざまな産業分野での利用価値が高いことがわかります。そのため、今後もホモポリマーの特性を活かしたさまざまな製品が開発され、産業界において重要な役割を果たすことが期待されています。
ホモポリマーの耐薬品性のメカニズム
ホモポリマーの耐薬品性は、その特性と用途において重要な要素です。ホモポリマーは、化学的に処理された薬品や環境条件に対して高い耐性を示すことができます。これは、ホモポリマー分子鎖が特定の薬品や条件に対して強固な結合を形成するためです。
例えば、工業用途では、ホモポリマーは酸やアルカリ、溶剤などの様々な薬品に対して優れた耐性を示します。これにより、機械部品や容器などの製品が長期間にわたって劣化せず、安定した性能を維持することが可能となります。
さらに、医療機器や食品包装などの分野でも、ホモポリマーの耐薬品性が重要な役割を果たしています。そのため、ホモポリマーは幅広い産業分野で利用され、その需要はますます高まっています。ホモポリマーの耐薬品性は、製品の品質や耐久性を向上させるために不可欠な特性であり、今後もさらなる進化が期待されています。
薬品に強いホモポリマーの例
ホモポリマーは、薬品に強い特性を持っています。この特性は、化学的な耐性を高めることに役立ち、さまざまな産業分野で幅広く活用されています。例えば、自動車部品や医療機器、建設材料など、耐久性が求められる製品に使われています。特に、自動車のエンジンルームでは、高温や化学物質に晒されるため、耐薬品性が重要な要素となります。
さらに、ホモポリマーは環境にも配慮した製品として注目されています。リサイクル可能な素材としても利用され、持続可能な製品開発に貢献しています。これにより、製品の寿命を延ばすだけでなく、環境への負荷を軽減する効果も期待されています。
このように、ホモポリマーは耐薬品性の高さと環境への配慮から、様々な産業分野で重要な役割を果たしています。
POM樹脂(ポリアセタール)の特性
POM樹脂の化学的性質
ホモポリマーは、単一の単位構造からなるポリマーであり、その特性は耐薬品性に優れています。この耐薬品性は、化学的性質に由来しており、例えば強い熱や化学薬品に対して安定した性質を示します。ホモポリマーは、工業製品や包装材料、医療機器などの幅広い用途に利用されています。
例えば、自動車部品においては、エンジン周りの高温・高圧環境に耐える必要があります。こうした厳しい条件下でも耐久性を保ちながら機能するため、POM樹脂が使用されています。また、化学薬品を取り扱う容器や配管などでも、その耐薬品性から信頼されています。
これらの特性から、ホモポリマーはさまざまな産業分野で重要な役割を果たしており、その需要は今後も拡大していくと期待されています。
POM樹脂の物理的性質
ホモポリマーは、その特性によって耐薬品性を高めることができます。例えば、POM樹脂は優れた物理的性質を持っています。この樹脂は耐熱性や耐摩耗性に優れており、化学薬品にも強い性質を持っています。これにより、自動車部品や工業製品など、様々な用途に活用されています。また、POMは潤滑性にも優れており、機械部品などの摩擦を減少させるのに適しています。そのため、POM樹脂は幅広い産業分野で重要な役割を果たしています。耐薬品性を重視する産業では、ホモポリマーの特性を活かした製品が求められており、日本国内でもその需要は着実に高まっています。
POM樹脂の耐薬品性
ホモポリマー(POM樹脂)は、耐薬品性が高い特性を持っています。この特性は、化学薬品や溶剤に対する優れた耐性を意味します。例えば、自動車部品や工業製品など、耐久性が求められる製品に広く利用されています。POM樹脂は、燃料や潤滑油などの化学的影響を受けにくく、長期間安定した性能を維持できるため、機械部品や歯車などの精密部品にも適しています。耐薬品性の高さから、POM樹脂は医療機器や食品加工機器などの分野でも重宝されています。これらの用途において、POM樹脂は安定性と信頼性を提供し、幅広い産業分野で重要な役割を果たしています。
POM樹脂の加工方法
POM樹脂の成形方法
ホモポリマーは耐薬品性に優れ、さまざまな用途で活躍しています。例えば、自動車の部品や医療機器、工業製品などに広く利用されています。その特性から、化学薬品や熱などの厳しい条件下でも安定した性能を発揮します。このような耐性が求められる環境では、ホモポリマーの使用が適しています。
さらに、ホモポリマーは成形しやすく、複雑な形状も実現できるため、製品の設計にも重宝されています。高い機械的強度や耐熱性を備え、信頼性の高い素材としても評価されています。これらの特性を活かし、さまざまな産業分野で幅広く利用されているのがホモポリマーなのです。
POM樹脂の加工上の注意点
ホモポリマーは、耐薬品性を高める素材として注目されています。その特性として、耐薬品性が非常に高いことが挙げられます。これは、化学的な薬品に対して安定して性能を維持できるため、さまざまな産業で幅広く利用されています。例えば、自動車部品や医療機器、工業製品などでホモポリマーが活用されています。
また、ホモポリマーは加工しやすいという特性も持っています。このため、製品の形状やサイズを自由に設計でき、さまざまな用途に適した製品を製造することが可能です。この柔軟性と耐久性から、ホモポリマーは多くの産業で重要な素材として活躍しています。そのため、耐薬品性を重視する製品開発や産業での需要が高まっています。
加工後のPOM樹脂の品質管理
ホモポリマーは、薬品に対する耐性を高める特性を持っています。例えば、工業製品や医療機器に使用されている部品など、耐久性が求められる分野で広く活用されています。このようなポリマーは、化学物質や薬品との接触に強いため、耐摩耗性や耐久性に優れています。さらに、ホモポリマーは環境にも配慮されており、リサイクル性にも優れています。
このような特性から、ホモポリマーは自動車部品や電子機器、産業機械など幅広い分野で利用されています。薬品や化学物質による劣化や変形が少ないため、長期間使用しても安定した性能を維持できます。そのため、製品の寿命を延ばしたり、製品の信頼性を高めるために重要な役割を果たしています。
POM樹脂の長所と短所
POM樹脂の利点
ホモポリマー(POM樹脂)は、耐薬品性が高い特性を持っています。この特性は、化学薬品や溶剤などの影響を受けにくく、耐久性が高いことを意味します。例えば、自動車部品や医療機器など、厳しい環境下で使用される製品に広く利用されています。POM樹脂は、機械加工性にも優れており、精密な部品を製造する際に重宝されています。このような利点から、製造業や産業界での需要が高まっています。さらに、熱にも強い性質を持ち、高温環境下でも安定した性能を発揮します。POM樹脂の特性を活かした製品は、幅広い分野で重要な役割を果たしており、その用途は今後も拡大が期待されています。
POM樹脂の制約と課題
ホモポリマーは、耐薬品性が高く、様々な用途で活躍しています。しかし、その特性には制約や課題も存在します。例えば、POM樹脂は耐熱性や機械的特性に優れていますが、紫外線に弱いという欠点があります。このため、屋外での使用には適していません。また、POM樹脂は摩擦で発生する熱により劣化しやすい性質があります。
これらの課題を克服するために、新たな耐候性を持つホモポリマーの研究や開発が進められています。例えば、化学結合の強化や添加剤の改良により、耐久性や耐候性を高める取り組みが行われています。このような技術革新により、ホモポリマーの性能向上が期待されています。耐薬品性を高めることで、さまざまな産業で幅広く活用される可能性があります。
POM樹脂の改良への取り組み
耐薬品性を高める!ホモポリマーの特性と用途
ホモポリマーは、様々な産業分野で広く使用されています。特に耐薬品性を高める特性が注目されています。この特性は、化学薬品や食品といった薬品に対する耐性を持つことを意味します。例えば、工業用パイプやタンク、医療機器などがあります。これらの製品は、薬品に接しても劣化しにくいため、安全性が高いと言えます。
ホモポリマーの耐薬品性を高めるためには、材料の配合や製造プロセスの工夫が必要です。最新技術を駆使して、耐薬品性をさらに向上させる研究が進んでいます。このような取り組みによって、さまざまな産業でホモポリマーが活躍する可能性が広がっています。
プラスチック材料の基礎知識
プラスチックの分類と特徴
ホモポリマーは、1種類のモノマーから作られるポリマーであり、その独特な特性からさまざまな用途で活躍しています。ホモポリマーは耐薬品性に優れており、化学薬品や燃料などの薬品に強い特性を持っています。例えば、ポリプロピレンは耐薬品性に優れており、化学工場や医療機器などの用途で広く使用されています。また、ポリエチレンは耐薬品性と柔軟性に優れており、パイプや容器など様々な分野で利用されています。ホモポリマーはその特性を活かして、さまざまな分野で重要な役割を果たしています。耐薬品性を高めることで、ホモポリマーはさらに幅広い用途に活用されることが期待されています。
プラスチックの選択基準
ホモポリマーは、耐薬品性が高い特性を持ち、さまざまな用途で活躍しています。例えば、化学工業では薬品や溶剤に耐性があり、耐久性が求められる部品や容器の製造に利用されています。また、自動車産業では、燃料やオイルといった薬品に対する抵抗力が必要な装置やパーツに利用されています。
耐薬品性が高いため、ホモポリマーは医療機器や食品包装などの分野でも重要な役割を果たしています。例えば、手術用具や医薬品の包装に使用されることがあります。食品包装では、保存性や衛生面での要求が厳しい製品にも広く活用されています。
このように、ホモポリマーはさまざまな産業分野で耐薬品性が求められる製品や部品に利用され、その特性を活かして幅広い用途で活躍しています。
プラスチックの環境への影響
ホモポリマーは、耐薬品性を高めるために重要な役割を果たしています。この特性により、化学薬品や溶剤などの影響を受けにくくなります。例えば、自動車や電子機器などの製造において、耐薬品性が求められる場面が多くあります。ホモポリマーはそのニーズに応える素材として広く使用されています。
ホモポリマーは、その耐薬品性だけでなく、耐熱性や耐摩耗性などの特性も持っています。これらの特性により、製品の耐久性や信頼性を向上させることができます。特に自動車部品や工業製品において、ホモポリマーは重要な役割を果たしています。
ホモポリマーの特性と用途を理解することで、製品の品質向上や環境への影響軽減につながることが期待されます。将来的には、より持続可能で効率的な製品開発に向けて、ホモポリマーの活用がますます重要になるでしょう。
クレハKFポリマーの特性
クレハKFポリマーの基本情報
ホモポリマーは、耐薬品性を高める素材として注目されています。例えば、建設業界では耐久性が求められるため、モノマーが同じポリマーで構成されるホモポリマーが広く利用されています。このようなホモポリマーは、化学薬品や熱などの要因に強い特性を持っており、長期間使用しても劣化しにくいという利点があります。さらに、自動車部品や医療機器などの分野でも、耐薬品性が要求されるため、ホモポリマーが活用されています。日本においても、製造業や医療産業などでホモポリマーの需要が高まっています。耐久性や安定性が求められる様々な分野において、ホモポリマーは重要な役割を果たしています。
クレハKFポリマーの耐薬品性
ホモポリマーは、化学的に単一のモノマーから構成される重要なポリマーです。これらのポリマーは、耐薬品性が高い特性を持っています。例えば、クレハKFポリマーは、酸やアルカリに対して非常に強い耐性を示します。これは、産業用途や医療機器など、さまざまな分野で広く使用されています。
ホモポリマーの耐薬品性は、環境への安全性や耐久性といった面でも重要な役割を果たしています。例えば、化学工場で使用される設備や自動車部品など、様々な分野でホモポリマーの利用が進んでいます。
このように、ホモポリマーは耐薬品性に優れる特性を持ち、さまざまな産業分野で重要な役割を果たしています。その耐性の高さから、安定した製品を提供する際に欠かせない素材として注目を集めています。
クレハKFポリマーの応用分野
ホモポリマーは、その耐薬品性からさまざまな分野で幅広く活用されています。例えば、自動車産業では、エンジンルーム内での化学薬品に対する耐性が求められるため、ホモポリマーが使用されています。また、家庭用品や医療機器などでも、耐薬品性が要求される場面でホモポリマーは重宝されています。
耐薬品性を備えることで、製品の耐久性や安全性が向上し、長期間にわたって使用することが可能となります。このように、ホモポリマーは高い機能性を持ちながらも安定性を保つ特性があります。
日本では、ホモポリマーの技術が進化し、産業界で広く活用されています。耐薬品性に優れたホモポリマーは、さまざまな製品の性能向上に貢献しており、今後もその重要性は高まることが期待されています。
ホモポリマーの用途と応用
POM樹脂の産業での使用例
耐薬品性を高める!ホモポリマーの特性と用途
ホモポリマーは化学的に安定しているため、耐薬品性が高いという特性を持っています。日本の自動車産業では、エンジンルーム内での様々な薬品にさらされる部品やコンポーネントにホモポリマーが広く使用されています。例えば、燃料タンクやエンジンカバー、オイルフィルターハウジングなどが挙げられます。
これらの部品にホモポリマーが使われる理由は、その耐薬品性にあります。燃料やオイルなどの化学薬品に対して安定性を維持し、劣化や変形を防ぐことができるため、安全性や耐久性が確保されます。
自動車産業以外でも、家電製品や医療機器など幅広い産業でホモポリマーが活用されています。その信頼性と高い性能から、さまざまな分野での需要が今後も期待されています。
耐薬品性を活かしたホモポリマーの特殊用途
ホモポリマーは耐薬品性を活かした特殊な用途で多くの注目を集めています。例えば、化学工業や医療機器産業では、薬品や化学物質に対する耐性が求められるため、ホモポリマーが重要な役割を果たしています。特に、強力な溶剤や薬品に晒される環境で使用されるパーソナルケア製品や医療機器において、ホモポリマーは優れた性能を発揮します。これにより、製品の信頼性や耐久性が向上し、安全性が確保されます。つまり、ホモポリマーは薬品耐性を活かしたさまざまな分野で重要な役割を果たし、その特性が広く評価されています。
ホモポリマーの将来性と発展可能性
ホモポリマーは、耐薬品性が高い特性を持ち、さまざまな用途に活用される素材です。日本では、自動車部品や医療機器、建築材料など幅広い産業で利用されています。
この素材の耐薬品性は、化学薬品や熱、摩耗などの外部要因に強いことを意味します。例えば、自動車部品に使用されるホモポリマーは、エンジンの高温環境や車体の衝撃に耐えるために重要です。また、医療機器においても、耐薬品性が要求されるため、安全性と耐久性を兼ね備えています。
将来性として、ホモポリマーの研究開発が進み、さらなる新たな用途が見込まれています。耐久性や軽量化が求められる産業分野において、ホモポリマーは重要な役割を果たすことが期待されています。このように、ホモポリマーは今後さらなる発展が期待される素材として注目されています。
ホモポリマーの選択と購入ガイド
ホモポリマー製品の選び方
ホモポリマー製品を選ぶ際に重要なポイントはいくつかあります。まず第一に、耐薬品性が高いかどうかを確認することが重要です。耐薬品性が高いホモポリマーは、化学薬品や溶剤などに対して耐久性があり、長期間使用しても劣化しにくい特性があります。例えば、工業用途や医療機器などの分野では、耐薬品性が求められることが多いです。
その他にも、ホモポリマーの用途に合った適切な特性を持つ製品を選ぶことも大切です。例えば、食品包装用途には食品衛生基準に適合した製品が必要となります。このように、ホモポリマー製品を選ぶ際には、耐薬品性だけでなく、用途に合った適切な特性を持つ製品を選ぶことが重要です。
耐薬品性ホモポリマーの市場とメーカー
ホモポリマーは、化学的に耐薬品性を持つポリマーであり、さまざまな産業分野で重要な役割を果たしています。この特性は、化学薬品や溶剤などの影響を受けにくく、耐久性に優れていることが特徴です。
例えば、自動車産業では、ホモポリマーが自動車部品の製造に広く使用されています。これは、耐薬品性が高く、燃料や潤滑油などの化学物質に対して強い耐性を持っているためです。
また、医療機器や包装材料、建築材料などでもホモポリマーが活用されており、その需要は着実に拡大しています。耐薬品性が求められる環境下での利用が増える中、ホモポリマー市場は成長を続けています。
このように、耐薬品性を持つホモポリマーは、さまざまな産業分野での用途が広がり、需要が高まる傾向にあります。そのため、製造メーカーや関連企業にとっても重要な市場となっています。
購入時の注意点とアフターサービス
ホモポリマーは化学物質で作られた材料で、耐薬品性を高める特性があります。例えば、ホモポリマー製品は化学薬品や薬品に対する耐性が高く、長期間使用しても劣化しにくいという利点があります。この特性から、化学工業や医療機器、自動車部品などのさまざまな分野で広く活用されています。
ホモポリマーは、耐薬品性が要求される環境や条件下で優れた性能を発揮するため、製品の耐久性や信頼性を向上させることができます。例えば、化学工場で使用される配管や容器、医療機器の部品などに用いられています。
そのため、ホモポリマーは日常生活から産業用途まで幅広い分野で重要な役割を果たしており、耐薬品性を求める製品やシステムの開発において欠かせない素材となっています。
まとめ
ホモポリマーには、耐薬品性を高める特性があります。これは、化学薬品に対する耐性を持つことを意味し、様々な用途に利用されます。ホモポリマーは、医療機器や工業製品など多くの分野で使用されており、その特性を活かして耐薬品性を高めることができます。これにより、製品の耐久性や安定性が向上し、さまざまな状況において優れた性能を発揮します。
耐薬品性を高める!ホモポリマーの特性と用途
耐薬品性を向上させるために欠かせない、ホモポリマーの特性と用途についてご紹介します。化学工業や医療分野など、さまざまな産業で重要な役割を果たすホモポリマー。その特性や利点を知ることで、耐薬品性を高めるための効果的な方法を探求できます。さらに、薬品耐性を強化することによって、製品の品質や耐久性を向上させることが可能です。本記事では、ホモポリマーに焦点を当て、その重要性や用途について詳しく解説していきます。耐薬品性を向上させるための鍵となる情報をお届けしますので、ぜひご一読ください。
ホモポリマーとは
ホモポリマーの基本概念
ホモポリマーは一種の高分子で、同じ単位構成体が重なって繰り返されてできています。この特性により、耐薬品性という大きな利点があります。耐薬品性とは、化学薬品や溶剤などの影響を受けにくい性質を指します。例えば、プラスチック製容器やパイプ、建材としての利用があります。これらの製品は日常生活や産業で幅広く利用されており、ホモポリマーの耐薬品性が重要視されているのです。さらに、医療機器や自動車部品など、厳しい環境下で使用される製品にも活用されています。ホモポリマーはその特性により、多岐にわたる用途で活躍しており、耐薬品性を高める重要な素材として注目を集めています。
ホモポリマーの種類と構造
ホモポリマーは、薬品に対する耐性を高めるために広く使用されています。ホモポリマーとは、同じ単量体からできた重合体のことです。この特性により、材料の物理的・化学的性質を調整し、耐薬品性を向上させることができます。
例えば、ホモポリプロピレンは、薬品に対する優れた耐性を持ち、パイプやタンクなどの産業用途で広く使用されています。また、ホモポリエチレンは、包装材料としても優れた耐薬品性を発揮し、食品や医薬品の保存に重要な役割を果たしています。
このように、ホモポリマーは多様な産業分野で耐薬品性を高めるために活用されています。その特性と用途から、物質の安定性や保護性を向上させる重要な役割を果たしています。
ホモポリマーの一般的な特性
ホモポリマーは、1種類のモノマーから作られる重要な高分子材料です。耐薬品性は、ホモポリマーの主な特性の一つです。耐薬品性が高いとは、化学薬品や溶剤などの外部からの影響に強いことを意味します。例えば、プラスチック容器やパイプなどに使用されるポリエチレンは、耐薬品性が高く、化学薬品の影響を受けにくい特性があります。これにより、化学工場や医薬品製造業界など、耐薬品性が要求されるさまざまな分野で重宝されています。ホモポリマーの耐薬品性が高まることで、産業界や生活の様々な面で利用される幅が広がり、安定性や効率性が向上すると期待されています。
ホモポリマーの薬品耐性
薬品耐性とは
ホモポリマーは、薬品に対する耐性を高める素材として注目されています。この特性について理解するために、まず薬品耐性の定義を考えてみましょう。薬品耐性とは、化学薬品や熱など外部の要因に対して、物質が変化せずにその性質を保つことを指します。
例えば、ホモポリマーは化学薬品に対して高い耐性を持つため、工業製品や医療機器などさまざまな分野で利用されています。ポリエチレンやポリプロピレンなどのホモポリマーは、その耐久性や耐薬品性から、食品包装や自動車部品などで広く使われています。
このように、ホモポリマーの薬品耐性は、さまざまな産業分野での利用価値が高いことがわかります。そのため、今後もホモポリマーの特性を活かしたさまざまな製品が開発され、産業界において重要な役割を果たすことが期待されています。
ホモポリマーの耐薬品性のメカニズム
ホモポリマーの耐薬品性は、その特性と用途において重要な要素です。ホモポリマーは、化学的に処理された薬品や環境条件に対して高い耐性を示すことができます。これは、ホモポリマー分子鎖が特定の薬品や条件に対して強固な結合を形成するためです。
例えば、工業用途では、ホモポリマーは酸やアルカリ、溶剤などの様々な薬品に対して優れた耐性を示します。これにより、機械部品や容器などの製品が長期間にわたって劣化せず、安定した性能を維持することが可能となります。
さらに、医療機器や食品包装などの分野でも、ホモポリマーの耐薬品性が重要な役割を果たしています。そのため、ホモポリマーは幅広い産業分野で利用され、その需要はますます高まっています。ホモポリマーの耐薬品性は、製品の品質や耐久性を向上させるために不可欠な特性であり、今後もさらなる進化が期待されています。
薬品に強いホモポリマーの例
ホモポリマーは、薬品に強い特性を持っています。この特性は、化学的な耐性を高めることに役立ち、さまざまな産業分野で幅広く活用されています。例えば、自動車部品や医療機器、建設材料など、耐久性が求められる製品に使われています。特に、自動車のエンジンルームでは、高温や化学物質に晒されるため、耐薬品性が重要な要素となります。
さらに、ホモポリマーは環境にも配慮した製品として注目されています。リサイクル可能な素材としても利用され、持続可能な製品開発に貢献しています。これにより、製品の寿命を延ばすだけでなく、環境への負荷を軽減する効果も期待されています。
このように、ホモポリマーは耐薬品性の高さと環境への配慮から、様々な産業分野で重要な役割を果たしています。
POM樹脂(ポリアセタール)の特性
POM樹脂の化学的性質
ホモポリマーは、単一の単位構造からなるポリマーであり、その特性は耐薬品性に優れています。この耐薬品性は、化学的性質に由来しており、例えば強い熱や化学薬品に対して安定した性質を示します。ホモポリマーは、工業製品や包装材料、医療機器などの幅広い用途に利用されています。
例えば、自動車部品においては、エンジン周りの高温・高圧環境に耐える必要があります。こうした厳しい条件下でも耐久性を保ちながら機能するため、POM樹脂が使用されています。また、化学薬品を取り扱う容器や配管などでも、その耐薬品性から信頼されています。
これらの特性から、ホモポリマーはさまざまな産業分野で重要な役割を果たしており、その需要は今後も拡大していくと期待されています。
POM樹脂の物理的性質
ホモポリマーは、その特性によって耐薬品性を高めることができます。例えば、POM樹脂は優れた物理的性質を持っています。この樹脂は耐熱性や耐摩耗性に優れており、化学薬品にも強い性質を持っています。これにより、自動車部品や工業製品など、様々な用途に活用されています。また、POMは潤滑性にも優れており、機械部品などの摩擦を減少させるのに適しています。そのため、POM樹脂は幅広い産業分野で重要な役割を果たしています。耐薬品性を重視する産業では、ホモポリマーの特性を活かした製品が求められており、日本国内でもその需要は着実に高まっています。
POM樹脂の耐薬品性
ホモポリマー(POM樹脂)は、耐薬品性が高い特性を持っています。この特性は、化学薬品や溶剤に対する優れた耐性を意味します。例えば、自動車部品や工業製品など、耐久性が求められる製品に広く利用されています。POM樹脂は、燃料や潤滑油などの化学的影響を受けにくく、長期間安定した性能を維持できるため、機械部品や歯車などの精密部品にも適しています。耐薬品性の高さから、POM樹脂は医療機器や食品加工機器などの分野でも重宝されています。これらの用途において、POM樹脂は安定性と信頼性を提供し、幅広い産業分野で重要な役割を果たしています。
POM樹脂の加工方法
POM樹脂の成形方法
ホモポリマーは耐薬品性に優れ、さまざまな用途で活躍しています。例えば、自動車の部品や医療機器、工業製品などに広く利用されています。その特性から、化学薬品や熱などの厳しい条件下でも安定した性能を発揮します。このような耐性が求められる環境では、ホモポリマーの使用が適しています。
さらに、ホモポリマーは成形しやすく、複雑な形状も実現できるため、製品の設計にも重宝されています。高い機械的強度や耐熱性を備え、信頼性の高い素材としても評価されています。これらの特性を活かし、さまざまな産業分野で幅広く利用されているのがホモポリマーなのです。
POM樹脂の加工上の注意点
ホモポリマーは、耐薬品性を高める素材として注目されています。その特性として、耐薬品性が非常に高いことが挙げられます。これは、化学的な薬品に対して安定して性能を維持できるため、さまざまな産業で幅広く利用されています。例えば、自動車部品や医療機器、工業製品などでホモポリマーが活用されています。
また、ホモポリマーは加工しやすいという特性も持っています。このため、製品の形状やサイズを自由に設計でき、さまざまな用途に適した製品を製造することが可能です。この柔軟性と耐久性から、ホモポリマーは多くの産業で重要な素材として活躍しています。そのため、耐薬品性を重視する製品開発や産業での需要が高まっています。
加工後のPOM樹脂の品質管理
ホモポリマーは、薬品に対する耐性を高める特性を持っています。例えば、工業製品や医療機器に使用されている部品など、耐久性が求められる分野で広く活用されています。このようなポリマーは、化学物質や薬品との接触に強いため、耐摩耗性や耐久性に優れています。さらに、ホモポリマーは環境にも配慮されており、リサイクル性にも優れています。
このような特性から、ホモポリマーは自動車部品や電子機器、産業機械など幅広い分野で利用されています。薬品や化学物質による劣化や変形が少ないため、長期間使用しても安定した性能を維持できます。そのため、製品の寿命を延ばしたり、製品の信頼性を高めるために重要な役割を果たしています。
POM樹脂の長所と短所
POM樹脂の利点
ホモポリマー(POM樹脂)は、耐薬品性が高い特性を持っています。この特性は、化学薬品や溶剤などの影響を受けにくく、耐久性が高いことを意味します。例えば、自動車部品や医療機器など、厳しい環境下で使用される製品に広く利用されています。POM樹脂は、機械加工性にも優れており、精密な部品を製造する際に重宝されています。このような利点から、製造業や産業界での需要が高まっています。さらに、熱にも強い性質を持ち、高温環境下でも安定した性能を発揮します。POM樹脂の特性を活かした製品は、幅広い分野で重要な役割を果たしており、その用途は今後も拡大が期待されています。
POM樹脂の制約と課題
ホモポリマーは、耐薬品性が高く、様々な用途で活躍しています。しかし、その特性には制約や課題も存在します。例えば、POM樹脂は耐熱性や機械的特性に優れていますが、紫外線に弱いという欠点があります。このため、屋外での使用には適していません。また、POM樹脂は摩擦で発生する熱により劣化しやすい性質があります。
これらの課題を克服するために、新たな耐候性を持つホモポリマーの研究や開発が進められています。例えば、化学結合の強化や添加剤の改良により、耐久性や耐候性を高める取り組みが行われています。このような技術革新により、ホモポリマーの性能向上が期待されています。耐薬品性を高めることで、さまざまな産業で幅広く活用される可能性があります。
POM樹脂の改良への取り組み
耐薬品性を高める!ホモポリマーの特性と用途
ホモポリマーは、様々な産業分野で広く使用されています。特に耐薬品性を高める特性が注目されています。この特性は、化学薬品や食品といった薬品に対する耐性を持つことを意味します。例えば、工業用パイプやタンク、医療機器などがあります。これらの製品は、薬品に接しても劣化しにくいため、安全性が高いと言えます。
ホモポリマーの耐薬品性を高めるためには、材料の配合や製造プロセスの工夫が必要です。最新技術を駆使して、耐薬品性をさらに向上させる研究が進んでいます。このような取り組みによって、さまざまな産業でホモポリマーが活躍する可能性が広がっています。
プラスチック材料の基礎知識
プラスチックの分類と特徴
ホモポリマーは、1種類のモノマーから作られるポリマーであり、その独特な特性からさまざまな用途で活躍しています。ホモポリマーは耐薬品性に優れており、化学薬品や燃料などの薬品に強い特性を持っています。例えば、ポリプロピレンは耐薬品性に優れており、化学工場や医療機器などの用途で広く使用されています。また、ポリエチレンは耐薬品性と柔軟性に優れており、パイプや容器など様々な分野で利用されています。ホモポリマーはその特性を活かして、さまざまな分野で重要な役割を果たしています。耐薬品性を高めることで、ホモポリマーはさらに幅広い用途に活用されることが期待されています。
プラスチックの選択基準
ホモポリマーは、耐薬品性が高い特性を持ち、さまざまな用途で活躍しています。例えば、化学工業では薬品や溶剤に耐性があり、耐久性が求められる部品や容器の製造に利用されています。また、自動車産業では、燃料やオイルといった薬品に対する抵抗力が必要な装置やパーツに利用されています。
耐薬品性が高いため、ホモポリマーは医療機器や食品包装などの分野でも重要な役割を果たしています。例えば、手術用具や医薬品の包装に使用されることがあります。食品包装では、保存性や衛生面での要求が厳しい製品にも広く活用されています。
このように、ホモポリマーはさまざまな産業分野で耐薬品性が求められる製品や部品に利用され、その特性を活かして幅広い用途で活躍しています。
プラスチックの環境への影響
ホモポリマーは、耐薬品性を高めるために重要な役割を果たしています。この特性により、化学薬品や溶剤などの影響を受けにくくなります。例えば、自動車や電子機器などの製造において、耐薬品性が求められる場面が多くあります。ホモポリマーはそのニーズに応える素材として広く使用されています。
ホモポリマーは、その耐薬品性だけでなく、耐熱性や耐摩耗性などの特性も持っています。これらの特性により、製品の耐久性や信頼性を向上させることができます。特に自動車部品や工業製品において、ホモポリマーは重要な役割を果たしています。
ホモポリマーの特性と用途を理解することで、製品の品質向上や環境への影響軽減につながることが期待されます。将来的には、より持続可能で効率的な製品開発に向けて、ホモポリマーの活用がますます重要になるでしょう。
クレハKFポリマーの特性
クレハKFポリマーの基本情報
ホモポリマーは、耐薬品性を高める素材として注目されています。例えば、建設業界では耐久性が求められるため、モノマーが同じポリマーで構成されるホモポリマーが広く利用されています。このようなホモポリマーは、化学薬品や熱などの要因に強い特性を持っており、長期間使用しても劣化しにくいという利点があります。さらに、自動車部品や医療機器などの分野でも、耐薬品性が要求されるため、ホモポリマーが活用されています。日本においても、製造業や医療産業などでホモポリマーの需要が高まっています。耐久性や安定性が求められる様々な分野において、ホモポリマーは重要な役割を果たしています。
クレハKFポリマーの耐薬品性
ホモポリマーは、化学的に単一のモノマーから構成される重要なポリマーです。これらのポリマーは、耐薬品性が高い特性を持っています。例えば、クレハKFポリマーは、酸やアルカリに対して非常に強い耐性を示します。これは、産業用途や医療機器など、さまざまな分野で広く使用されています。
ホモポリマーの耐薬品性は、環境への安全性や耐久性といった面でも重要な役割を果たしています。例えば、化学工場で使用される設備や自動車部品など、様々な分野でホモポリマーの利用が進んでいます。
このように、ホモポリマーは耐薬品性に優れる特性を持ち、さまざまな産業分野で重要な役割を果たしています。その耐性の高さから、安定した製品を提供する際に欠かせない素材として注目を集めています。
クレハKFポリマーの応用分野
ホモポリマーは、その耐薬品性からさまざまな分野で幅広く活用されています。例えば、自動車産業では、エンジンルーム内での化学薬品に対する耐性が求められるため、ホモポリマーが使用されています。また、家庭用品や医療機器などでも、耐薬品性が要求される場面でホモポリマーは重宝されています。
耐薬品性を備えることで、製品の耐久性や安全性が向上し、長期間にわたって使用することが可能となります。このように、ホモポリマーは高い機能性を持ちながらも安定性を保つ特性があります。
日本では、ホモポリマーの技術が進化し、産業界で広く活用されています。耐薬品性に優れたホモポリマーは、さまざまな製品の性能向上に貢献しており、今後もその重要性は高まることが期待されています。
ホモポリマーの用途と応用
POM樹脂の産業での使用例
耐薬品性を高める!ホモポリマーの特性と用途
ホモポリマーは化学的に安定しているため、耐薬品性が高いという特性を持っています。日本の自動車産業では、エンジンルーム内での様々な薬品にさらされる部品やコンポーネントにホモポリマーが広く使用されています。例えば、燃料タンクやエンジンカバー、オイルフィルターハウジングなどが挙げられます。
これらの部品にホモポリマーが使われる理由は、その耐薬品性にあります。燃料やオイルなどの化学薬品に対して安定性を維持し、劣化や変形を防ぐことができるため、安全性や耐久性が確保されます。
自動車産業以外でも、家電製品や医療機器など幅広い産業でホモポリマーが活用されています。その信頼性と高い性能から、さまざまな分野での需要が今後も期待されています。
耐薬品性を活かしたホモポリマーの特殊用途
ホモポリマーは耐薬品性を活かした特殊な用途で多くの注目を集めています。例えば、化学工業や医療機器産業では、薬品や化学物質に対する耐性が求められるため、ホモポリマーが重要な役割を果たしています。特に、強力な溶剤や薬品に晒される環境で使用されるパーソナルケア製品や医療機器において、ホモポリマーは優れた性能を発揮します。これにより、製品の信頼性や耐久性が向上し、安全性が確保されます。つまり、ホモポリマーは薬品耐性を活かしたさまざまな分野で重要な役割を果たし、その特性が広く評価されています。
ホモポリマーの将来性と発展可能性
ホモポリマーは、耐薬品性が高い特性を持ち、さまざまな用途に活用される素材です。日本では、自動車部品や医療機器、建築材料など幅広い産業で利用されています。
この素材の耐薬品性は、化学薬品や熱、摩耗などの外部要因に強いことを意味します。例えば、自動車部品に使用されるホモポリマーは、エンジンの高温環境や車体の衝撃に耐えるために重要です。また、医療機器においても、耐薬品性が要求されるため、安全性と耐久性を兼ね備えています。
将来性として、ホモポリマーの研究開発が進み、さらなる新たな用途が見込まれています。耐久性や軽量化が求められる産業分野において、ホモポリマーは重要な役割を果たすことが期待されています。このように、ホモポリマーは今後さらなる発展が期待される素材として注目されています。
ホモポリマーの選択と購入ガイド
ホモポリマー製品の選び方
ホモポリマー製品を選ぶ際に重要なポイントはいくつかあります。まず第一に、耐薬品性が高いかどうかを確認することが重要です。耐薬品性が高いホモポリマーは、化学薬品や溶剤などに対して耐久性があり、長期間使用しても劣化しにくい特性があります。例えば、工業用途や医療機器などの分野では、耐薬品性が求められることが多いです。
その他にも、ホモポリマーの用途に合った適切な特性を持つ製品を選ぶことも大切です。例えば、食品包装用途には食品衛生基準に適合した製品が必要となります。このように、ホモポリマー製品を選ぶ際には、耐薬品性だけでなく、用途に合った適切な特性を持つ製品を選ぶことが重要です。
耐薬品性ホモポリマーの市場とメーカー
ホモポリマーは、化学的に耐薬品性を持つポリマーであり、さまざまな産業分野で重要な役割を果たしています。この特性は、化学薬品や溶剤などの影響を受けにくく、耐久性に優れていることが特徴です。
例えば、自動車産業では、ホモポリマーが自動車部品の製造に広く使用されています。これは、耐薬品性が高く、燃料や潤滑油などの化学物質に対して強い耐性を持っているためです。
また、医療機器や包装材料、建築材料などでもホモポリマーが活用されており、その需要は着実に拡大しています。耐薬品性が求められる環境下での利用が増える中、ホモポリマー市場は成長を続けています。
このように、耐薬品性を持つホモポリマーは、さまざまな産業分野での用途が広がり、需要が高まる傾向にあります。そのため、製造メーカーや関連企業にとっても重要な市場となっています。
購入時の注意点とアフターサービス
ホモポリマーは化学物質で作られた材料で、耐薬品性を高める特性があります。例えば、ホモポリマー製品は化学薬品や薬品に対する耐性が高く、長期間使用しても劣化しにくいという利点があります。この特性から、化学工業や医療機器、自動車部品などのさまざまな分野で広く活用されています。
ホモポリマーは、耐薬品性が要求される環境や条件下で優れた性能を発揮するため、製品の耐久性や信頼性を向上させることができます。例えば、化学工場で使用される配管や容器、医療機器の部品などに用いられています。
そのため、ホモポリマーは日常生活から産業用途まで幅広い分野で重要な役割を果たしており、耐薬品性を求める製品やシステムの開発において欠かせない素材となっています。
まとめ
ホモポリマーには、耐薬品性を高める特性があります。これは、化学薬品に対する耐性を持つことを意味し、様々な用途に利用されます。ホモポリマーは、医療機器や工業製品など多くの分野で使用されており、その特性を活かして耐薬品性を高めることができます。これにより、製品の耐久性や安定性が向上し、さまざまな状況において優れた性能を発揮します。
コポリマーの薬品耐性向上ガイド
コポリマーは、様々な分野で使用される重要な材料です。その中でも、薬品耐性を向上させることは、特に化学工業や医療分野において重要な課題です。
コポリマーの薬品耐性向上ガイドでは、コポリマーの基本的な特性から、薬品に対する耐性を向上させる方法まで、幅広い情報をご紹介します。コポリマーを使用する際に気をつけるべきポイントや、効果的な加工方法についても詳しく解説していきます。
化学物質や薬品との相性は、製品の性能や耐久性に直結する重要な要素です。このガイドを通じて、コポリマーの薬品耐性を向上させるための方法やノウハウを身につけて、製品開発や研究に活かしてみませんか?設計や製造の現場で役立つ情報が満載です。
コポリマーの基本と薬品耐性の概要
コポリマーとは
コポリマーとは、2つ以上の異なる単量体から構成される重合体のことを指します。これらの異なる単量体は、それぞれの特性を組み合わせて、新しい性質を持った材料として利用されます。例えば、ポリスチレンとポリエチレンからなるコポリマーは、ポリスチレンの剛性とポリエチレンの柔軟性を兼ね備えた特性を持っています。
コポリマーは、薬品に対する耐性を向上させるためにも利用されます。特定の薬品に対して耐性を持つポリマーが必要な場合、コポリマーの開発が重要になります。例えば、化学工業で使用されるコポリマーは、耐性向上が求められることが多いです。
つまり、コポリマーは異なる性質を持つ単量体を組み合わせ、新しい特性を生み出す重要な材料として幅広い分野で活用されています。そのため、今後もコポリマーの研究や開発は重要性を増していくことが予想されます。
コポリマーの種類と特性
コポリマーは、薬品に対する耐性を向上させる素材として注目されています。コポリマーは異なる種類の単量体からできており、その組み合わせによって様々な特性が得られます。例えば、エチレンとプロピレンの組み合わせは、柔らかさと弾力性を持つコポリマーを作り出します。これにより、様々な用途に適した製品を開発することが可能となります。
さらに、コポリマーは化学的に安定しており、耐薬品性に優れています。これは、化学薬品や溶剤などの影響を受けにくいということを意味します。そのため、コポリマーは工業製品や医療機器など、薬品と接する製品の製造に最適です。
コポリマーの特性を活かして、さまざまな製品や産業に応用されており、その需要は今後もさらに拡大することが期待されています。
薬品耐性とは
コポリマーの薬品耐性向上ガイド
薬品耐性とは、コポリマーが化学薬品や溶剤など外部の物質に対してどれだけ耐性を持つかを示す性質です。例えば、工業製品や医療機器において化学薬品にさらされる可能性が高い場合、コポリマーの薬品耐性は重要な要素となります。特に、石油化学産業や自動車産業などの分野では、コポリマーの薬品耐性向上が製品の品質と耐久性の向上につながります。
コポリマーの薬品耐性を向上させるためには、適切な添加剤や工程を選択することが重要です。例えば、ポリエチレンとエチレン-プロピレンゴムのようなコポリマーは、適切な加工条件や添加剤を用いることで化学薬品に対する耐性を向上させることができます。
薬品耐性の向上は製品の性能向上につながり、安定した製品供給にも貢献します。コポリマーの薬品耐性を理解し、適切に管理することで、さまざまな産業分野における製品の品質向上につながることが期待されます。
化学薬品に対する素材の耐性の重要性
化学薬品に対する素材の耐性は、重要です。例えば、コポリマーは化学薬品に耐性があるため、工業製品や医療機器など多くの分野で利用されています。薬品に強い素材は、製品の寿命を延ばすだけでなく、安全性や信頼性も向上させます。
コポリマーの一つであるポリウレタンは、薬品に耐性があり、耐摩耗性や耐油性に優れています。例えば、化学工場で使用される配管やタンク、自動車の部品などに利用されています。このように、耐性のある素材は様々な状況で重要な役割を果たしています。
したがって、素材の耐性を考える際には、安全面や製品の性能向上だけでなく、製品の長寿命化や効率化も重要な要素となります。素材の選択は製品の品質や信頼性に直結するため、耐性を持つ素材の活用は産業界にとって欠かせません。
Proteus®コポリマーPPの特徴
Proteus®コポリマーPPの化学薬品耐性
コポリマーPPの薬品耐性を向上させるためには、Proteus®コポリマーを使用することが効果的です。この特殊なコポリマーは、化学薬品に対して優れた耐性を持ち、さまざまな産業分野で幅広く活用されています。
Proteus®コポリマーは、その特性から工業用途や医療機器、自動車部品などの製造に適しています。例えば、化学物質にさらされる環境下で安定した性能を発揮し、耐久性を保つことができます。これにより、製品の品質向上や製造プロセスの効率化が実現されるのです。
化学薬品に適したProteus®コポリマーを使用することで、製品の寿命が延び、メンテナンスコストが削減されることが期待されます。産業界において、安定した品質と効率的な生産プロセスを実現するために、コポリマーの選択は重要な要素となります。
Proteus®コポリマーPPの応力耐性
[コポリマーの薬品耐性向上ガイド]
コポリマーは、様々な分野で幅広く活用されていますが、特に薬品耐性の向上が求められています。例えば、化学工場や医薬品製造工場など、薬品にさらされる環境では耐性が重要となります。
その理由は、薬品によってはプラスチック製品を腐食させる可能性があり、結果として機能性や安全性の低下が懸念されます。コポリマーはこのような状況において、耐性を高める特性を持っており、長期間安定した性能を提供します。
例えば、化学物質による腐食から保護するパイプラインやタンク、医療機器、食品包装などにコポリマーが活用されています。そのため、薬品耐性向上ガイドは、安全性や耐久性を重視する産業にとって貴重な情報源となるでしょう。
Proteus®コポリマーPPの応用事例
コポリマーの薬品耐性は重要です。薬品に対する耐性を向上させる方法を考えてみましょう。例えば、Proteus®コポリマーPPは優れた薬品耐性を持ち、化学物質に対して安定性が高いことが知られています。
薬品に対する耐性を向上させるためには、適切な製造プロセスや添加剤の使用が重要です。Proteus®コポリマーPPを使用することで、化学薬品に対する耐性が向上し、製品の耐久性が高まります。
特に工業用途でのコポリマーの需要が高まっており、Proteus®コポリマーPPはさまざまな産業分野で幅広く活用されています。薬品耐性が求められる環境下での応用事例も増えています。
コポリマーの薬品耐性向上は、製品の品質向上や安全性確保に貢献します。Proteus®コポリマーPPを活用することで、薬品に対する優れた耐性を実現し、さまざまな産業分野でのニーズに応えることができます。
コポリマーの耐薬品性向上の方法
耐薬品性を高めるコポリマーの設計
コ ポ リ マ ーは様々な産業で広く使用されていますが、薬品に対する耐性を高めることは重要です。例えば、化学工場で使用される配管システムや薬品容器など、薬品が接触する環境では耐薬品性が求められます。このような環境でコポリマーが劣化すると、重大な事故や損害を引き起こす可能性があります。
耐薬品性を高めるためには、コポリマーの設計段階から注意が必要です。特定の薬品に対する耐性を向上させるために、分子構造や添加物の使用を工夫する必要があります。例えば、ポリエチレンなどのコポリマーは、強化された耐薬品性を持ち、化学薬品に対する安定性が高いことが知られています。
このような設計改良によって、コポリマー製品の寿命が延び、安全性が向上します。薬品による劣化や変形を抑制することで、産業界での利用価値が高まります。耐薬品性を向上させるコポリマーの設計は、安全性と信頼性を確保する上で重要な要素となります。
耐久性を向上させるコポリマーの加工技術
コポリマーの耐久性を向上させるためには、適切な加工技術が欠かせません。例えば、熱可塑性ポリマーをブレンドすることで、化学薬品に対する耐性を高めることができます。このようなコポリマーは、薬品による劣化や変形を抑制し、製品の寿命を延ばすことができます。
さらに、特定の添加剤を使用することで、コポリマーの耐熱性や耐薬品性を向上させることが可能です。例えば、ポリエーテルスルホンは耐熱性に優れ、強酸や強塩基にも強い耐性を持ちます。これにより、化学工業や医療機器など、厳しい環境下で使用される製品においてコポリマーが重要な役割を果たしています。
このように、適切な加工技術と添加剤の選定によってコポリマーの耐久性を向上させることができます。企業や研究機関がこの分野に注力し、製品の品質向上や新たな産業分野の開拓に貢献することが期待されています。
耐薬品性を評価する方法
コポリマーの薬品耐性向上ガイド
コポリマーの薬品耐性を評価する方法は、重要な機能です。薬品に対する耐性が向上することで、製品の耐久性や安全性が向上します。例えば、自動車部品や医療機器など、さまざまな産業でコポリマーが使用されています。薬品に耐性のあるコポリマーは、環境においても優れたパフォーマンスを発揮します。
耐薬品性を評価する方法には、実験や試験が含まれます。特定の薬品に対してコポリマーの性能をテストし、その結果に基づいて改良を行うことが重要です。このような努力によって、製品の品質が向上し、市場競争力が高まります。薬品耐性向上は産業界において欠かせない要素であり、継続的な研究開発が求められています。
耐薬品性に優れた材料の特徴
材料選択の基準と考慮点
コポリマーの薬品耐性向上ガイド
コポリマーの耐性を向上させるためには、材料選択の基準と考慮点が重要です。例えば、コポリマーは特定の薬品に対して耐性が必要な場面で使用されます。そのため、材料の選択は重要な役割を果たします。耐性向上のための具体的な例として、特定の薬品に対して試験を行い、最適な材料を選定することが挙げられます。また、製品の使用環境や条件に合わせて材料を選択することも重要です。最終的には、材料の選択を通じてコポリマーの薬品耐性を向上させることが大切です。これにより、品質や耐久性が向上し、製品の性能が向上することが期待されます。
耐薬品性に優れたコポリマーの利点
コポリマーは、薬品に対する耐性が優れているため、様々な利点があります。まず、工業製品や医療機器など、薬品に接する環境下で使用される場面で優れた性能を発揮します。例えば、化学薬品や溶剤が直接触れる箇所に使用されると、コポリマーは高い耐久性を示し、劣化しにくい特性があります。さらに、薬品の浸食や変形に対しても強い耐性を持ち、安定性が保たれることが多いです。
このように、コポリマーの耐薬品性は、産業界や医療分野などで幅広く活用されています。それにより、製品の寿命を延ばしたり、安全性を高めたりすることが可能となります。耐薬品性に優れたコポリマーは、現代社会において欠かせない重要な素材として注目されています。
業界ごとの耐薬品性の要求基準
コポリマーの薬品耐性向上ガイド
コポリマーの産業において、様々な材料が様々な環境や条件において使用されます。それぞれの業界において、材料が薬品に対してどの程度の耐性を持つことが求められています。例えば、自動車産業では燃料やオイルといった薬品に対する耐性が重要です。また、建築業界では風雨や酸性雨などの外部要因からの保護が求められます。
それぞれの業界において、コポリマーは異なる耐薬品性基準を満たす必要があります。例えば、自動車部品で使用されるコポリマーは、耐油性が高くなければなりません。一方、建築材料で使用されるコポリマーは、耐候性や耐薬品性が重要となります。
業界ごとの要求基準を満たすことが、コポリマーの薬品耐性向上の鍵となります。
ポリカーボネート樹脂の特性と用途
ポリカーボネート樹脂の基本特性
コポリマーの薬品耐性向上ガイド
コポリマーは、様々な分野で幅広く使われる素材です。その中でも、薬品耐性を向上させることは重要なテーマです。薬品に対する耐性が向上することで、製品の耐久性や安全性が向上し、さらなる用途拡大が期待されます。
コポリマーの薬品耐性を向上させるためには、材料の選定や製造工程の改善などが必要です。例えば、特定の薬品に対する耐性を高める添加剤の使用や、特殊なコーティング技術の導入などが考えられます。
これらの取り組みにより、コポリマー製品はさらなる進化を遂げることが期待されます。薬品耐性の向上は、製品の品質向上や新たな産業分野への展開につながる重要な要素となります。
ポリカーボネートの薬品耐性
コポリマーの薬品耐性向上ガイド
コポリマーは、化学物質に対する耐性を向上させるための重要な指標です。例えば、ポリカーボネートは、化学物質に対して非常に耐久性があります。これは、化学薬品による腐食や劣化から製品を保護する重要な要素です。
コポリマーの薬品耐性を向上させるには、材料の選択が重要です。例えば、特定の添加剤を使用することで、ポリマーの特性を調整し、化学薬品に対する耐久性を向上させることができます。
さらに、実際の使用状況に合わせてコポリマーを設計することも重要です。例えば、工業用途で使用されるコポリマーは、特定の薬品に対する耐性を向上させるために特別に設計されています。
コポリマーの薬品耐性を向上させることは、製品の耐久性や安全性を確保するために不可欠です。そのため、材料の選択や設計段階での検討が重要です。
ポリカーボネート樹脂の応用分野
コポリマーの薬品耐性向上ガイド
薬品耐性を向上させるためには、コポリマーの特性を理解することが重要です。コポリマーは、複数の異なる単量体から構成される重要な材料です。例えば、ポリカーボネートは熱可塑性のコポリマーで、高い透明性と耐衝撃性を持っています。そして、このような特性が化学薬品に対する耐性を向上させるのに役立ちます。
さらに具体的な例を挙げると、自動車部品や医療機器の製造において、コポリマーは広く活用されています。例えば、医療機器の外部カバーには、化学薬品への耐性が求められるため、ポリプロピレンコポリマーが使用されます。
このように、コポリマーの薬品耐性は様々な産業分野で重要な役割を果たしており、応用分野の拡大が期待されています。化学薬品に対する耐性向上は、安全性や耐久性を高めるだけでなく、製品の品質向上にもつながる重要な要素となります。
ポリエステルコポリマーの加工と特性
ポリエステルコポリマーの加工方法
コ ポ リ マ ーの薬品耐性向上ガイド
薬品に対する耐性を向上させるためには、コ ポ リ マーの適切な加工方法が重要です。例えば、適切なポリエステルコポリマーを使用することで、化学薬品に対する耐性を高めることができます。このようなコ ポ リ マーは、工業製品や医療機器などの分野で広く使用されています。
特定の薬品に対する耐性を向上させるためには、材料の選択や製造プロセスの最適化が欠かせません。例えば、耐薬品性の高いコ ポ リ マーを選択し、加工時に適切な温度や圧力をかけることで耐性を高めることができます。
このように、コ ポ リ マーの薬品耐性を向上させるためには、適切な材料と加工方法を選択することが重要です。これにより、製品の耐久性や安全性を確保することができます。
加工における注意点と技術
コポリマーは、様々な場面で利用される重要な素材です。このコポリマーの薬品耐性を向上させるためには、いくつかの注意点と技術があります。
まず、使用する薬品に応じて適切なコポリマーを選択することが重要です。例えば、特定の化学物質に対して耐性のあるコポリマーを選ぶことで、製品の耐久性を向上させることができます。
さらに、製造過程での加工方法にも注意が必要です。適切な温度や圧力を設定することで、コポリマーの薬品耐性を高めることができます。
これらの注意点と技術を遵守することで、コポリマーの薬品耐性を向上させることができ、安定した製品を提供することができます。
ポリエステルコポリマーの特性と優れた用途
コポリマーの薬品耐性向上ガイド
コポリマーは、薬品に対する耐性を高めることができる重要な要素です。例えば、ポリエステルコポリマーは、化学薬品や溶剤に耐性があり、さまざまな用途に優れています。この特性を活かして、化粧品や医療機器、自動車部品など幅広い分野で活用されています。
コポリマーの中でも、ポリエステルコポリマーは熱にも強く、耐久性に優れています。例えば、自動車部品に使用すると、耐油性や耐薬品性に優れた性能を発揮します。さらに、建築材料や工業製品にも広く利用されており、その信頼性と効果が高く評価されています。
このように、コポリマーはさまざまな産業で重要な役割を果たしています。薬品耐性を向上させることで、製品の耐久性や性能を向上させることができるため、今後もさらなる進化が期待されています。
まとめ
コポリマーの薬品耐性向上ガイド
コポリマーの薬品耐性を向上させるためには、適切な添加剤や製造方法を選択することが重要です。特定の薬品に対する耐性を向上させるためには、コポリマーに特定の添加剤を組み合わせることが有効です。また、製造工程での温度や圧力の調整も耐性向上に大きく影響します。
コポリマーの薬品耐性を向上させるためには、素材の選定から製造工程までを慎重に検討し、適切な対策を講じることが不可欠です。それにより、コポリマーの性能を最大限に引き出し、薬品に対する耐性を向上させることが可能となります。
化学業界必見!コポリマーを使った耐薬品性向上の秘訣
化学業界における革新的な技術や素材は、産業の発展に欠かせません。本記事では、化学業界における重要な要素であるコポリマーを使用した耐薬品性向上の秘訣について探求します。コポリマーは、その独自の性質によってさまざまな産業で幅広く活用されており、特に薬品耐性向上においてその効果を発揮しています。
この記事では、コポリマーの特性や利点、薬品耐性向上の仕組みについて詳しく解説します。化学業界に携わる方々や素材開発に興味をお持ちの方々にとって、今後の技術革新や製品開発において参考になる情報を提供します。
化学業界の未来を担うために、コポリマーを使った耐薬品性向上の秘訣を知ることは不可欠です。ぜひともこの記事を通じて、新たな知識と洞察を得て、業界の発展に貢献していただければ幸いです。
コポリマーの基礎知識
コポリマーとは:定義と基本構造
コポリマーとは、2つ以上の異なる単量体(分子の構成単位)から構成される高分子化合物です。これらの単量体は、それぞれ特定の性質や機能を持ち、それらが結合してできるコポリマーは、新しい特性や応用価値を持つことが特徴です。例えば、耐薬品性向上の秘訣として、コポリマーは優れた耐薬品性を発揮することができます。
化学業界では、コポリマーの使用が注目されており、様々な製品や産業でその優れた特性が活かされています。例えば、自動車部品や医療機器の耐久性向上、建築材料の強度向上など、幅広い分野でコポリマーが活躍しています。このように、コポリマーは耐薬品性を向上させるための重要な材料として、化学業界で欠かせない存在となっています。
コポリマーの種類とそれぞれの特性
化学業界必見!コポリマーを使った耐薬品性向上の秘訣
コポリマーは、複数の異なる単量体からなる重要なポリマーです。これらは、薬品や化学薬品などの様々な環境に耐えるための特性を備えています。例えば、ポリプロピレンとエチレンからなるコポリマーは、耐薬品性に優れています。化学業界では、特定の薬品に対する耐性が必要な場面が多くあり、コポリマーはその要求を満たすために重要な役割を果たしています。
他にも、ポリエチレンとプロピレンからなるコポリマーは、包装材料として広く使用されています。これらのコポリマーは、耐薬品性や物理的な強度を両立させることができるため、包装業界でも重宝されています。化学業界において、コポリマーの種類とそれぞれの特性を理解することが、製品の品質向上や効率化につながる重要な要素となります。
コポリマーの一般的な用途
コポリマーは、様々な産業で幅広く活用されています。例えば、自動車産業では、コポリマーが耐薬品性を向上させるために使用されています。エンジン部品や内装部品など、様々な箇所で薬品に対する耐性が求められます。コポリマーの特性を活かすことで、耐薬品性が向上し、製品の耐久性や品質向上につながります。その他、建築材料や医療機器などでもコポリマーは重要な役割を果たしています。耐薬品性を必要とする場面で、コポリマーは優れた素材として選ばれています。これからも、コポリマーのさまざまな用途が広がり、産業界での重要性がますます高まることが期待されます。
耐薬品性プラスチックの選び方
耐薬品性プラスチックの基準と評価方法
コポリマーは、化学業界で注目されている素材です。なぜなら、コポリマーを使用することで、耐薬品性を向上させることができるからです。耐薬品性が高いプラスチックは、化学物質や薬品に対して効果的に耐性を持ち、安定性が保たれます。
このような特性を持つプラスチックが重要視されるのは、例えば工業用途や医療機器、自動車部品などの分野で、耐久性や安全性が求められるからです。コポリマーを使用することで、これらの製品の品質や信頼性を向上させることができます。
化学業界では、耐薬品性プラスチックの基準や評価方法が重要です。コポリマーを使用した製品の評価には、厳格な基準が定められており、その品質を保証するための取り組みが行われています。このような取り組みにより、安全で信頼性の高い製品が市場に供給されることが期待されます。
コポリマーを含む耐薬品性プラスチックの選択ガイド
コポリマーを含む耐薬品性プラスチックの選択ガイド
耐薬品性が重要な化学業界において、コポリマーを使用することは品質向上の鍵となります。例えば、ポリプロピレンとエチレンプロピレンジエンゴム(EPDM)といったコポリマーは、耐薬品性に優れています。これは、化学物質に対して優れた耐性を持ち、長期間安定した性能を発揮することができるからです。
さらに、自動車部品や医療機器などの用途においても、コポリマーを含むプラスチックは幅広く活用されています。その理由は、耐久性や耐熱性、そして工業的な加工性に優れているからです。これらの特性により、製品の品質向上や安全性確保に貢献しています。
化学業界において、コポリマーを含む耐薬品性プラスチックは重要な要素となっており、選択する際にはその特性を理解することが肝要です。
アプリケーション別最適素材の選定
コポリマーは化学業界において耐薬品性を向上させる重要な役割を果たしています。例えば、コポリマーを使用することでプラスチック製品の耐薬品性が向上し、化学薬品や溶剤などの影響を受けにくくなります。このような改良は、製品の耐久性を高めるだけでなく、安全性も確保することにつながります。
コポリマーの利点は、その柔軟性と耐久性にあります。例えば、自動車部品や医療機器など幅広い分野で利用されており、厳しい環境下でも優れた性能を発揮します。これにより、製品の寿命を延ばすだけでなく、製品の品質を向上させることができます。
化学業界において、コポリマーは耐薬品性向上の重要な要素として注目されています。その特性を最大限に活かし、製品の品質や安全性を向上させるために、適切な素材選定が欠かせません。
化学業界におけるコポリマーの最新動向
コポリマーの市場動向と将来予測
化学業界において、コポリマーは耐薬品性向上の重要な要素として注目されています。コポリマーは2種類以上の異なる単量体で構成され、それぞれの特性を組み合わせることで、耐薬品性が向上します。例えば、ポリエステルとポリアミドのコポリマーは、化学薬品に対する耐久性が向上し、産業用途に適しています。さらに、コポリマーは柔軟性や耐熱性など、さまざまな特性を調整することができるため、幅広い産業で活用されています。
将来予測では、コポリマー市場は着実に成長を続け、特に耐薬品性が求められる産業分野での需要が高まることが期待されています。化学業界において、コポリマーは技術革新や製品開発において重要な役割を果たし、持続可能な社会の実現に貢献することでしょう。
新しい耐薬品性コポリマーの開発状況
化学業界必見!コポリマーを使った耐薬品性向上の秘訣
最近、新しい耐薬品性コポリマーの開発が進んでいます。これらのコポリマーは、化学薬品に対する耐性が高く、さまざまな産業分野で重要な役割を果たしています。
コポリマーは、異なる特性を持つ2種類以上の単量体から構成され、それぞれの特性を組み合わせることで耐薬品性を向上させることができます。例えば、化学工場で使用されるパイプやタンクの内部コーティングにコポリマーが使用されることで、薬品による腐食から保護されることができます。
このように、コポリマーは化学業界に革新をもたらし、耐薬品性向上の重要な技術として注目されています。そのため、新しいコポリマーの開発は今後も進められ、産業界に多大な影響を与えることが期待されています。
環境規制とコポリマーのイノベーション
化学業界における重要なテーマとして、コポリマーを使った耐薬品性の向上が注目されています。環境規制の厳格化に伴い、安全性と耐久性が求められる中、コポリマーは解決策として活用されています。
例えば、自動車の塗装やパイプラインの被覆などにコポリマーが利用されています。これにより、化学薬品や気候変動などの影響から保護されると同時に、製品の寿命が延びる効果が期待されています。
化学業界において、環境への配慮や製品の品質向上を追求する中で、コポリマーの利用は今後ますます重要となっていくでしょう。耐薬品性の向上を通じて、安全で持続可能な製品開発に貢献するコポリマーの可能性に注目が集まっています。
耐薬品性プラスチックの加工方法
コポリマーを含むプラスチックの成形技術
コポリマーを含むプラスチックは、耐薬品性向上に役立つ重要な材料です。工業製品や医療機器など、さまざまな分野で使用されています。例えば、食品容器や化学物質を扱う装置などは、耐薬品性が要求される場面です。
コポリマーを使用することで、プラスチック製品の強度や耐久性が向上し、薬品による劣化や変形を防ぐことができます。このように、コポリマーを含むプラスチックは、環境や安全面でも優れた性能を発揮します。
化学業界では、コポリマーを使った耐薬品性の向上が重要視されています。材料の選定や成形技術の進化により、より高性能なプラスチック製品が生まれることで、産業界全体の発展に寄与することが期待されています。
加工時の注意点と品質管理
化学業界必見!コポリマーを使った耐薬品性向上の秘訣
コポリマーは、化学業界で注目される素材です。薬品に対する耐性を向上させるために使用されています。例えば、自動車部品や建設材料などの耐久性を高めるためにコポリマーが活用されています。
コポリマーは異なる種類の分子から構成されており、それぞれの特性を組み合わせることで耐薬品性が向上します。これにより、化学製品や産業製品の品質が向上し、長期的な利用価値が高まります。
化学業界において、コポリマーを活用することで耐薬品性を向上させる方法が重要です。研究開発を通じてさらなる革新が期待され、産業界における競争力強化につながるでしょう。
特殊加工技術とその応用例
化学業界必見!コポリマーを使った耐薬品性向上の秘訣
コポリマーは、化学業界で注目される素材です。特に、薬品に対する耐性を向上させるために活用されています。例えば、コポリマーを加工して作られた貯蔵タンクは、薬品の腐食から保護する役割を果たします。
その理由は、コポリマーが化学薬品に対して耐久性が高いからです。薬品の性質によっては、金属製のタンクが腐食することがありますが、コポリマー製のタンクはそのような心配がありません。
さらに、コポリマーは軽量でありながら強度も兼ね備えているため、施工も容易です。そのため、多くの企業がコポリマーを活用して薬品性を向上させることで、安定した製品の製造を実現しています。化学業界におけるコポリマーの応用は、今後ますます重要性を増していくことが期待されています。
耐薬品性プラスチックの長期耐久性
長期耐久性の評価方法
コポリマーを使った耐薬品性向上の秘訣は、長期耐久性の評価方法にあります。化学業界では、材料の性能を評価する際に、耐久性が非常に重要です。コポリマーは、薬品に対する耐性が向上するため、さまざまな産業で利用されています。特に、化学製品や医療機器などの分野でその優れた特性が活かされています。
耐薬品性を向上させるためには、長期にわたる評価が必要です。例えば、特定の薬品に対するコポリマーの耐性を定期的にテストすることで、その性能を確認することができます。このような評価を通じて、製品の品質向上や安全性確保が図られ、顧客に信頼性の高い製品を提供することが可能となります。
したがって、コポリマーを活用する際には、長期耐久性の評価方法を適切に実施することが重要です。耐薬品性向上の秘訣は、確かな評価に基づいた製品開発と品質管理にあると言えます。
耐薬品性向上のためのコポリマーの改良
コポリマーは、耐薬品性を向上させるための重要な要素です。化学業界において、コポリマーは様々な製品や材料に利用されています。たとえば、プラスチック製品や塗料、接着剤などがあります。コポリマーは異なる種類の重合体が結合してできており、その組み合わせによって耐薬品性などの特性が向上します。
コポリマーを使った製品は、耐薬品性が求められる環境で幅広く活用されています。例えば、薬品を保管する容器や自動車の部品などがあります。このような製品は、化学物質や薬品に耐性があり、長期間安定して使用することができます。
結論として、コポリマーは耐薬品性向上において重要な役割を果たしています。その特性を活かして、さまざまな製品の品質向上や高性能化が実現されています。化学業界において、コポリマーの改良は今後も注目されるでしょう。
実用化事例とフィードバック
【化学業界必見!コポリマーを使った耐薬品性向上の秘訣】
工業製品や日常品で使われる材料には、耐久性が求められます。その中でコポリマーは、耐薬品性を向上させるために重要な役割を果たしています。例えば、自動車部品や医療機器など、薬品にさらされる製品において、コポリマーの使用は品質と安全性を高める効果があります。
コポリマーは異なる種類の重合体が結合した構造を持ち、それにより強度や耐熱性、耐候性などが向上します。このような特性を持つコポリマーは、化学業界で幅広く利用され、製品の性能を飛躍的に向上させる秘訣となっています。耐薬品性を求める製品の開発や製造において、コポリマーは欠かせない要素となっています。
まとめ
コポリマーを使用した耐薬品性の向上には、特定の分子構造や材料組成の変更が重要です。このようなコポリマーは、化学業界において薬品耐性の要求が高い製品に適しています。特定のコポリマーを使用することで、製品の性能を向上させることが可能です。これにより、製品の寿命が延びるだけでなく、環境への影響も軽減することが期待されます。
薬品に強いプラスチック!ポリアセタールの耐性能力を解説
薬品に接する場面は、日常生活だけでなく産業界でも非常に重要です。そんな中、ポリアセタールは薬品に強いプラスチックとして注目を集めています。本記事では、ポリアセタールの耐性能力について詳しく解説していきます。ポリアセタールとは一体何なのか、どのような特性を持っているのか、薬品に対する耐性能力はどのように高められるのか。これらの疑問にお答えするべく、本記事ではポリアセタールの魅力と応用分野について探っていきます。薬品に関わるあらゆる状況において、ポリアセタールがどのような役割を果たすのか、その真実が明らかになります。
ポリアセタール(POM)の基本
ポリアセタールの定義と概要
ポリアセタールは、耐性能力に優れたプラスチックの一種です。化学的に安定性が高く、耐薬品性に優れている特徴があります。この特性から、様々な産業分野で幅広く利用されています。例えば、機械部品や自動車部品、電子機器などでよく使用されています。
ポリアセタールの耐性能力は、化学薬品や溶剤、油、熱、摩耗などから保護する役割を果たします。そのため、環境にさらされる機械部品や工業製品において、高い信頼性を提供しています。
このように、ポリアセタールはその耐性能力によって広く用いられており、産業界において重要な役割を果たしています。
POM樹脂の化学的性質
ポリアセタール(POM)は、薬品に強いプラスチックとして知られています。この特性は、化学的な性質に由来しています。ポリアセタールは耐性が高く、何種類もの薬品に対して優れた耐性を持っています。そのため、工業製品や自動車部品などの分野で幅広く利用されています。
例えば、自動車のエンジン部品やギア、電子機器の部品などにポリアセタールが使われています。これは、薬品による劣化や変形を抑制し、耐久性を向上させるためです。
さらに、ポリアセタールは耐熱性や耐摩耗性にも優れており、長期間安定した性能を発揮します。このような特性から、様々な産業分野で広く活用されているのです。これらの理由から、ポリアセタールは薬品に強いプラスチックとして注目されています。
ポリアセタールの分類と種類
ポリアセタールは、薬品に強いプラスチックとして知られています。その耐性能力は、化学薬品や溶剤に対して優れており、機械部品や電気部品として広く利用されています。
ポリアセタールは、耐薬品性、耐摩耗性、硬度、剛性などの特性を持っており、自動車部品や歯車、ファスナー、電気スイッチなど幅広い用途に使われています。
このような特性から、ポリアセタールは様々な産業分野で重要な役割を果たしています。化学薬品や溶剤にさらされる環境での使用が求められる場面で、その耐性能力を発揮し、安定した性能を提供します。
ポリアセタールの優れた特性により、産業界での需要が高まり、今後もさらなる進化が期待されています。そのため、ポリアセタールは今後も注目されるプラスチック材料として、さまざまな分野で活躍することでしょう。
ポリアセタールの耐薬品性
薬品耐性とは何か?
ポリアセタールは、薬品に強いプラスチックとして注目されています。薬品耐性とは、化学物質や薬品に対して変質や劣化が少ない性質を指します。例えば、化学薬品を取り扱う産業分野や医療機器などで重宝されています。
ポリアセタールは、耐熱性や摩耗耐性に優れているため、様々な用途に幅広く使われています。薬品に対する耐性能力が高いことから、自動車部品や電子機器の製造にも活用されています。
このように、ポリアセタールはその薬品に対する高い耐性能力からさまざまな産業分野で重宝されている素材です。その信頼性と使い勝手の良さから、さらなる注目が集まっています。
POM樹脂の耐薬品性のメカニズム
ポリアセタール(POM)は、薬品に強いプラスチックとして知られています。この耐性能力は、POMの構造に由来しています。POMは分子が密に結合しており、化学的な薬品攻撃から分子を守る防護バリアを形成しています。例えば、酸やアルカリ、溶剤などの薬品に対して耐性を示します。
さらに、POMは高い剛性と耐摩耗性も備えており、機械部品などに広く利用されています。自動車部品や工業機械、家電製品など、さまざまな分野でPOMの耐性能力が活かされています。
このように、POMはその耐薬品性や強度などの特性から幅広い用途で活躍しています。工業製品の製造や構造物の耐久性向上など、さまざまな分野で重要な役割を果たしています。
耐薬品性を活かしたポリアセタールの実用例
ポリアセタールは、その耐薬品性によりさまざまな用途で活躍しています。例えば、自動車部品や工業製品に広く使用されています。この素材は、化学薬品や油などの影響を受けにくく、耐久性に優れています。そのため、エンジン部品やギア、ベアリングなど、高い耐久性が求められる部品に利用されています。
さらに、食品関連の分野でもポリアセタールは重要な役割を果たしています。例えば、調理器具や食器などに使われていることがあります。この素材は食品との相性がよく、衛生面でも優れているため、食品産業で広く採用されています。
ポリアセタールはその耐性能力から幅広い分野で利用されており、その優れた特性がさまざまな産業に貢献しています。
ポリアセタール樹脂の特性と用途
POM樹脂の物理的特性
ポリアセタール(POM)は、耐薬品性に優れたプラスチック材料です。化学薬品や溶剤に対して強い抵抗力を持ち、優れた特性を示します。例えば、自動車部品や工業製品などで幅広く使用されています。POMは機械的特性も優れており、強度や耐摩耗性が高いため、歯車やベアリングといった精密部品に適しています。加えて、POMは熱や湿気にも強く、安定した性能を維持します。そのため、耐熱性や耐久性が求められる環境下でも優れた実績を示しています。ポリアセタールは、さまざまな産業分野で重要な役割を果たしており、その耐薬品性や物理的特性から幅広い用途に活用されています。
POMの機械的特性
ポリアセタール(POM)は薬品に強いプラスチックとして注目されています。耐性能力が高く、化学薬品や溶剤に対して耐久性があります。この特性から、自動車部品や機械部品などの産業分野で幅広く使用されています。
POMの特徴の一つは、優れた機械的特性を持っていることです。例えば、疲労強度が高く、摩耗にも強いため、歯車やベアリングなどの部品に適しています。また、耐熱性や耐蝕性も優れており、長期間安定した性能を維持できます。
このようにPOMは、その耐性能力や機械的特性によってさまざまな産業分野で重要な役割を果たしています。化学薬品に強いプラスチックとして、幅広い用途で活躍しています。
ポリアセタールの主な用途と応用分野
ポリアセタールは、薬品に強いプラスチックとして知られています。その耐性能力や特性からさまざまな分野で活躍しています。例えば、自動車部品や電子機器のギアや軸受け、インジェクションモールディング部品などに広く利用されています。ポリアセタールは、化学薬品や溶剤に対する耐性が高く、機械的な強度や剛性も優れています。これにより、耐摩耗性や耐久性に優れているため、長期間にわたって安定した性能を発揮します。
さらに、ポリアセタールは低摩擦特性も持ち合わせており、潤滑剤を必要としない利点があります。これは、機械部品や歯車などの摩擦を低減し、耐久性を向上させるのに役立ちます。そのため、産業機器や家庭用品など幅広い分野で重要な役割を果たしています。ポリアセタールは、その特性から多くの産業分野で重要な素材として活用され、高い需要が期待されています。
プラスチック加工技術とPOM
プラスチック加工技術の概要
ポリアセタールは、薬品に強いプラスチックとして知られています。その耐性能力について解説します。ポリアセタールは化学薬品や油、溶剤に対して優れた耐性を持ち、機械的強度も高いため、様々な産業で幅広く使用されています。例えば、自動車部品や家電製品、工業機械などで活用されています。
さらに、ポリアセタールは温度変化にも強いため、高温下や低温下でも性能を維持します。この特性から、エンジニアリングプラスチックとして要求の厳しい環境下で重要な役割を果たしています。耐久性や耐摩耗性にも優れており、長期間安定した性能を提供します。
ポリアセタールの耐性能力により、さまざまな産業分野で重要な役割を果たしており、今後もその需要は高まると考えられます。
ポリアセタール樹脂の加工適性
ポリアセタール樹脂は、薬品に強いプラスチックとして注目されています。その耐性能力について解説します。ポリアセタールは耐薬品性に優れており、化学薬品や溶剤に対して高い安定性を持っています。この特性から、医療機器や自動車部品、家電製品などの分野で幅広く使用されています。
例えば、自動車用エンジン部品にポリアセタール樹脂が使用されることがあります。エンジン部品は高温条件や化学薬品に触れることが多いため、耐久性が求められます。ポリアセタールはこれらの要件を満たすため、信頼性の高い素材として重要な役割を果たしています。
そのため、ポリアセタール樹脂はその耐性能力からさまざまな産業分野で幅広く活用され、製品の信頼性向上に貢献しています。
POM加工時の注意点
ポリアセタールは、薬品に強いプラスチックとして知られています。この耐性能力は、化学薬品や溶剤に対して優れた耐性を持つため、さまざまな産業分野で幅広く利用されています。例えば、自動車部品や家電製品など、耐久性が求められる製品に使用されています。
ポリアセタールの特性は、高い剛性と強度、耐摩耗性、耐熱性などが挙げられます。このため、機械部品や歯車などの精密な部品にも広く利用されています。さらに、食器やカトラリーなどの日常品にもポリアセタールが使われていることがあります。
化学物質に対する耐性が高いポリアセタールは、安全性や信頼性が求められる製品において重要な素材として使用されています。そのため、環境への影響や人体への安全性を考慮しながら、ポリアセタールを適切に加工することが重要です。
ポリアセタール(POM)樹脂の長所と短所
ポリアセタールの長所
ポリアセタールは、薬品に強いプラスチックとして知られています。その特徴は耐性能力にあります。例えば、化学薬品や溶剤、油、脂肪、さらには熱や湿気にも強いのです。この耐性能力が、さまざまな産業分野で重宝されています。
ポリアセタールの優れた性質を理解するために、化学製品の取扱いや自動車部品、電子機器など、身近な製品にも活用されている例を挙げてみましょう。自動車のインジェクションポンプや電子機器のギア、家電製品の歯車など、ポリアセタールはさまざまな場面で活躍しています。
その強靭な性質から、ポリアセタールは機能性や信頼性が求められる製品開発において重要な材料として注目されています。このように、ポリアセタールは多くの利点を持ち、幅広い産業で活躍しているプラスチックなのです。
ポリアセタールの短所
ポリアセタールは、耐薬品性に優れたプラスチックの一種です。しかし、注意すべき短所も存在します。例えば、ポリアセタールは高温に弱い性質を持っています。これは、高温での長時間の使用によって劣化しやすくなることを意味します。さらに、ポリアセタールは耐候性にもやや難があります。屋外での使用や紫外線の影響を受ける環境下では、劣化が進行しやすい特性があります。これらのポイントを考慮しながら、ポリアセタールの利用を検討する際には、適切な使い道や環境を選ぶことが重要です。
他材料との比較
ポリアセタールは、薬品に強いプラスチック素材です。この素材は耐性能力に優れており、化学薬品や溶剤、燃料などの影響を受けにくい特性があります。他のプラスチック素材と比較すると、ポリアセタールは優れた耐性能を持っています。例えば、ポリエチレンやポリプロピレンと比べても、ポリアセタールは化学薬品に対して優れた耐性を示します。このような特性から、ポリアセタールは自動車部品や電子機器など、厳しい環境下で使用される製品に広く利用されています。そのため、耐性能が求められるさまざまな産業分野でポリアセタールが重要な役割を果たしています。
ポリアセタール(POM)の加工方法
切削加工
ポリアセタールは、薬品に強いプラスチックとして注目を集めています。化学的に安定しており、耐性能力が高い特徴を持っています。例えば、薬品や溶剤に対して優れた耐久性を発揮します。この特性から、医療機器や自動車部品などの分野で広く使用されています。ポリアセタールは、耐熱性や機械的な強度も優れており、機能性に優れたプラスチックとして重宝されています。さらに、摩耗や摩擦にも強いため、耐久性が求められる部品に適しています。そのため、工業製品や機械部品などの分野でも広く利用されています。ポリアセタールは、多岐にわたる産業分野で重要な役割を果たしており、その耐性能力が高い特性から幅広い用途で活躍しています。
射出成形
ポリアセタール(POM)は、薬品への耐性に優れたプラスチックとして注目されています。この特性があるため、自動車部品や機械部品などの産業製品に広く使われています。POMは、化学薬品や溶剤などの影響を受けにくく、強度と硬度が高いため、耐久性に優れています。さらに、摩耗に強い特性があり、長期間使用しても変形しにくいのが特徴です。
例えば、自動車の歯車や電子機器の部品に使用されることが多く、その信頼性が高く評価されています。POMは、耐熱性や寸法安定性にも優れており、高温環境でも安定した性能を発揮します。このように、ポリアセタールは様々な産業分野で幅広く活用されている強靱なプラスチック材料です。
押出成形
ポリアセタールは、薬品に強いプラスチックとして知られています。この素材は耐性能力が高く、化学薬品や溶剤に対して優れた耐性を持っています。例えば、自動車部品や電子機器のギアやベアリング、家庭用品などに幅広く利用されています。
ポリアセタールは、耐摩耗性や機械的な強度にも優れており、長期間にわたって高い性能を維持します。そのため、耐久性が求められる製品に適しています。さらに、耐熱性にも優れているため、高温環境下でも安定した性能を発揮します。
ポリアセタールの特性を活かして、さまざまな産業分野で幅広く利用されていることから、その耐性能力は高く評価されています。このように、ポリアセタールは薬品に強いプラスチックとして、幅広い用途において重要な役割を果たしています。
その他の加工方法
ポリアセタールは、薬品に強いプラスチックとして注目されています。その耐性能力は、化学薬品や溶剤に対して優れており、耐食性にも優れています。例えば、自動車部品や電子機器などの製品に広く使用されています。その理由は、ポリアセタールが化学的に安定しているため、薬品や溶剤などの影響を受けにくいからです。
さらに、ポリアセタールは摩耗や疲労にも強く、耐久性が高い特性があります。これにより、長期間使用しても変形しにくいため、耐久性を求められる部品や機器に適しています。そのため、歯車やベアリングなど、高い耐久性が求められる製品に広く利用されています。
ポリアセタールの耐性能力は、様々な産業分野で重要視されており、その特性を活かした製品が幅広く展開されています。そのため、ポリアセタールは現代の産業界において欠かせないプラスチックの一つと言えるでしょう。
耐磨耗性に優れたPOM(ジュラコン®)の特徴
ジュラコン®の耐磨耗性とは
薬品に強いプラスチック!ポリアセタールの耐性能力を解説
ポリアセタールは、化学薬品や摩耗に強いプラスチック素材です。この耐性能力のおかげで、様々な産業分野で幅広く活用されています。具体例として、自動車部品や電子機器の部品、医療機器、スポーツ用具などでポリアセタールが使用されています。化学薬品にさらされる環境や高摩耗の状況でも、ポリアセタールは優れた耐久性を発揮します。
このように、ポリアセタールは優れた特性を持つプラスチック素材であり、その耐性能力は様々な産業で重宝されています。そのため、今後もさらなる発展が期待される素材と言えるでしょう。
耐磨耗性が求められる環境と用途
ポリアセタールは、耐磨耗性が求められる環境や用途において重要な役割を果たしています。例えば、薬品に強いプラスチックとして、機械部品や自動車部品などの製造に広く使用されています。その耐性能力から、化学薬品や油、ガソリンなどの影響を受けにくく、長期間にわたって安定した性能を維持することができます。
さらに、ポリアセタールは摩擦にも強く、機械部品の動作時に生じる摩耗を軽減する役割を果たします。そのため、歯車やベアリングなどの部品に広く利用されています。耐久性が求められる環境での使用において、ポリアセタールは信頼性の高い素材として注目されています。
このように、ポリアセタールはその耐久性や耐性能力から多様な産業分野で重宝されており、今後もさらなる技術革新が期待されています。
ジュラコン®の耐久性と経済性
ポリアセタールは、薬品に強いプラスチックとして注目されています。耐久性に優れ、化学薬品や溶剤に対する耐性が高い特性を持っています。例えば、工業用途ではポリアセタールは、潤滑剤として使用される機械部品や歯車で広く利用されています。その理由は、化学薬品による影響を受けにくいため、長期間にわたって安定した性能を維持できるからです。
さらに、自動車産業でも、ポリアセタールはギアやベアリングなどの部品に使用されています。これは、軽量でありながら強度があり、耐摩耗性に優れているため、車両の性能を向上させる役割を果たしています。
ポリアセタールはその耐久性と経済性から、様々な産業で幅広く活用されています。その特性を活かし、さまざまな製品の性能向上や耐久性の向上に貢献しています。
まとめ
ポリアセタールは、化学薬品に強いプラスチックとして知られています。その耐性能力は高く、薬品に対する耐性も備えています。この特性から、工業製品や医療機器、自動車部品など様々な分野で利用されています。ポリアセタールは、薬品に対する耐性が必要な場合には有用な素材であり、その特性を理解した上で適切に利用することが重要です。
ジュラコン素材の耐薬品性能とは?選び方のポイント解説
ジュラコン素材は、その耐薬品性能において特筆すべき特性を持っています。薬品に対する耐性が高いことから、様々な産業分野で重宝されています。耐薬品性能を求める際、ジュラコン素材は優れた選択肢となるでしょう。本記事では、ジュラコン素材の耐薬品性能に焦点を当て、その選び方のポイントを詳しく解説していきます。ジュラコン素材を使用する際のメリットや注意点を知りたい方にとって、この記事は役立つ情報源となるでしょう。
ジュラコン素材の基本
ジュラコンとは何か?
ジュラコンは、耐薬品性に優れた素材です。薬品や化学物質に強い耐性を持ち、その特性からさまざまな産業分野で広く利用されています。例えば、医療機器や自動車部品、食品加工機器などに使用されています。ジュラコンは耐久性があり、耐熱性や耐摩耗性にも優れています。そのため、長期間安定した性能を発揮し、製品の寿命を延ばす効果が期待されています。ジュラコンの優れた特性を活かすためには、適切な素材選択が重要です。使用環境や必要な性能に合わせて適切なジュラコン製品を選ぶことが重要です。耐薬品性が必要な場面では、ジュラコンは信頼性の高い選択肢となることが多いです。
ジュラコン素材の一般的な特性
ジュラコン素材は、耐薬品性能が高い特長を持っています。化学薬品や溶剤に対して優れた耐性を示し、その安定性から様々な産業で重要な役割を果たしています。例えば、医療機器や自動車部品、工業機械などで広く使用されています。この素材は高温や高圧にも耐えられるため、厳しい環境下でも優れた性能を発揮します。
ジュラコン素材を選ぶ際のポイントは、耐久性や耐熱性、耐摩耗性などが重要です。特に化学薬品に触れる環境では、耐薬品性が必須となります。そのため、使用する環境や条件に応じて、適切なジュラコン素材を選ぶことが重要です。
ジュラコン素材はその特性から幅広い産業で利用されており、その耐久性や耐薬品性能によって信頼性が高い素材として注目されています。
ジュラコンの適用分野と例
ジュラコン素材は、耐薬品性能が高いことからさまざまな分野で利用されています。例えば、工業用ポンプやバルブ、化学プラントの部品などで広く採用されています。これは、ジュラコンが化学薬品に対して優れた耐性を持ち、長期間安定した性能を発揮するためです。
さらに、医療機器や歯科材料、時計の部品などの分野でもジュラコン素材が重宝されています。例えば、人体内で使用される部品にも採用されることがあります。そのため、生体親和性が高く、安全性が確保されていることがポイントとなります。
ジュラコン素材はその耐薬品性能や多様な適用分野から、幅広い産業で重要な役割を果たしています。
ジュラコンの耐薬品性能
薬品耐性とは?
ジュラコン素材の耐薬品性能とは、化学薬品や溶剤などの影響に対する素材の持つ耐性や耐久力のことです。ジュラコンは、その高い化学的安定性から薬品に対して優れた耐性を持つ素材として知られています。例えば、強力な溶剤や薬品が使用される環境でも、ジュラコン素材は変形や劣化を起こしにくく、長期的な耐久性を発揮します。これにより、工業用途や医療機器などの分野で広く利用されています。
ジュラコン素材を選ぶ際のポイントは、耐薬品性能だけでなく、耐熱性、機械的強度、耐摩耗性などの性能も重要です。特に、薬品に直接触れる環境では、素材の特性を正しく理解し、適切な素材を選択することが重要です。これにより、安全性や効率性を確保しつつ、長期間良好な性能を維持することができます。
ジュラコンの耐薬品性能の詳細
ジュラコン素材は、耐薬品性能に優れています。この耐薬品性能は、化学薬品や溶剤などさまざまな薬品に対して、変色や変質せずに耐える能力を指します。例えば、工業用途や医療機器などで使用される際には、耐久性が求められます。ジュラコン素材はそのような環境下でも安定した性能を発揮し、信頼性が高いと言えます。また、食品関連の業界でも使用されており、耐性が重要視されるケースが多いです。
選ぶ際のポイントとしては、耐薬品性能だけでなく、耐熱性や耐摩耗性などの特性も考慮するとよいでしょう。ジュラコン素材はその多様な特性から、幅広い用途に活用されています。素材の特性を理解し、適切に選択することで、効果的な利用が可能となります。ジュラコン素材は、その特性からさまざまな産業分野で重要な役割を果たしており、その耐薬品性能は高い評価を受けています。
耐薬品性を評価する指標
耐薬品性を評価する指標
ジュラコン素材の耐薬品性能は、化学物質や薬品に対する耐性を示す重要な特性です。例えば、薬品に接触する産業や研究施設では、耐薬品性が要求されます。ジュラコンは、その耐久性や耐薬品性により、さまざまな用途に利用されています。
ジュラコン素材は、強酸や強アルカリ、有機溶剤などの薬品に対して優れた耐性を持っています。この特性により、産業機器や医療機器など、厳しい環境下で使用される製品に適しています。耐薬品性が高いため、長期間安定した性能を維持することができ、信頼性が高いと言えます。
ジュラコン素材の選び方のポイントは、使用環境や必要な耐性に適した製品を選択することです。耐薬品性を十分に考慮し、適切なジュラコン製品を選ぶことで、製品の耐久性や安全性を確保することができます。
ジュラコンとPOM(ポリオキシメチレン)の違い
ジュラコンとPOMの材料としての特徴
ジュラコン素材は、耐薬品性能に優れています。耐薬品性とは、化学薬品や溶剤などの影響を受けずに性能を保つことができる能力のことです。ジュラコンは、化学的な安定性が高く、耐油性や耐溶剤性に優れています。これにより、食品加工機械や自動車部品などの産業製品に広く使用されています。
ジュラコン素材を選ぶ際のポイントは、まずは使用環境や条件に応じた耐性を確認することです。さらに、寸法安定性や機械加工性も重要な要素です。例えば、ジュラコン製の歯車は高い耐摩耗性と低い摩擦係数を持ち、長期間の使用に適しています。
ジュラコン素材の特性を理解し、適切に選定することで、耐薬品性に優れた製品を開発・製造することが可能となります。
ジュラコンとPOMの化学的差異
ジュラコンとPOMの化学的差異について考えてみましょう。ジュラコンは、耐薬品性に優れた特性があります。これは、化学的に不活性であり、多くの化学薬品に対して安定した性能を発揮します。一方、POMはジュラコンと比較すると、化学的に薬品に弱い面があります。例えば、強い酸やアルカリ性溶液に対して、POMは劣る耐性を持っています。
ジュラコンの一般的な応用例として、医療機器や自動車部品などが挙げられます。これらの分野では、耐久性や安定性が求められるため、ジュラコン素材が好んで使用されています。したがって、耐薬品性を重視する場合は、ジュラコンを選択することがポイントとなります。そのため、応用目的や環境条件に応じて、素材を適切に選定することが重要です。
ジュラコンとPOMの物理的特性比較
ジュラコン素材の耐薬品性能とは?選び方のポイント解説
ジュラコンは、その耐薬品性能に優れていることからさまざまな産業分野で重宝されています。化学薬品や溶剤などの影響を受けにくく、耐久性に優れています。例えば、自動車部品や医療機器、食品加工機器などで広く使用されています。
理由として、ジュラコンは化学的に安定しており、耐熱性や耐摩耗性にも優れています。これにより、様々な厳しい環境下でも高い性能を維持できるのです。そのため、薬品や化学薬品が多用される環境では、ジュラコンが選択される傾向があります。
ジュラコンの物理的特性は、POM(ポリオキシメチレン)と比較しても優れています。薬品に強い素材を必要とする場合、ジュラコンは信頼性の高い選択肢となるでしょう。
ジュラコンの加工性
フライス加工とは?
ジュラコン素材は、耐薬品性に優れた特性を持っています。薬品に対して強い耐性を持つため、さまざまな産業分野で重宝されています。例えば、医療器具や自動車部品、食品加工機械などが挙げられます。ジュラコンは、耐熱性や機械的強度にも優れており、長期間使用される環境にも適しています。
ジュラコン素材を選ぶ際のポイントは、耐薬品性だけでなく、耐熱性や機械的特性にも注目することが重要です。特に、化学物質にさらされる環境や高温の条件下で使用される場合には、より耐性の高いジュラコン素材を選択することが求められます。このように、ジュラコン素材の特性を理解し、適切な用途に使うことで、耐久性や安全性を確保することができます。
ジュラコンのフライス加工適性
ジュラコン素材は耐薬品性に優れています。この性能は化学薬品や溶剤に対して高い耐性を持つため、医療機器や工業製品などの用途で重宝されています。ジュラコン素材を選ぶ際のポイントは、その耐薬品性能が挙げられます。例えば、ジュラコン製の歯科用インプラントは口の中でさまざまな薬品と接触するため、その耐性が重要です。また、機械部品やシールなどでも薬品に対する安定性が求められます。ジュラコンはこれらの要求に応える優れた素材であり、その特性を理解した上で適切に選定することが重要です。耐薬品性に優れたジュラコン素材を利用することで、製品の耐久性や安全性を確保することができます。
POMのフライス加工適性との比較
ジュラコン素材の耐薬品性能とは?選び方のポイント解説
ジュラコン素材は、化学薬品に対する耐性に優れています。この特性から、様々な産業で使用されており、特に薬品に触れる環境下では信頼性が高い素材として知られています。
ジュラコン素材の耐薬品性能を選ぶ際に重要なポイントは、使用する薬品の種類や濃度、および温度などの条件に適した素材を選ぶことです。例えば、病院の医療器具や化学工場の設備など、厳しい環境下で使用される場合は、ジュラコン素材の適性が問題となります。
したがって、ジュラコン素材を選ぶ際には、耐薬品性能を確認することが重要です。適切な素材を選ぶことで、耐久性や安全性を確保し、製品の性能向上につながることが期待されます。
プラスチック素材の選び方
プラスチック選択の基準
ジュラコン素材は耐薬品性能に優れていますが、選ぶ際のポイントを知っておくことが重要です。ジュラコンは化学薬品に対して強い耐性を持ち、耐久性にも優れています。例えば、化学工場や医療機器、食品加工などの分野で幅広く使用されています。そのため、薬品に触れる環境で使用する際に適しています。また、ジュラコン製品は高温にも耐えられるため、加熱処理が必要な場面でも安心して使用できます。耐久性や耐薬品性が求められる産業や用途において、ジュラコン素材は信頼性が高く適していると言えます。臨機応変に適切な素材を選ぶことで、効率的かつ安全な環境を確保できます。
使用環境に応じたジュラコンの選び方
ジュラコン素材は、耐薬品性に優れた特性を持っています。ジュラコンを選ぶ際には、使用環境によって適したタイプを選ぶことがポイントです。例えば、化学薬品が多く使用される工場では、耐薬品性が高いジュラコンが必要となります。その他、医療機器や食品加工業界などでも同様に耐薬品性の重要性が高まっています。
また、ジュラコン素材は耐熱性や耐摩耗性にも優れており、長期間安定して使用することができます。これにより、作業効率を向上させるだけでなく、コスト削減にもつながります。さらに、ジュラコンの表面は滑らかで清潔なため、衛生面でも優れています。
使用環境に合わせた適切なジュラコンの選択は、安全性と効率性を確保する上で重要です。耐薬品性能に優れたジュラコン素材を選ぶことで、様々な産業分野での利用価値が高まることが期待されます。
コストと性能のバランス
ジュラコン素材は、耐薬品性能に優れていることからさまざまな産業で利用されています。この素材を選ぶ際に重要なポイントは、コストと性能のバランスです。例えば、化学薬品を扱う工場では、耐薬品性能が高いジュラコン素材が欠かせません。耐久性に優れ、化学薬品による腐食や変質を防ぐことができます。さらに、食品加工業界でもジュラコン素材は重宝されています。食品との接点が多いため、衛生面や耐久性が求められるからです。このように、ジュラコン素材の耐薬品性能は、さまざまな産業において重要な役割を果たしています。選び方のポイントを理解し、コストと性能のバランスを考えながら素材を選ぶことが重要です。
まとめ
ジュラコン素材は、その耐薬品性能で注目されています。この素材は、化学薬品や溶剤に対して非常に優れた耐性を持っており、さまざまな産業分野で利用されています。そのため、選び方のポイントを理解することが重要です。特に、薬品耐性を求める環境下では、ジュラコン素材の使用を検討する価値があります。