POM材加工で重要な表面粗さとは?理想的な仕上がりを追求する方法
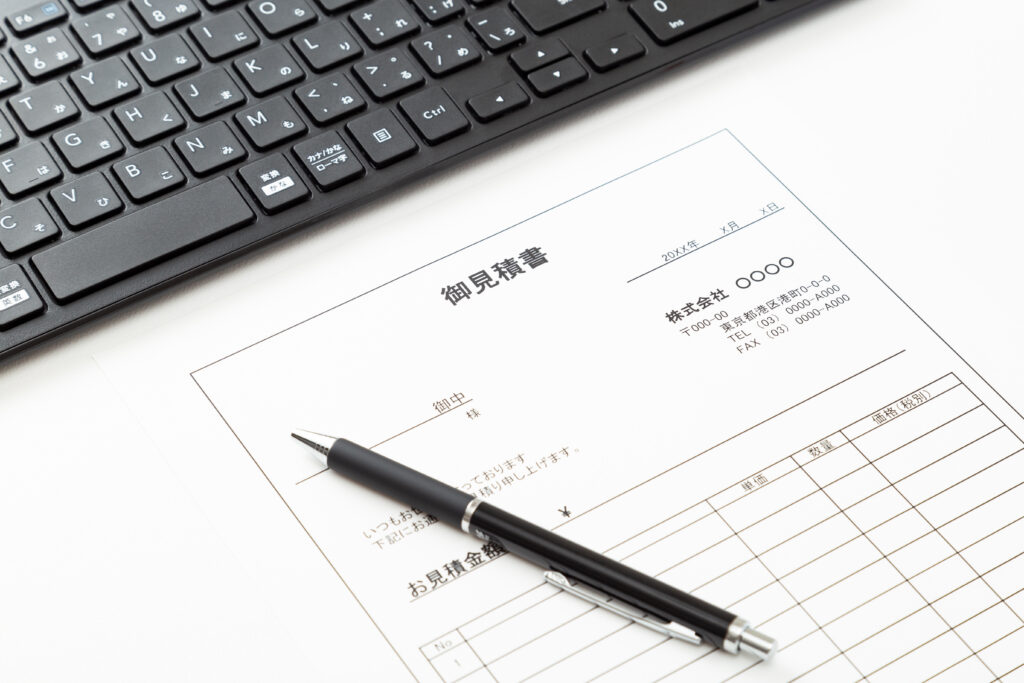
POM材加工において、理想的な仕上がりを実現するために不可欠な要素とは一体何でしょうか?表面粗さというポイントは重要な意味を持ち、製品の品質や機能性に大きな影響を与える要素として取り沙汰されています。本記事では、POM材加工における表面粗さの重要性に焦点を当て、その理想的な仕上がりを求める際の方法を探求していきます。POM材の特性や加工技術、表面仕上げのポイントなど、知っておくべきすべての情報を詳しく解説します。製品の品質向上や加工効率の向上に繋がる重要なヒントが満載です。ご一読いただき、POM材加工における表面粗さについての理解を深めてみてください。
POM材とは?
POM(ポリオキシメチレン)は、耐摩耗性や剛性に優れたエンジニアリングプラスチックで、「デルリン」としても知られています。機械的性能が高く、優れた加工性を持つため、多様な工業製品に利用されています。
POM材の基本特性
特性 | 詳細説明 |
---|---|
耐摩耗性 | 摩擦や磨耗に強く、長期間使用しても劣化しにくい。 |
剛性 | 高い剛性を持ち、変形しにくい。 |
耐薬品性 | 化学薬品に対しても安定した性能を保つ。 |
加工性 | 精密な形状に加工しやすく、高い寸法安定性を持つ。 |
表面仕上げ | 非常に滑らかな表面処理が可能、0.1μm単位で高精度な測定が可能。 |
表面粗さとその重要性
POM材の加工において表面粗さは重要な要素です。理想的な仕上がりを達成するためには、以下の点が重要です。
表面粗さの要件
- 測定単位: 0.1μm単位で測定可能
- 理想的な表面粗さ: 0.8μm〜3.2μm程度
- 影響: 表面粗さが均一であることは、加工品の見た目や機能性を向上させます。
表面粗さの測定には、自動測定機器や専用の測定器具を使用します。これにより高精度な測定が可能となり、最終製品の品質を向上させます。
POM材の工業的利用
POM材は、その特性を活かしてさまざまな工業分野で使用されています。以下はその主な利用例です。
利用分野
- 機械部品: 摩擦係数が低く、滑りやすい表面が求められる部品。
- 自動車部品: 高い機械的性能が要求される部品。
- 医療機器: 精密さと耐薬品性が求められる部品。
- 電子機器: 高い寸法安定性と精密な加工が求められる部品。
POM材と他樹脂素材との比較
POMは他の樹脂素材と比較して、以下のような特性を持っています。
特性比較
表面仕上げ: POMは滑らかな表面処理が可能だが、他の樹脂素材によって異なる。
耐摩耗性: POMは非常に高いが、他の樹脂素材によって異なる。
剛性: POMは高いが、他の樹脂素材によって異なる。
耐薬品性: POMは優れているが、他の樹脂素材によって異なる。
加工性: POMは精密な形状に加工しやすいが、他の樹脂素材によって異なる。
表面粗さの基礎知識
表面粗さとは?
表面粗さは、POM(ポリオキシメチレン)材料の加工において非常に重要な要素です。特に精密部品、例えばPOM製の歯車においては、表面粗さが均一でないと歯車同士がスムーズに噛み合わず、動作に支障をきたす可能性があります。表面粗さを適切に管理することは、製品の見た目や機能性を維持するために不可欠です。
表面粗さの測定単位と指標
表面粗さの測定には、以下の指標が使用されます。これらを理解し、最適な加工方法を選定することが重要です。
指標 | 説明 |
---|---|
Ra | 平均粗さ(平均的な表面の粗さを示す) |
Rz | 最大高さ(最高点と最低点の差を示す) |
Rmax | 最大略面高さ(粗さの中で最も高い略面の高さ) |
POM材の表面粗さを高精度で測定するためには、これらの指標を基にした加工技術や切削工具の選定が重要です。適切なRa値を達成するためには、加工工程の設計にも注意が必要です。
表面粗さが製品性能に与える影響
表面粗さが製品性能に与える影響は次の通りです。適切な粗さの管理が製品の機能や寿命に直結します。
表面粗さの状態 | 影響 |
---|---|
滑らかすぎる | 摩擦が不十分になり、動力伝達ができなくなる可能性がある |
荒れすぎる | 耐久性が低下し、製品の寿命が短くなる恐れがある |
表面粗さが滑らかすぎると、摩擦が不足し動力伝達が困難になります。逆に荒れすぎると、耐久性が低下し、製品寿命に悪影響を及ぼします。最適な表面粗さを保つことが、製品の摩擦特性や耐久性を向上させるためには非常に重要です。
POM材における表面粗さの最適化
POM材の加工において、適切な表面粗さを保つことが品質と性能を最適化する鍵となります。以下の方法が推奨されます。
- 切削工具の選定: 使用する工具が表面粗さに大きく影響します。例えば、ダイヤモンドコーティング工具を使用することで、より滑らかな表面仕上げが可能になります。
- 加工条件の設定: 切削速度や送り速度を最適化することで、均一な表面粗さを実現できます。
- 仕上げ工程の工夫: 研磨や仕上げ加工を行うことで、表面の滑らかさを向上させることができます。
POM材における表面粗さを適切に管理することで、製品の機能性と耐久性が大きく向上します。特に精密部品を製造する際は、表面粗さの管理が製品の品質に直結します。
POM材の切削加工と表面粗さ
POM材の切削加工方法
POM材の切削加工では、表面粗さを最適化するために、適切な加工条件、工具の選定、切削方向の最適化、冷却剤の使用などが重要です。以下の要素に留意することで、より滑らかな表面仕上げが可能になります。
要素 | 説明 |
---|---|
加工条件 | 適切な切削速度や切削量を設定し、表面を滑らかに仕上げることが重要 |
切削工具 | 刃先形状や材料に適した切削工具の選定が重要 |
切削方向 | 切削方向の最適化が表面仕上げに影響を与える |
冷却剤の使用 | 適切な冷却剤の使用が表面粗さの改善に役立つ |
振動対策 | 切削時の振動を抑えることで表面粗さが向上する |
POM材の切削加工での表面粗さ向上のための方法
POM材の切削加工で表面粗さを向上させるためには、加工条件や工具の選定が非常に重要です。特にミリング加工においては、以下の点に注意することでより滑らかな仕上げを実現できます。
- 回転数: 適切な回転数を設定することで、表面の滑らかさを保つことができます。
- 刃先形状: 切削工具の刃先形状を適切に選ぶことで、より滑らかな表面を得られます。
- 冷却剤の使用: 冷却剤を使用することで、切削時の熱を抑え、材料の溶着を防ぎます。
- 振動対策: 振動を抑制することで、切削中の不均一な力が表面に与える影響を減らし、仕上がりを良くします。
樹脂切削加工での表面粗さRa1.6の実現可能性
POM材の加工において、Ra1.6という表面粗さはしばしば目標とされます。この表面粗さは加工品質や耐摩耗性に直結し、以下の要素が重要です。
要素 | 説明 |
---|---|
表面粗さRa1.6 | POM材の加工において目標とされる表面粗さ |
加工品質 | 表面粗さRa1.6は加工品質や耐摩耗性に直結 |
用途例 | 歯車部品などでは表面粗さが動作や耐久性に影響を与える |
POM材の表面粗さRa1.6を実現することで、製品の耐久性や摩擦特性が向上し、性能が最適化されます。
表面粗さRa1.6の実現に向けた工夫
POM材の表面粗さRa1.6を達成するためには、加工プロセスや工具選定、加工条件の最適化が必要です。以下の工夫が推奨されます。
- 加工プロセスの最適化: 工程ごとに適切な条件を設定し、段階的に精度を高めます。
- 工具選定: より精度の高い工具を使用することで、表面粗さを均一に保ちます。
- 加工速度や切削条件の最適化: 適切な加工速度や条件設定を行い、表面粗さを一定に保つことができます。
切削条件と表面粗さの関係
切削速度や送り速度を調整することで、POM材の表面粗さをコントロールできます。以下の要素が表面仕上げに影響します。
要素 | 説明 |
---|---|
切削速度 | 高速で切削すると滑らかな仕上がりになります |
送り速度 | 送り速度の調整により表面粗さをコントロール可能 |
条件設定 | 適切な切削条件を設定することで目指す表面粗さが実現可能 |
切削条件の調整による表面粗さのコントロール
切削条件の調整は、表面粗さの最適化に非常に重要です。以下のポイントに注意し、最適な条件を設定することが求められます。
低速切削: 低速で切削すると、粗い表面が残りやすいため、加工の精度を確保するには適切な速度設定が必要です。
高速切削: 高速で切削すると、表面が滑らかになりやすいですが、工具の摩耗が早くなる可能性もあります。
POMフライス加工の表面仕上げ
フライス加工の基本
POM材のフライス加工における表面粗さの管理は、製品品質に直接影響します。下記の要素が重要な役割を果たします。
要素 | 説明 |
---|---|
表面粗さの重要性 | 表面粗さを適切に管理することで、製品の見た目や性能、品質が安定します。 |
加工の影響 | 表面粗さが均一であれば、摩擦や摩耗を低減し、製品の耐久性を向上させます。 |
精度の要求 | 高精度な部品には均一な表面粗さが必須です。 |
表面粗さの重要性
- 表面粗さ管理: これにより製品の見た目や性能、品質が向上し、長期的に安定します。
- 摩擦・摩耗の低減: 均一な表面粗さは摩擦を低減させ、部品の耐久性を向上させます。
加工の影響
- 表面粗さが均一であれば、摩擦や摩耗が抑えられ、品質が安定します。
精度の要求
- 高精度な部品(例:自動車部品)では、表面粗さの均一性が極めて重要です。
フライス加工での表面粗さの重要性
POM材のフライス加工時において、以下の要素が表面粗さの均一化に影響します。
要素 | 説明 |
---|---|
表面粗さの均一化 | 均一な表面粗さが確保されることで、摩擦が最適化され、動作が滑らかになります。 |
加工速度と送り速度 | 適切な速度の選定が、表面粗さの均一化に寄与します。 |
工具の選定 | 高精度な表面仕上げには適切な工具が必要です。 |
表面粗さの均一化
- 均一な表面粗さは摩擦を減少させ、滑らかな動作を提供します。特に機械部品では重要です。
加工速度と送り速度
- 加工速度や送り速度の最適化により、表面粗さを均一に保ちながら精度高い仕上がりが得られます。
工具の選定
- 仕上がりに高精度が求められる場合、適切な工具選定が重要です。
POMフライス加工における表面仕上げの課題
POM材のフライス加工時に直面する課題と、それに対する対策は以下の通りです。
要素 | 説明 |
---|---|
表面粗さの課題 | POM材は加工中に熱膨張や変形が起こりやすく、表面粗さに影響を与えます。 |
切削条件の設定 | 適切な切削速度や切削量の選定が必要です。 |
冷却方法の選定 | 過熱を防ぐため、適切な冷却方法を選定することが求められます。 |
表面粗さの課題
- POMは熱膨張しやすく、加工中に表面が荒れることがあります。これを防ぐためには適切な加工条件が必要です。
切削条件の設定
- 切削速度や切削量を適切に設定し、表面粗さを均一に保つことが重要です。
冷却方法の選定
- 冷却剤を適切に使用し、POM材の過熱を防ぐことで加工精度が向上します。
表面仕上げに関する課題と対策
POM材のフライス加工における表面仕上げを向上させるための具体的な対策を紹介します。
- 切削条件の最適化
- 切削速度や送り速度を適切に調整し、均一で滑らかな仕上げを実現します。
- 振動の抑制
- 加工中の振動を抑えることで、表面仕上がりの精度が向上します。
- 冷却方法の改善
- 適切な冷却方法を使用し、POM材の過熱を防ぐことで、より精度の高い仕上げを得られます。
表面仕上げを向上させる工夫
POM材のフライス加工で表面仕上げを向上させるためには、工具の選定、加工技術の向上、成功事例の活用が重要です。
要素 | 説明 |
---|---|
工具の選定 | 高品質な仕上がりを求めるためには、適切な工具選定が必要です。 |
加工技術の向上 | 最新の加工技術や方法を取り入れることで、仕上がりが向上します。 |
成功事例の活用 | 他社の成功事例を参考にすることで、効率的な加工方法を見つけることができます。 |
工具の選定
- 高品質な仕上がりには、超硬工具や特殊コーティング工具を使用することが有効です。
加工技術の向上
- 新しい技術を積極的に取り入れ、加工精度を向上させることが品質向上に繋がります。
成功事例の活用
- 他社の成功事例を参考にし、効率的な加工方法や条件を取り入れることで、表面仕上げが向上します。
表面仕上げを向上させるための工夫
POM材のフライス加工における表面仕上げを向上させるために、以下の工夫が役立ちます。
積極的な工夫の導入: 成功事例を参考にし、実験を重ねることで、より高い品質の製品を生み出せます。
加工方法の見直し: 最新技術を取り入れ、加工条件を最適化することで仕上がりが向上します。
樹脂・プラスチック製品の面粗度
面粗度の重要性
樹脂・プラスチック製品における面粗度は、製品の耐久性や機能性に直結する重要な要素です。以下の要素により、面粗度が製品性能に与える影響が明確に理解できます。
要素 | 説明 |
---|---|
表面粗さの影響 | 表面粗さが適切でないと、製品の耐久性や機能性に悪影響を与える可能性があります。 |
POM材の特性 | POM材は摩擦に強い特性がありますが、表面が荒れると摩耗が進みやすくなります。 |
加工工程 | 適切な工具や技術を用いて表面粗さをコントロールすることが重要です。 |
表面粗さの影響
- 耐久性への影響: 不均一な表面は摩耗を進行させ、製品寿命を縮めます。
- 機能性への影響: 表面粗さが不適切な場合、部品間で摩擦が増し、機械の効率が低下します。
POM材の特性
- POMは摩擦に強い材料ですが、表面が粗いと摩耗が進みやすくなるため、表面粗さの管理が重要です。
加工工程
- 表面粗さを制御するためには、適切な加工方法や工具の選定が欠かせません。
表面粗さ管理の重要性
POM材の加工において、表面粗さを正確に制御することが品質や機能性に大きく影響します。以下の要素で管理することが理想的な仕上がりを実現します。
要素 | 説明 |
---|---|
切削速度の選定 | 適切な切削速度を選ぶことで、表面粗さを均一に保つことができます。 |
刃先形状の選定 | 刃先の形状により、仕上がりが大きく変わります。 |
加工工程の最適化 | 加工中の振動や熱の影響を抑え、安定した仕上がりを実現します。 |
切削速度の選定
- 切削速度が速すぎると、表面が荒れることがあります。適切な速度で加工を行うことが重要です。
刃先形状の選定
- 刃先の形状が仕上がりに大きな影響を与えます。高精度な刃先を使用することで、より良い仕上がりが得られます。
加工工程の最適化
- 加工工程を最適化し、振動や熱を抑えることで、より精密で均一な仕上がりを得られます。
樹脂製品における面粗度の特徴
樹脂製品では、表面粗さの管理が製品の見た目や性能に直結します。以下の要素で表面粗さの改善が可能です。
要素 | 説明 |
---|---|
表面粗さの制御 | 適切な表面粗さのコントロールにより、製品の見た目や性能が向上します。 |
工具選定 | 適切な工具選定により、表面仕上がりが改善されます。 |
仕上げ工程の工夫 | 適切な仕上げ工程を取り入れることで、より美しい仕上がりを実現可能です。 |
表面粗さの制御
- 適切な表面粗さのコントロールによって、製品の品質や機能性を向上させることができます。
工具選定
- 切削工具や研磨工具の選定が仕上がりに直結するため、最適な工具を選ぶことが重要です。
仕上げ工程の工夫
- 仕上げ工程を工夫することで、製品の外観を向上させ、性能を最適化することができます。
表面粗さの管理と品質向上
POM材の表面粗さを適切に管理することで、製品の品質向上や耐久性の向上が期待できます。以下の方法で理想的な仕上がりを実現できます。
- 加工方法: 最適な加工方法を選択し、表面を均一に仕上げることが重要です。
- ツール選定: 高精度な工具を選ぶことで、仕上がりが向上します。
- 仕上げ工程: 仕上げ工程を改善することで、最終的な品質を大きく向上させることができます。
面粗度を改善する方法
POM材の表面粗度を改善するためには、以下の方法を組み合わせることが効果的です。
要素 | 説明 |
---|---|
表面粗さの改善 | 均一で滑らかな仕上がりを追求し、表面粗さを改善します。 |
適切な工具の選定 | 研磨や研削作業を行うことで、表面粗さを効果的に改善できます。 |
加工方法の選定 | POM材の特性に合わせた加工方法を選定することが重要です。 |
表面粗さの改善
- 均一で滑らかな表面を追求し、摩耗や摩擦を抑えることができます。
適切な工具の選定
- 研磨や研削作業を適切に行うことで、表面粗さを大幅に改善できます。
加工方法の選定
- POM材の特性を考慮し、適切な加工方法を選定することで、仕上がりが大きく向上します。
表面粗度改善の具体的な方法
POM材加工における表面粗度を改善するためには、適切な工具や技術を使用し、研磨作業を行うことが効果的です。具体的な方法としては、以下のようなものがあります。
加工方法の最適化: POM材の特性に合わせた加工方法を選択することで、優れた仕上がりが得られます。
適切な研磨工具の使用: 高精度な研磨工具を使用し、仕上がりを改善します。
プラスチック加工の基礎知識
加工方法の種類と特徴
加工方法 | 特徴 |
---|---|
切削加工 | 刃物の刃先形状や回転数、進行速度が表面粗さに影響を与えます。高品質な加工には適切な制御が必要です。 |
旋盤加工 | 切削速度や刃の形状を選択することで、表面の仕上がりを向上させることができます。 |
フライス加工 | 適切な切削条件や工具選定が重要で、表面粗さに影響を与えます。冷却剤や振動対策も影響します。 |
表面粗さと加工方法
POM材の加工において、表面粗さは加工方法によって異なります。理想的な表面仕上げを実現するためには、加工方法の選定とその特徴を理解することが重要です。例えば、切削加工や旋盤加工では、刃物の状態や切削条件が表面粗さに直接影響します。
加工における材料選定のポイント
要素 | 説明 |
---|---|
材料選定 | 適切な材料を選定することで、加工の精度や仕上がりが向上します。 |
加工条件 | 適切な切削速度や刃の形状を選ぶことが、理想的な表面粗さの実現に寄与します。 |
工具選定 | 適切な工具を使用することで、表面粗さをコントロールし、加工品質を向上させます。 |
理想的な表面粗さを追求する方法
POM材加工においては、表面粗さを適切に管理することが重要です。加工方法や工具の選定を適切に行うことで、製品の見た目や機能性を向上させることができます。旋盤加工や切削加工においては、切削速度や刃物の形状が鍵となります。
加工精度を左右する要因
要素 | 説明 |
---|---|
加工方法 | 使用する加工方法によって、表面粗さが大きく異なります。 |
工具の状態 | 適切な工具の選定と維持が、表面粗さの管理に影響を与えます。 |
切削速度 | 適切な切削速度の設定が、表面粗さに直結します。 |
定期的な検査 | 加工中の表面粗さの変化を把握するために、定期的な検査や調整が必要です。 |
表面粗さの管理と品質向上
POM材の加工において表面粗さを適切に管理することで、高品質な製品を生産することが可能です。加工方法や工具の選定、定期的な調整が表面粗さの改善に寄与し、製品の品質向上に繋がります。
理想的なPOM材表面粗さへの道
加工技術の選定と最適化
要素 | 説明 |
---|---|
加工技術の選定 | POM材加工には、フライス加工や旋盤加工などがあり、それぞれの技術に応じた表面粗さの管理が必要です。 |
切削条件 | 高速切削や適切な切削速度を選ぶことで、理想的な表面粗さを実現します。 |
工具の選定 | 刃先の形状や材質が表面粗さに影響するため、POM材に適した工具を選定することが重要です。 |
理想的な表面粗さを実現するための方法
POM材の表面粗さを理想的にするためには、加工技術の選定と最適化が重要です。具体的には、フライス加工や旋盤加工などの技術を選び、その特性に合わせた切削条件を設定する必要があります。例えば、高速切削や適切な刃先形状を選ぶことで、理想的な表面仕上がりを得ることが可能です。
表面粗さを最適化するための加工条件
要素 | 説明 |
---|---|
切削速度 | 適切な切削速度を設定することで、表面粗さを最適化します。 |
刃の形状 | 刃の形状や材質が表面粗さに影響するため、適切な形状を選ぶことが重要です。 |
冷却と潤滑 | 適切な冷却と潤滑が、熱や摩擦による悪影響を防ぎ、表面の質を向上させます。 |
加工条件による表面粗さの最適化
表面粗さを最適化するためには、切削速度や刃の形状、冷却と潤滑の管理が重要です。適切な切削速度や刃の状態を保つことで、POM材の表面を滑らかに仕上げることができます。また、過剰な熱や摩擦を防ぐために、適切な冷却や潤滑も必要です。
継続的な品質改善のためのアプローチ
要素 | 説明 |
---|---|
加工方法の改善 | 常に最新の加工技術や方法を導入し、品質の向上を図ることが必要です。 |
工具の定期点検 | 定期的に工具の状態を点検し、磨耗や劣化に対処することで、加工精度を保つことができます。 |
温度管理 | 適切な加工温度の管理が、表面粗さや品質に影響を与えるため、注意が必要です。 |
継続的な品質向上のための工夫
POM材加工において、理想的な表面粗さを維持するためには、継続的な品質改善が不可欠です。加工方法や工具の選定を見直し、適切な温度管理や切削条件を調整することで、品質の向上を図ります。これにより、製品の外観や機能性が向上し、顧客満足度も高まるでしょう。